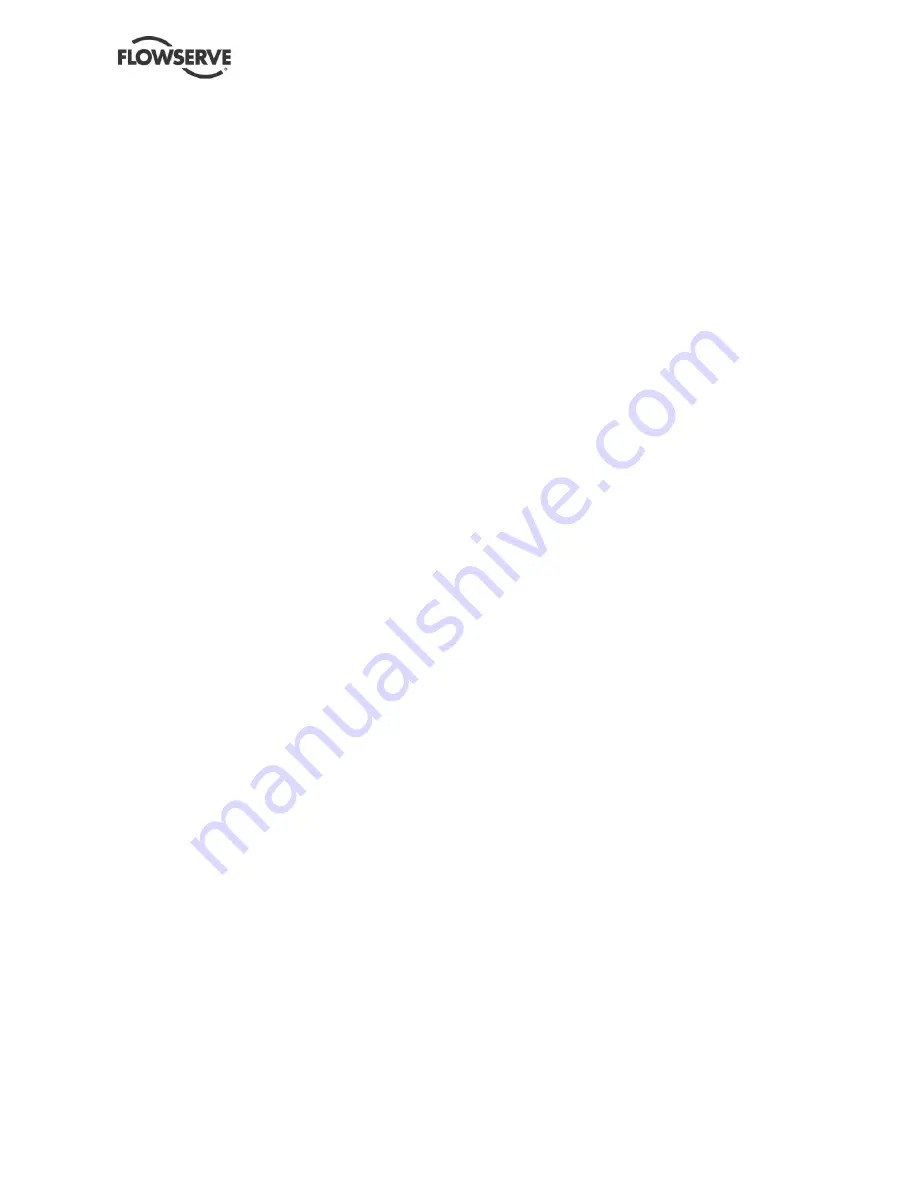
WIK USER INSTRUCTIONS ENGLISH BO2662 5/09
Page 55 of 76
5) Using same method as was observed in step
2 above, tack weld bushing using welding wire
and gas-tungsten arc or install set screws in
bushing and parent part. Stake set screws.
6.8.2.5 Casing cover
Before assembling the casing cover [1221],
inspect the following:
1) Remove any traces of old gaskets from the
parting surfaces of casing cover [1221], casing
[1100], discharge spacer casing diffuser
[1140], and inner head gasket disc spacer
[3645].
2) Check discharge spacer casing diffuser [1140],
balance drum bushing [1600], and casing
cover [1221] for damage or corrosion that
might impair efficient operation; additionally,
check parting surfaces of casing [1100] and
casing cover [1221] for damage that could
affect sealing.
3) Verify correct running clearance between
balance drum bushing [1600] and balance
drum [6230] (see section 6.8.2.7.2 below).
6.8.2.6 Case End Plate
Before installing the case end plate [9322], inspect
the following:
1) Remove any traces of old gasket form the
parting surfaces of the case end plate [9322]
and the case [1100].
2) Check case end plate [9322] for damage or
corrosion that might impair efficient operation,
and check parting surfaces of case end plate
[9322]and case [1100] for damage which
might affect sealing.
6.8.2.7 Internal assembly
Before assembling the internal assembly, inspect
the following:
6.8.2.7.1
Visual Inspection
To perform a good visual inspection and to obtain
the highest degree of cleanliness, which is
essential to the balance of the rotating parts and
the correct fit of all internal parts (rotating and
stationary) ensure that all parts are disassembled,
including all those on the shaft. The visual
inspection consists of examining these parts for
those conditions that commonly impair operation.
Parts and conditions are listed below. Where
corrective action may not be apparent to a
journeyman millwright or a more extensive
examination is required, the inspection item is
cross-referenced to a detailed procedure. Inspect:
1) Shaft [2100] for scratches, nicks, burrs, and
distortion; absolutely smooth surfaces and a
straight shaft are required (see section
6.8.2.7.3 below).
2) All internal castings (intermediate covers,
impellers, etc.) for erosion and other damage
such as nicks, gouges and cracks must be
corrected before final assembly.
3) Dowels for distortion, cracks, burrs, and
proper fit; dowel holes for damage and elliptic
shape.
4) Abutting faces and running surfaces of
impeller hubs and skirts, shaft sleeves,
pressure reducing sleeve, wearing rings,
bushings, all internal castings, for nicks, burrs,
scratches and scouring-concentric and
absolutely smooth surfaces are required.
5) Pressure reducing sleeve/bushing, wearing
rings, and bushings for excessive wear (see
section 6.8.2.7.2 below).
6) Impeller bores and pressure reducing sleeve
bore for correct fit with shaft (see section
6.8.2.7.4 below).
7) Impeller hub and skirt for roundness by taking
micrometer readings of their diameters at 90
degree intervals. For corrective action (see
section 6.8.2.7.6 below).
8) Split rings and shoulder ring for burrs, nicks
and gouges.
9) O-ring grooves in shaft sleeve for nicks, burrs,
and scratches-absolutely smooth surfaces are
required.
10) Rotating assembly for nominal concentricity
(see section 6.8.2.7.5 below).
6.8.2.7.2
Checking Running Clearances
Actual running clearance is determined by
measuring the inside diameter of the stationary
part and the outside diameter of the rotating part
and taking the difference. Measurements should
be taken with a micrometer and each part should
be checked for trueness or roundness by taking
diametrical readings 90 degrees apart. To where
replacement of a part is advisable, compare the
actual clearance with the design clearance that is
listed under section 10.3, then, consider the wear
(that is, actual clearance minus design clearance)
with respect to the general statement under
section 10.3 concerning restoration of mechanical
and hydraulic efficiency and decide whether to
restore design clearance. Before final assembly,
the trueness and the running clearance of the
following should be checked:
1) Balance drum [6230] and bushing [1600];
replace parts if running clearance exceeds the
recommendation under section 10.3 or parts
do not run true. Since the parts are designed
with a specific area for balancing hydraulic