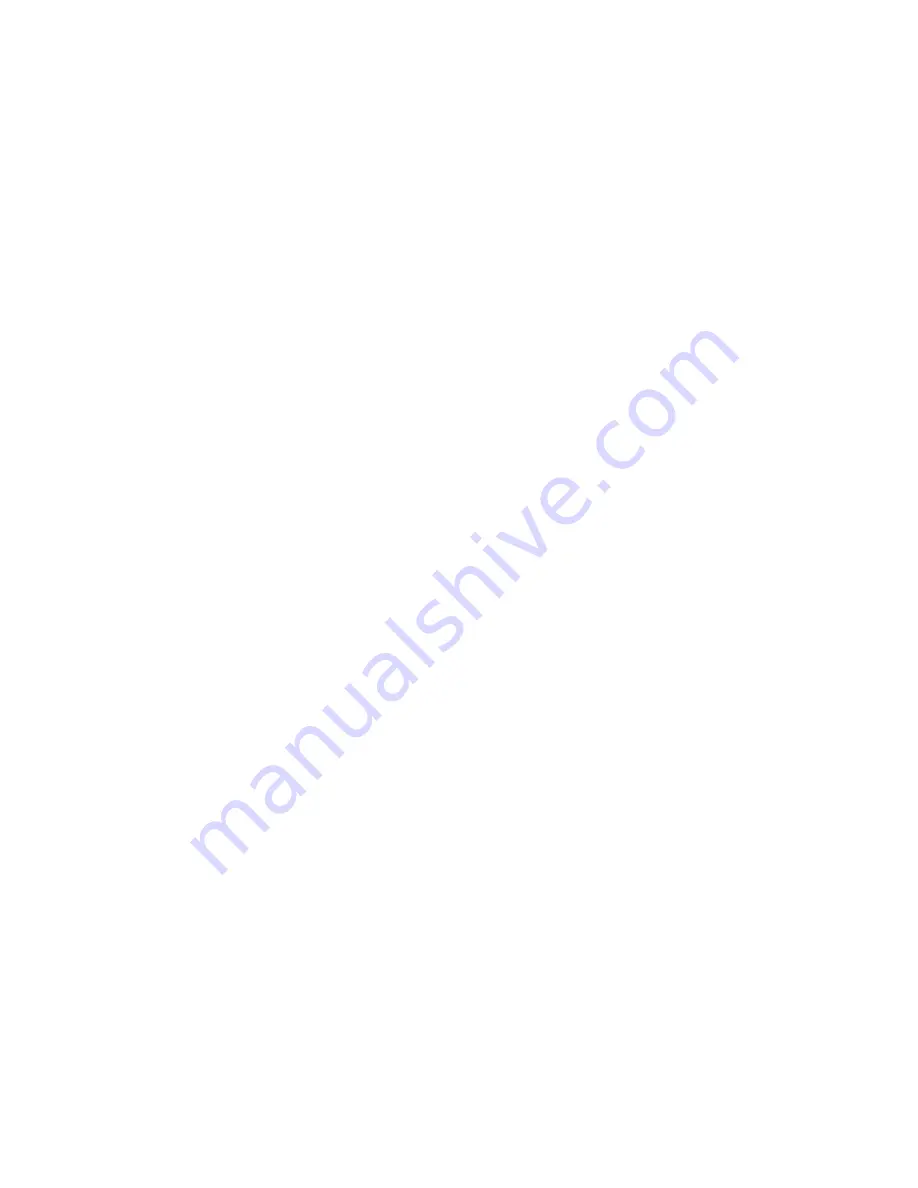
Flowserve Corporation, Valtek Control Products, Tel. USA 801 489 8611
48-7
rate calibration equipment of
±
0.1 percent of
span should be used. The pressure gauge port is
1
/8-inch NPT. Calibration manifolds are available
from the factory (Part No. 97370).
1. Connect I/P module to a supply pressure between
30 to 150 psi.
2. Remove I/P module housing cover. (See Figure 9.)
WARNING: Be certain power to I/P module is
disconnected before removing housing cover in
explosive atmospheres; otherwise personal in-
jury may occur.
3. Before adjusting the zero and span, be certain the
MPC feature is disabled. Refer to Step 7 in the
‘Adjusting the Minimum Pressure Cutoff Feature’
section.
4. Connect a current source to terminal block on
circuit board.
NOTE: The zero and span adjustments are multi-
turn potentiometers (pots) and have no stops on
the ends of their travel; however, they have a slip
clutch to prevent damage from over-adjustment.
The pots also make a clicking noise when they
have reached adjustment limits.
5. Apply a 4.0 mA signal to the input. Locate and
adjust zero trim pot to achieve a 3.0 psi output. The
output will increase with clockwise rotation of the
zero trim pot. If calibrating an I/P module with a 10-
50 mA input signal, apply a 10.0 mA signal to input.
6. Increase input signal to 20.0 mA (50 mA for 10-50
mA units). Locate and adjust span trim pot to
achieve a 15.0 psi output. The output will increase
with clockwise rotation of the span.
7. Recheck zero setting by repeating Step 5. The span
adjustment may affect zero setting.
8. Repeat Steps 5, 6 and 7 until proper adjustments
are obtained.
Adjusting Minimum Pressure Cutoff
Feature
The XL90 positioner with I/P Transducer has a ‘Mini-
mum Pressure Cutoff’ (MPC) feature, which allows the
user to set the positioner. When the input signal falls
below a user-adjustable current, the pressure output
falls rapidly to approximately 1.7 psi, causing the valve
to move to the failure position. This feature is generally
used when the service requires a tight shut off or to
prevent throttling near the valve seat. To adjust this
feature, refer to Figure 9 and perform the following:
NOTE: The following procedure applies only when
the minimum pressure cutoff feature will be used.
NOTE: The zero and span settings of both the
positioner and I/P transducer should be verified
as accurate before the minimum pressure cutoff
feature is enabled and adjusted.
1. Connect the I/P module to a 30 to 150 psi air supply
pressure.
2. Remove the I/P module housing cover.
WARNING: Be certain power to the I/P module is
disconnected before removing the housing
cover in explosive atmospheres; otherwise per-
sonal injury may occur.
3. Connect an adjustable current source to the termi-
nal block on the circuit board. Apply the desired
input signal to the positioner at which the output
pressure is to fall to approximately 1.7 psi. This
signal can range from factory setting of 3.7 to 8 mA.
4. Turn the minimum pressure cutoff pot clockwise
until the output pressure drops off.
5. Fine-tune the pressure drop-off point by increasing
the input signal and then decreasing it through the
desired shut-off signal. Observe the signal value at
which the pressure drops off. If the pressure drops
off at a lower mA signal than desired, turn the MPC
pot counterclockwise. If the pressure drops off at a
higher signal than desired, turn the tight shut-off
screw clockwise.
6. Repeat Step 5 until the pressure drops off at the
desired input signal.
7. To disable the MPC feature turn the minimum
pressure cutoff pot (marked “MPC”) 20 turns coun-
terclockwise or until it makes a clicking noise.
Positioner Maintenance
NOTE: Refer to NT 3000 IOM for I/P module
maintenance instructions.
For proper maintenance, proceed as follows:
1. Maintain a clean air supply, free of dust, oil and
water. A coalescing air filter for I/P is required to
ensure a clean air supply. Check and maintain filter
regularly.
2. Make sure all arms and levers move freely.
3. Check for loose parts.
4. Be sure there are no leaks in the air supply tubing,
fittings or connections.
5. Refer to the troubleshooting chart on page 12 in
case of problems.
Pilot Relay Disassembly and Reassembly
The pilot relay is available as a complete unit and can
be easily replaced (See Steps 2 and 18.) Before at-
tempting to correct any problem with the pilot relay
assembly, obtain a positioner repair kit that contains the
soft goods most commonly required.
NOTE: Numbers in parentheses correspond to
the numbers in Figure 16.
1. Remove the feedback spring (47) and rotate the
span and zero arms (40, 46) out of the way.