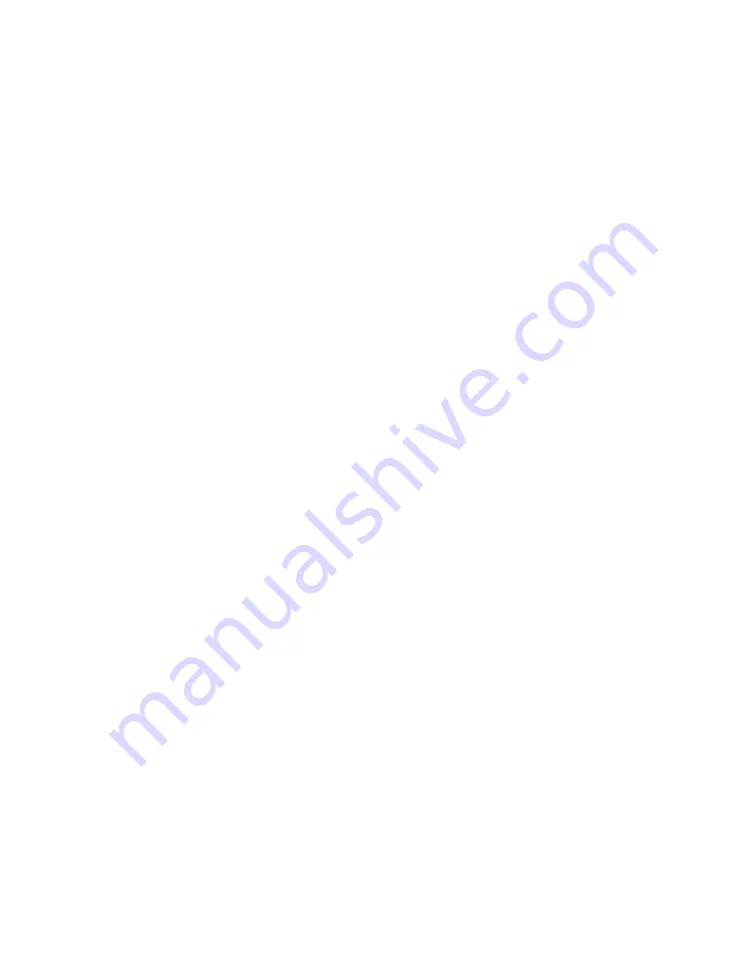
•
vibrations in the calibration environment should be minimized
•
altitude less than 2,000 meters
•
indoor use only
If the unit is operating at temperatures above 600°C, cooling coils are accessi-
ble on the rear of the chassis to prevent the furnace heat from loading down the
room air conditioning system. (See
Section 3.4
Plumbing)
8