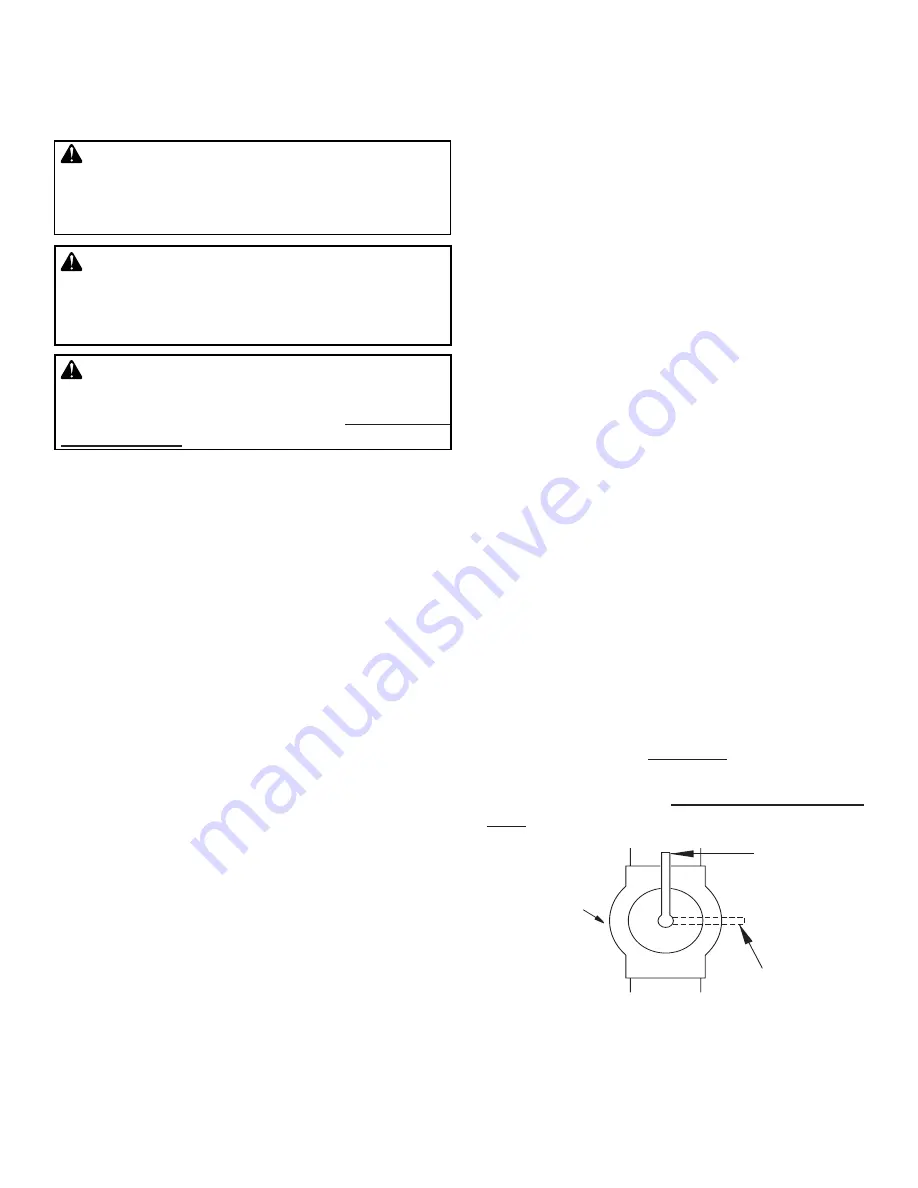
www.fmiproducts.com
125883-01C
7
INSTALLATION
Continued
CHECKING GAS CONNECTIONS
WARNING: Test all gas piping and connec-
tions, internal and external to unit, for leaks
after installing or servicing. Correct all leaks
at once.
WARNING: Never use an open flame to
check for a leak. Apply a noncorrosive leak
detection fluid to all joints. Bubbles forming
show a leak. Correct all leaks at once.
CAUTION: Make sure external regulator has
been installed between propane/LP supply and
appliance. See guidelines under
Connecting
to Gas Supply
, page 6.
PRESSURE TESTING GAS SUPPLY PIPING
SYSTEM
Test Pressures In Excess Of 1/2 PSIG (3.5
kPa)
1. Disconnect appliance with its appliance main gas
valve (control valve) and equipment shutoff valve
from gas supply piping system. Pressures in ex-
cess of 1/2 psig will damage appliance regulator.
2. Cap off open end of gas pipe where equipment
shutoff valve was connected.
3. Pressurize supply piping system by either open-
ing propane/LP supply tank valve for propane/LP
gas or opening main gas valve located on or near
gas meter for natural gas or using compressed
air.
4. Check all joints of gas supply piping system. Ap-
ply noncorrosive leak detection fluid to all joints.
Bubbles forming show a leak.
5. Correct all leaks at once.
6. Reconnect appliance and equipment shutoff
valve to gas supply. Check reconnected fittings
for leaks.
Test Pressures Equal To or Less Than 1/2 PSIG
(3.5 kPa)
1. Close equipment shutoff valve (see Figure 4).
2. Pressurize supply piping system by either open-
ing propane/LP supply tank valve for propane/LP
gas or opening main gas valve located on or near
gas meter for natural gas or using compressed
air.
3. Check all joints from gas meter to equipment
shutoff valve for natural gas or propane/LP
supply to equipment shutoff valve for propane/
LP. Apply noncorrosive leak detection fluid to all
joints. Bubbles forming show a leak.
4. Correct all leaks at once.
PRESSURE TESTING APPLIANCE GAS
CONNECTIONS
1.
Open equipment shutoff valve (see Figure 4).
2. Open main gas valve located on or near gas
meter for natural gas or open propane/LP supply
tank valve.
3. Make sure control knob of appliance is in the
OFF position.
4. Check all joints from gas meter to equipment
shutoff valve for natural gas or propane/LP supply
to equipment shutoff valve for propane/LP. Ap
-
ply noncorrosive leak detection fluid to all joints.
Bubbles forming show a leak.
5. Correct all leaks at once.
6. Light appliance (see
Operation
, page 15). Check
all other internal joints for leaks.
7. Turn off appliance (see
To Turn Off Gas to Appli-
ance
, page 15).
Figure 4 - Equipment Shutoff Valve
Open
Closed
Equipment
Shutoff
Valve