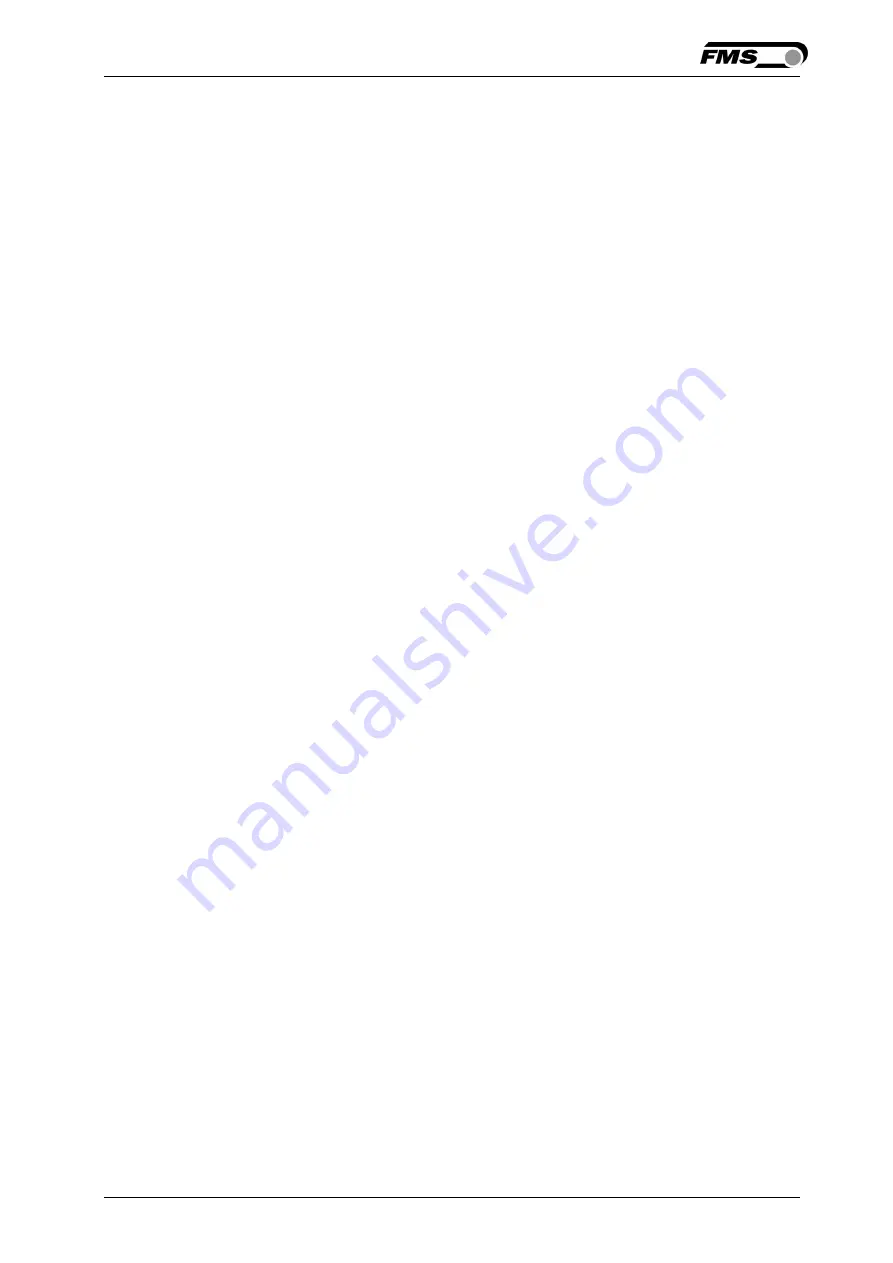
Operating Manual BKS015
26.11.2018
7
Refer to Fig. 21 for the mechanical dimensions and mounting holes of the
BKS015.EIP.
2.
Check your system requirements such as:
–
Desired guiding form (edge or centre guiding)
–
Supply conditions
3.
Draw the wiring diagram for your configuration (ref. to 4.3 “Connecting the
BKS015.EIP“ and chapter 4.4 “
Connector and Screw Terminal Arrangement”
)
4.
If required, determine special parameters (ref. to 7.1 “Description Operation
Parameters”)
3.2
Installation Procedure
1.
Mount and ajust your material sensor(s) to the steering frame (ref. to chapter 4.2)
2.
Mount the web guide to the machine frame
3.
Connect the sensor(s) to the electronic unit.
4.
Make sure the power supply voltage is in the range 18 to 36V DC (Vnom= 24V)
5.
Power your system on
6.
If required, make additional settings (ref. to chapters 8.6 and 8.7)