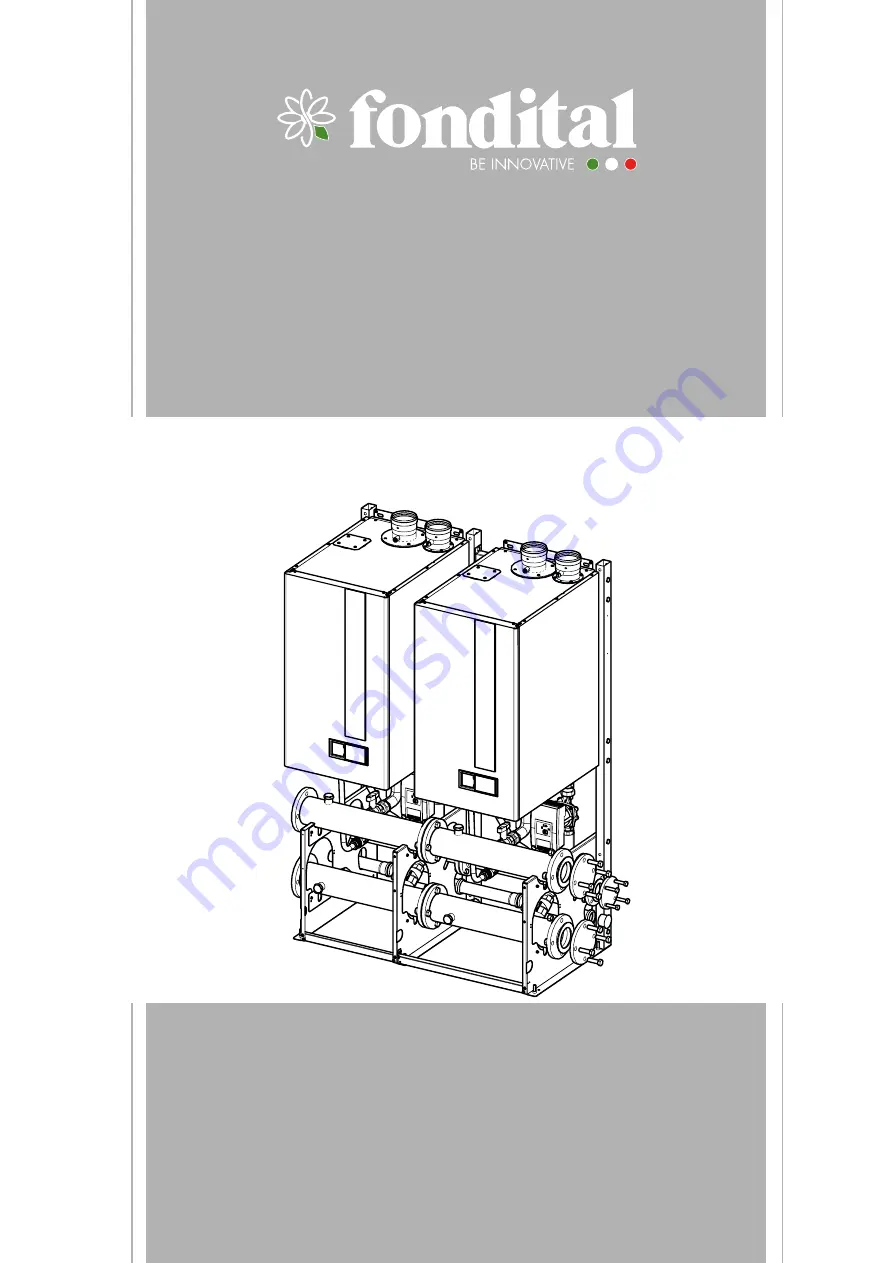
IST 03 C 1321 - 02
MODULAR HEAT GENERATORS
ITACA CH KR
MODULE ON FRAME
INDOOR INSTALLATION ONLY
INSTALLATION, USE
It is compulsory to read this manual before proceeding with the product installation, use and
maintenance operations.
This system is intended for production of hot technical water only:
• For heating of residential, commercial and industrial rooms.
• For heating of industrial process water.
• For indirect production of domestic hot water.
Any other use is forbidden.
EN