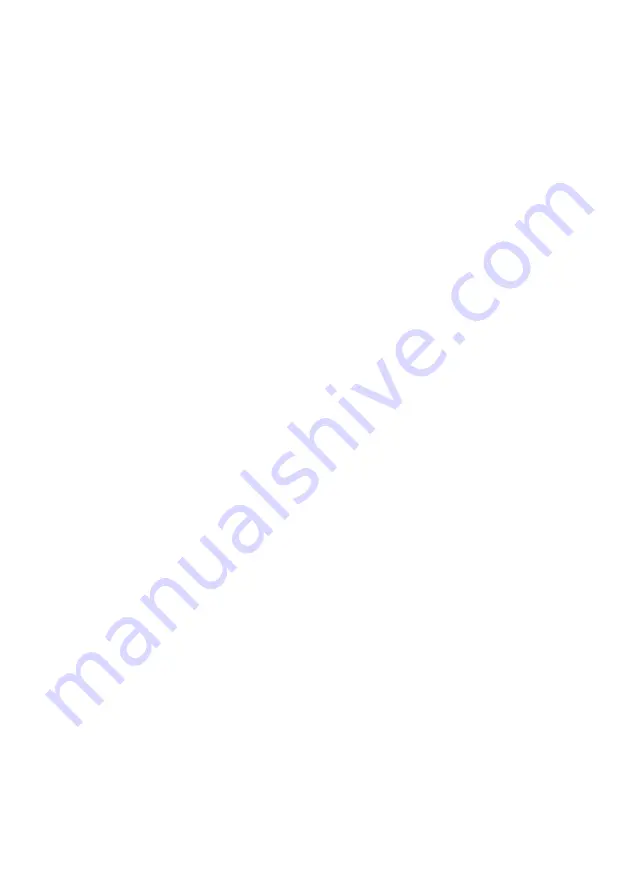
■
Marking of the device has to be always easily legible.
■
Pneumatic tools may only be operated and serviced by trained personnel.
■
Repairs are to be executed only by authorised persons.
■
No manipulations, emergency repairs or usage for purposes other than intended are allowed
for pneumatic tools
■
Do not reach into the working area when working with pneumatic tools.
■
If leakage or other malfunctions occur, the device must be disconnected immediately from
the compressed air source and the failure cause has to be fixed.
■
Never use quick-coupling systems directly at the unit. There has to be at least a 20cm hose
separating the quick-coupling system from the device.
■
Tool attachments like e.g. chisel, needles, socket wrench inserts etc. may only be replaced
when the compressed air hose is disconnected.
■
For lubricating or for the replacement of tool attachments like e.g. chisel, needles, socket
wrench inserts always disconnected the compressed air hose first.
■
Always make sure that the tool attachments are in faultless condition.
■
Only use the tool attachments specific for the respective tool like e.g. chisels for chipping
hammers, grinding discs and abrasive belts for pneumatic grinding tools etc..
■
Pay attention to the reaction moment. Pay attention to reaction torques and the possible
breaking of the tool. In tight spaces the reaction torques might cause injuries. Make sure to
take countermeasures against unexpected reaction torques.
■
Permanent vibrations might be harmful for your health.
■
Ensure stability at the place you are standing.
3. Maintenance and care
The use, inspection and maintenance of pneumatic tools must always be in compliance with
local state or federal government regulations.
3.1. Maintenance
■
Always disconnect the device from the compressed air supply before carrying out mainte-
nance work.
■
For cleaning the tool or its individual parts we recommend the use of benzine.
■
Never clean with detergents or acid cleaners, esters (organic compounds from acids and
alcohol), acetone (ketone), chlorinated hydrocarbons or nitrocarbon-containing oils. Do not
use chemicals with low flashpoint.
■
Damaged or worn components such as O-rings, bearings, rotary blades etc. are to be
replaced.
■
Only the spare parts recommended by the manufacturer are to be used, otherwise the war-
ranty expires.
■
When disposing of components, lubricants or cleaning detergents make sure that the ap-
propriate guidelines for environmental protection are followed.
■
Drain the compressor tank and remove condensed water from the air hoses. Please read the
operation manual for the compressor carefully as well.
Lubricating:
■
Pneumatic tools have to be lubricated throughout their lifetime.
Motor and ball bearings need compressed air to power the tool.
As the moisture in the compressed air causes motor corrosion, the motor must be lubricated
daily. We therefore recommend using an integrated lubricator.