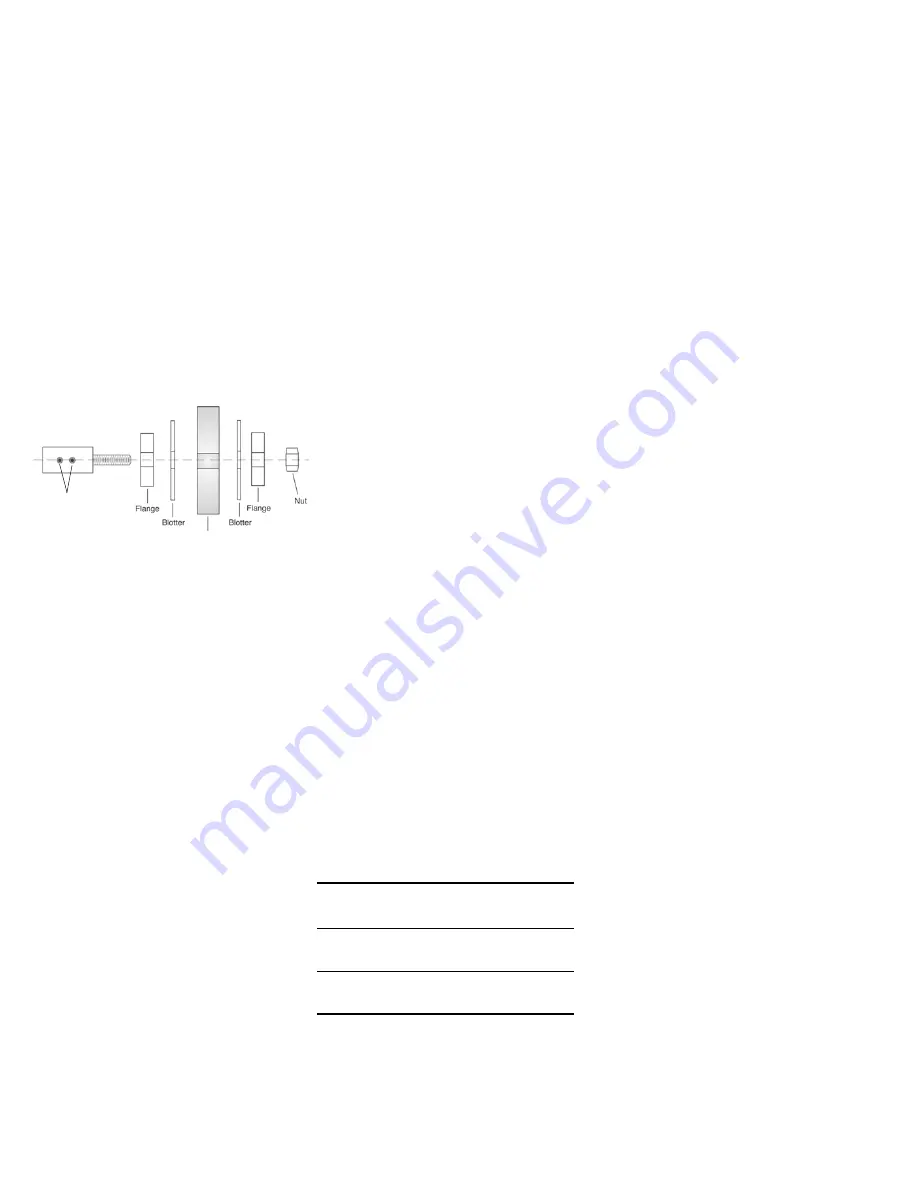
A-JCA-2 chuck arbor, A-WM6 wheel mandrel
and S.B0 Flexades
®
are right hand side
accessories, intended for use on the right
hand side of the lathe as you face it. Do not
use them on the left side as buff, wheel or
tool may unscrew under load. The supplied
A-TM5 tapered spindle and optional A-WM-5
wheel mandrel is intended for use on the left
side only. (Every spindle and mandrel is
marked with an R or L to indicate right or
left hand.)
Attach the spindles or mandrels by sliding
them onto the motor shaft until there is only
a 1/8
″
space between the motor housing and
inside edge of the spindle or mandrel. Be
sure that the two set screws line up over the
flat on the motor shaft. Tighten both screws
securely with supplied hex key.
See Figure 2 for mounting rubber wheels or
other accessories with 1/4
″
diameter center
holes on A-WM-6 wheel mandrel. Run the
lathe at slow speed without a buff (or wheel)
to see that the spindles, mandrel, or collet
holder on the lathe are running true.
Never use a buff, brush, abrasive wheel,
or any other accessory that is rated under
7,000 RPM. Never use one that appears to
wobble or vibrate. It could damage the lathe
or injure you.
Never use buffs over 4
″
in diameter.
Never use grinding wheels over 2
″
in
diameter. Never use rubber bonded wheels
over 3
″
in diameter.
Please refer to Figure 2 for the proper mount-
ing procedure for wheels or brushes on the
A-WM-6 or A-WM-5 mandrel.
Tapered Spindles: For use with 3
″
or smaller
wheels with arbor holes up to 7/16
″
cotton,
felt, and chamois buffs with shellac hardened
leather or lead centers. Also for felt inside
ring buffs mounted on wooden mandrels,
EXL Wheels, Radial Bristle Discs with A-4561
or A-4562 tapered spindle adapters.
Mounting Wheels onto Tapered Spindles:
Turn lathe on and run at low speed. Align arbor
hole of accessory with screw-like threads of
tapered spindle. The accessory will self tighten
as it travels up the spindle threads. To remove,
turn lathe off and manually unscrew your
wheel or buff.
Collet Holder: Loosen the two hex or allen
screws on A-CHA-5 Collet Holder and slide
onto exposed motor shaft of BL Lathe. Position
screws over the flat area of the shaft
and re-tighten.
Changing Collets and Accessories: A-CHA-5
Collet Holder comes with 3/32
″
, 1/8
″
and 1/4
″
collets for use with accessories and mandrels
with 3/32
″
, 1/8
″
and 1/4
″
diameter shanks. The
1/4
″
collet typically comes installed. To switch
out a collet and/or an accessory with a differ-
ent shank size, insert supplied pin with safety
spring into hole next to the two set screws.
Insert the wrench onto the flats at the tip of the
chuck nut and unscrew nut while holding pin
in place to keep spindle from turning. Remove
chuck nut and switch out collet. This may
require the use of a needle nose pliers. Replace
chuck nut and tighten after installing the
desired accessory or mandrel. Never tighten a
chuck nut without an accessory installed, as
damage to the collet may occur.
Chuck Arbor: Loosen the two hex or allen
screws on A-JCA-2 Chuck Arbor and slide onto
exposed motor shaft of BL Lathe. Position
screws over the flat area of the shaft
and re-tighten.
Changing Accessories: A-JCA-2 has a geared
3-jaw #0 chuck. Open chuck jaws as far as
necessary with key provided. Insert shank of
accessory fully into the chuck. Tighten each of
the jaws with chuck key until accessory is
secure and centered. If accessory does not
run true, reopen jaws, rotate accessory and
retighten. To release accessory, simply reopen
chuck jaws with key and pull out accessory.
The chart above shows the SFPM obtained with
different diameter wheels at various speeds.
Operation
Because of the higher maximum speed
(approxi-
mately 7,000 RPM) and variable speed control,
the Foredom Bench Lathe has several advan-
tages over conventional single or two speed
polishing and buffing lathes:
1.
The same size buffing wheel can be used to
obtain different surface speeds, as measured
in surface feet per minute (SFPM). 3
″
or 4
″
diameter buffs can provide the 1,750 to 3,450
SFPM recommended for polishing and the
3,450 and higher SFPM recommended for
buffing. The chart below shows the SFPM
obtained with different diameter buffs at vari-
ous speeds.
2.
The SFPM can be varied while using the
same diameter buff or wheel. This will give
better results on different types of material.
3.
The 7,000 RPM maximum speed will enable
you to get much higher SFPM with smaller 1
″
or 2
″
buffs or inside ring buffs, than slower
single or double speed equipment.
4.
3M Scotch-Brite™ Radial Bristle Discs in 2
″
and 3
″
diameters require 5,000 or higher RPM
or optimum performance, making them perfect
for use in the lathe.
5.
The maximum speed of 7,000 RPM is also
fast enough to permit the use of small mount-
ed abrasive points, brushes, cutters, or other
accessories in the A-CHA-5 collet holder,
S.B0-516 Flexade
®
or A-JCA-2 chuck holder.
For additional information on buffing and
polishing procedure, wheel selection, and
Foredom buffing and polishing compounds,
please refer to the Foredom Buffing and
Polishing Guide (Form No. 1234).
Maintenance
Lubrication: The Foredom Bench Lathe has
prelubricated ball bearings, a dust-proof motor
housing and does not require any lubrication.
The motor is designed to operate above room
temperature which will be warm to the touch but
not harmful to the motor.
Motor Brush Wear: Disconnect power cord
before checking for motor brush wear. Check for
motor brush wear periodically (about every 200
hours of continuous operation). Unscrew the
motor brush tube caps (located on front and
back of right side of lathe), check the motor
brush length, and install new brushes if the old
ones are less then 3/16
″
(4.7mm) in overall
length. Be sure that the radius in the end of the
brush is in line and conforms to the commutator
surface. Replacement motor brushes (MP262P)
are available from your dealer, the factory, or you
may order them from www.foredom.net.
Buff
Speed
SFPM
Diameter
1
″
Full 7,000 RPM
1,750
Med 4,000 RPM
1,000
2
″
Full 7,000 RPM
3,500
Med 4,000 RPM
2,000
3
″
Full 7,000 RPM
5,250
Med 4,000 RPM
3,000
4
″
Full 7,000 RPM
7,000
Med 4,000 RPM
4,000
Motor Shaft
set screws
Rubber
Wheel
Figure 2
Wheel Mandrel A-WM-5 and A-WM-6
Assemble all components in proper sequence.
(A-WM-5 left side wheel mandrel has same
components in opposite sequence)