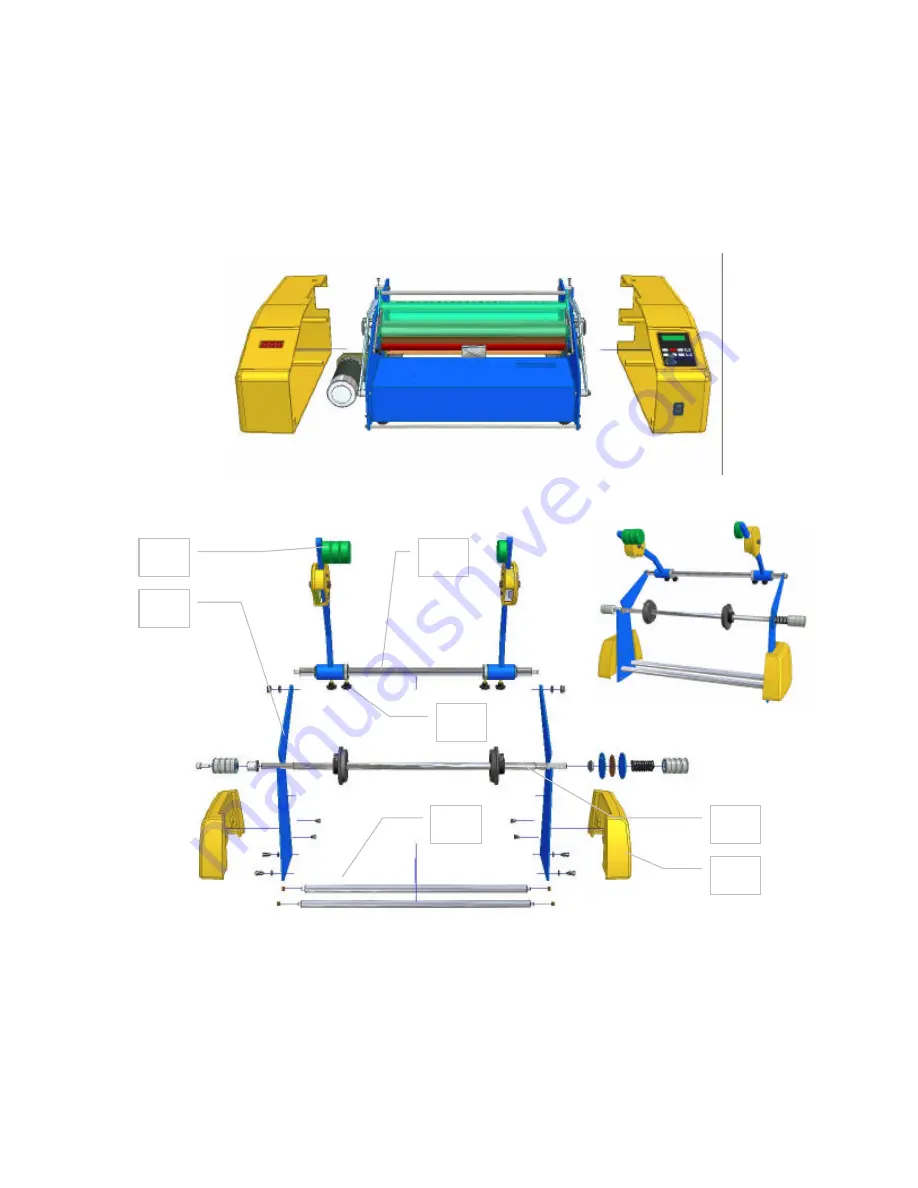
11
3.4 Installing and assembling the equipment
The equipment is shipped in a wooden pallet, partially dismantled. It is therefore necessary to
assemble the equipment before installation. Assembling the machine is an easy installation
work. The equipment must be disconnected from the power network during installation.
Installation procedure:
1.
Placing the foundation of the equipment on the working place
2.
Removing side protective covers
Figure 4
3.
Installation of the carriers of the roll with equalizing rollers
Figure 5
A) Pylon
B) Weights
C) Additional shaft
D) Arrest screws
E) Equalizing rollers
F) Carrier of the roll
G) Cover of the pylon
C
A
F
E
D
B
G
Summary of Contents for Foliant 370T
Page 2: ...2...