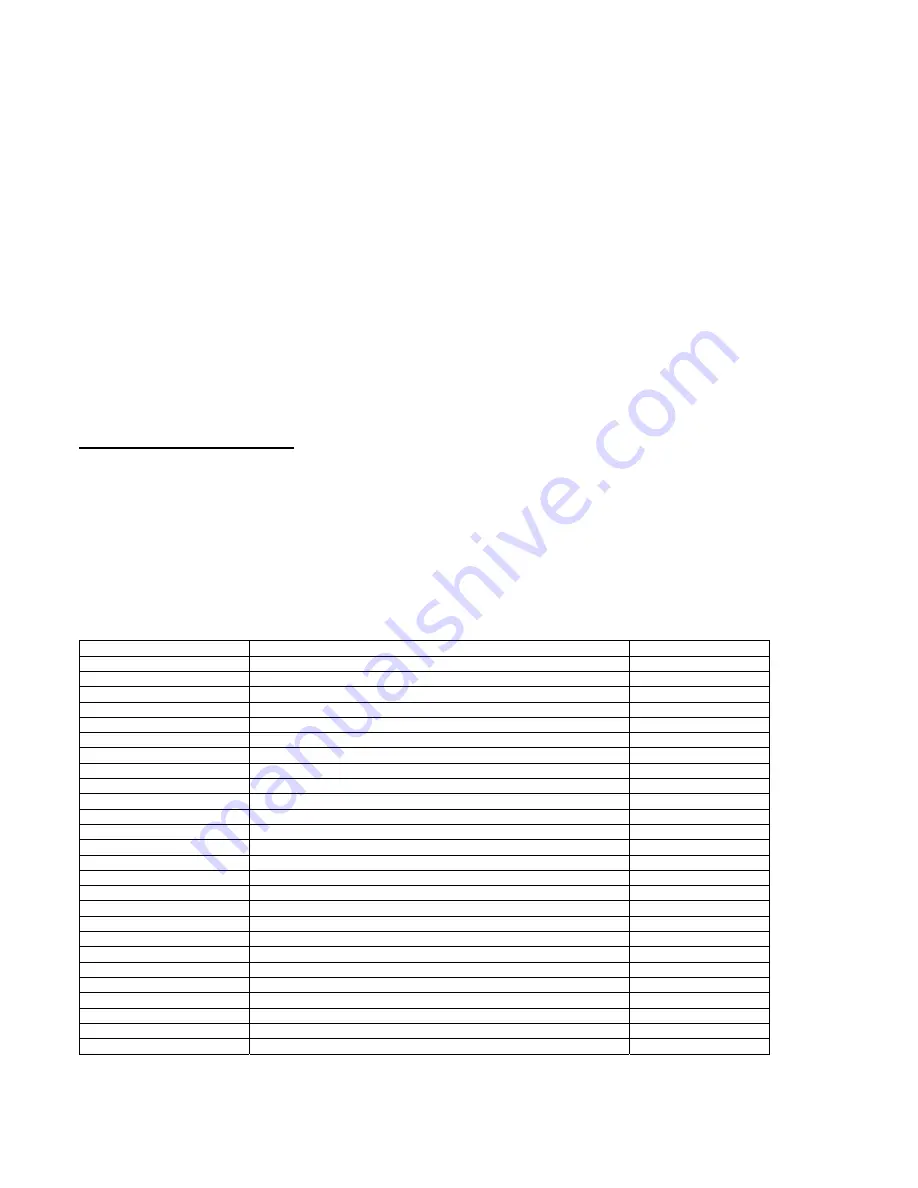
2
The controller will determine the temperature to be maintained during the hold phase based on the chilling cycle that has
been completed. If a soft or hard chill has taken place the controller will maintain an air temperature of 2°c.
The hold mode is principally intended as a temporary storage facility offering the operator flexibility until the product can
be unloaded into a longer term storage units at the correct storage temperature. On occasion this hold period may
become extended to operate overnight or to provide emergency refrigeration backup. In such instances defrosting would
automatically occur as necessary.
Model Details.
The RBC 20-60 is capable of blast chilling 60kg of product from +70°c to +3°c in 90 minutes with entry temperature up to
90°c
The cabinet is compatible with the Rational 20 rack GN 1/1 201 trolley.
Refrigerant used is R404A.
The RBC20-60 has two separate refrigeration systems comprising, two condensing units, a twin circuit condenser and a
twin circuit evaporator. (See pages 20 and 21 for assembly details and page 22 for schematic dual circuit refrigeration
layout).
The RBC20-60R has the same refrigeration systems but the condensing units are remotely sited.
Refrigerant control is by expansion valve to control the correct amount of refrigerant required to meet the demand of the
evaporator. (See page 21 for assembly detail).
The parameter ‘Capacity Enable’ is set to ‘ON’ to allow for both condensing units to be running during the chill cycle
therefore maximising the heat extraction from the product. During the ‘HOLD’ mode with the ‘Capacity Enable’ set to ‘ON’
one compressor will control the temperature throughout unless the temperature exceeds the capacity control limit.
A 1½” BSP drain outlet is fitted in to the base of the cabinet for connection to external drain.
The cabinet is delivered with the legs secured to the base of the cabinet.
Controller Technical Detail
The FCC controller is a three-piece unit made up of the Front Display and Dial Shaft Encoder, Mother Board plus
Evaporator, Food and Air temperature probes. The front display PCB and the CPU/ Switching PCB unit are
interconnected by a ribbon cable. The membrane attached to the front provides an IP rating of IP54 providing a scratch
free wipe clean finish.
The control dial is the method by which the controller is accessed for all requirements. It has three planes of movement,
clockwise, anticlockwise and inwards.
The control dial allows the operator/ engineer to move forward and backwards through various menu selections shown on
the display, and enter a desired programme. The control system will then respond appropriately either commencing the
operating cycle or allowing further configuration.
Part numbers
Item Description
Part
Number
Controller Mother Board
00-555395
Controller Shaft Encoder
00-555396
Controller LCD Display
00-555394
Air Probe P1
NTC type. 2.5m
00-555397
Evaporator Probe P2
NTC type. 2.5m
00-555397
Food Probe
5M Length
00-555663
Compressor x 2
TAJ4519ZH T 400/50
00-555885
Condenser Coil
BC6013/122
01-257300-01
Condenser Fan Assembly
S4E300-BP26-30
00-555886
Sight Glass
3/8"
15483015
Drier
00-555388
Solenoid Valve
EVR6 0
15451215
Liquid Receiver
00-555579
LP Switch
2.5 Bar 0.5 Bar Diff
00-555387
HP Switch
28 Bar – 3 Bar Diff
00-555386
High Pressure Thermostat
KP5 Auto Re-set (set at 18 BAR with a 3 BAR diff.)
15452109
Evaporator Coil
BC6013/121
01-256400-01
Expansion Valve
Valve Body TES2-NL68Z34300/68
15450386
Orifice
NO 02 68-2092/68-2072
15451104
Expansion Valve
Solder Adaptor 68-2
15450910
Evaporator Fan Motor
W4E420-CP02-66788-4-7320
00-555375
hinge Edgemount
00-555880
Door Gasket
1406x546MM
01-256387-01
Door Switch
Circular (Reed Type)
00-555829
Door Switch Magnet
Circular
00-555828
Door Handle
Edgemount Latch Kit
00-555881
Summary of Contents for BC 21
Page 1: ...RBC20 60 Blast Chiller ...
Page 24: ...23 COMPRESSOR WIRING RBC20 60 ...
Page 25: ...RBC20 60 1 of 2 Wiring Diagram 24 ...
Page 26: ...RBC20 60 2 of 2 Wiring Diagram 25 ...
Page 27: ...RBC20 60R 1 of 2 Wiring Diagram 26 ...
Page 28: ...27 RBC20 60R 2 of 2 Wiring Diagram ...
Page 29: ......
Page 30: ...2 ...
Page 31: ...3 ...