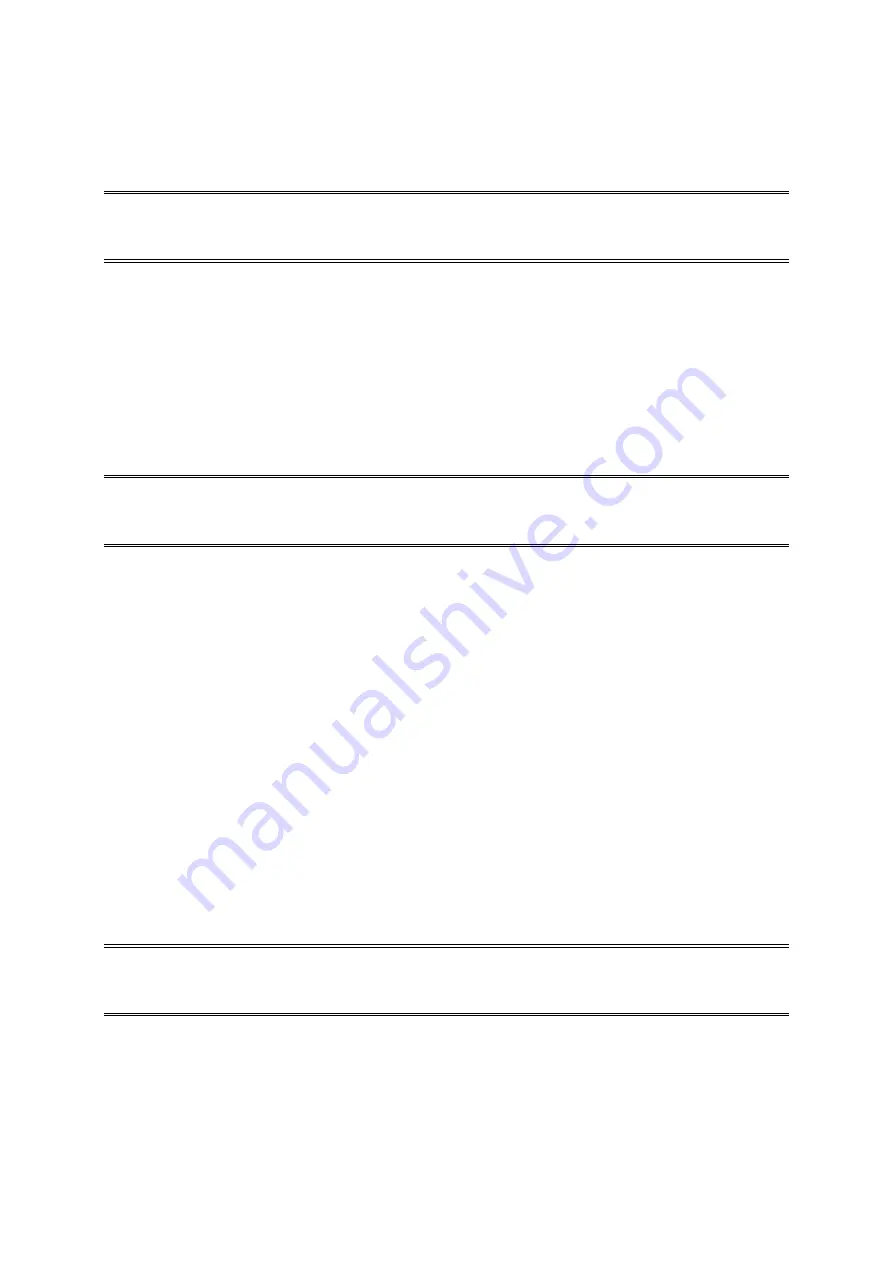
14
*
Damaged and dirty oils must always be returned to an approved reception
centre and an oil return point respectively.
CHECKS BEFORE START-UP/STARTING
Check the following before final start-up:
That the oil has been correctly refilled and that the oil level is correct.
That all external components have been filled with oil in advance.
Check whether any oil is leaking from components, hoses and fittings and re-
tighten as necessary.
STARTING/START-UP OF THE SYSTEM
It is very important that the start-up procedure is carried out correctly to maximise the
lifetime of the system. Many pumps in particular are damaged during start-up
because the very strict purity requirements are not met or the user manual is not
followed. However, even with the highest purity levels and the greatest care, it is not
possible to completely avoid dirt with an entirely new system, as particles are also
scraped off moving components during the actual start-up and starting processes.
The system must therefore not be subjected to the maximum load until all the dirt in
the filters has been removed. All the filters must be replaced after ever five operating
hours.
Check the oil level frequently and always top up with clean oil.
The oil must not be allowed to drip down onto the ground, floor or similar. The oil
must be collected up in a waste oil tray, bucket or similar. It is important that we
protect the environment.
RE-TIGHTENING THE SYSTEM
Shortly after start-up/starting at the highest operating pressure, all fittings, bolts,
screws, pipes and hoses on the various systems should be re-tightened. Re-
tightening should then be carried out as necessary.
It is important that all hydraulic components and pipe components are re-tightened
due to the high operating pressures and rapid heat generation.
Summary of Contents for W-6011-EH
Page 1: ...Fransgård Manual GB Tractor winch W 6011 EH ...
Page 10: ...8 g A B D E Max 30 Max 30 C A B C D ...
Page 11: ...9 F H G Max 4mm ...
Page 13: ...11 ...
Page 21: ......
Page 22: ......
Page 23: ......
Page 24: ......