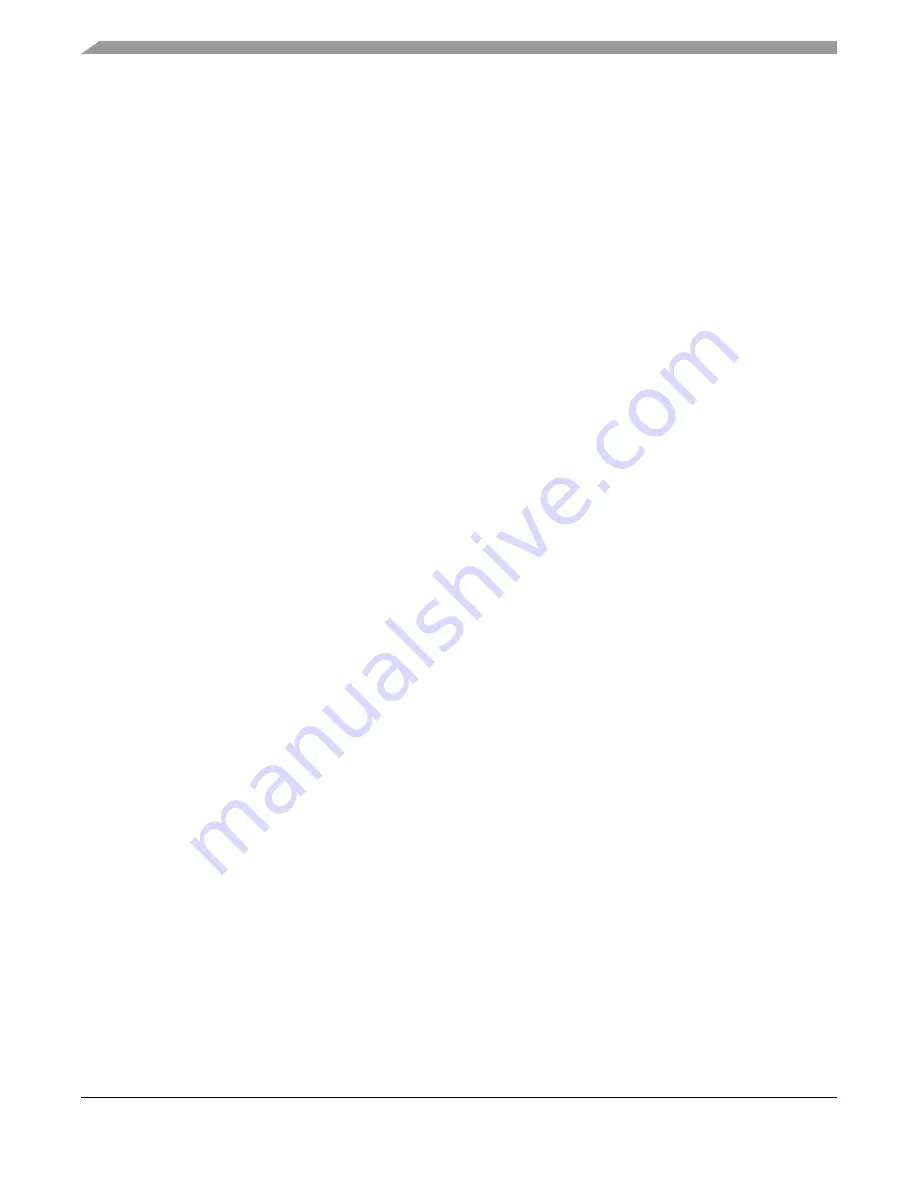
MPC563XM Reference Manual, Rev. 1
846
Freescale Semiconductor
Preliminary—Subject to Change Without Notice
the same filter clock as the channel input signals. For details on TCRCLK and channels digital filter
control refer to
Section 23.3.3.1, “ETPUTBCR - eTPU Time Base Configuration Register
and
Section 23.4.5.6, “Enhanced Digital Filter - EDF
23.4.6.2.4
Red Line (STAC) Bus Client Mode
In this mode the TCR2 register is continuously updated from the Red Line (STAC) bus, and the clock
selection and prescaling logic becomes ineffective. It is not write accessible for the microcode, and when
read, it reflects the Red Line bus imported value. The use of EAC is forbidden in client mode. This mode
is configured through the register ETPUREDCR (see
Section 23.3.3.4, “ETPUREDCR - eTPU Red Line
).
23.4.6.2.5
Red Line (STAC) Bus Server Mode
When TCR2 bus is exported to the Red Line (STAC) bus as a server, it can provide either time or angle
bus to other peripherals, according to its operation mode. This mode is configured through the register
ETPUREDCR (see
Section 23.3.3.4, “ETPUREDCR - eTPU Red Line Configuration Register
). To
provide sequential update of the Red Line clients, the Angle tick rate must not be faster than the Red Line
programmed update rate. This requirement puts a limitation on the angle clock count rate on high rate
mode. In this case the Angle and Angle Fraction accumulator (see
) are advanced at rate of system clock divided by eight. Therefore, the Red
Line update rate for the Angle Bus must not be slower than eight system clocks.
23.4.6.2.6
TCR2 Bus in Angle Clock Mode
In this mode the TCR2 counter operates as part of the eTPU Angle Counter (EAC). The TCR2 bus value
reflects this angle representation in which it counts Angle Ticks. Angle Mode is selected when the AM bit
is set in ETPUTBCR.
Note that when TCR2 works in Angle Mode, it does not count directly from the TCR2 clock input which
indicates tooth signal transition. Its Angle counter is controlled by the Count Control and High Rate logic
(see
Section 23.4.7.5, “Count Control and High Rate Logic
), which provides the interpolated pin position,
and handle cases of missing tooth, acceleration, de-acceleration and mechanical corrections.
The EAC uses the TCRCLK signal to get the tooth transition indications. The TCR2CTL field in
ETPUTBCR has to be set for the appropriate tooth edge detection rise, fall, “rise-and-fall” or none. TCR2
count clock comes from the EAC control and not directly from the physical tooth. This way the EAC
control processes the signal transitions and handles missing teeth and flywheel mechanical corrections.
Note that when TCR2CTL selects “none” for tooth edge selection, the TCR2 is not necessarily frozen, but
can still be incremented by the EAC logic.
In Angle Mode, eTPU channel 0, 1 or 2 operation is combined with the EAC operation. When channel 0
is selected for EAC operation, the TCRCLK digital filter is used both by the EAC and by channel 0 to get
full synchronization between the two logics.
The eTPU Angle Counter (EAC) logic runs continuously and updates the TCR2 Angle counter,
eliminating the microcode latency in updating the TCR2 value.