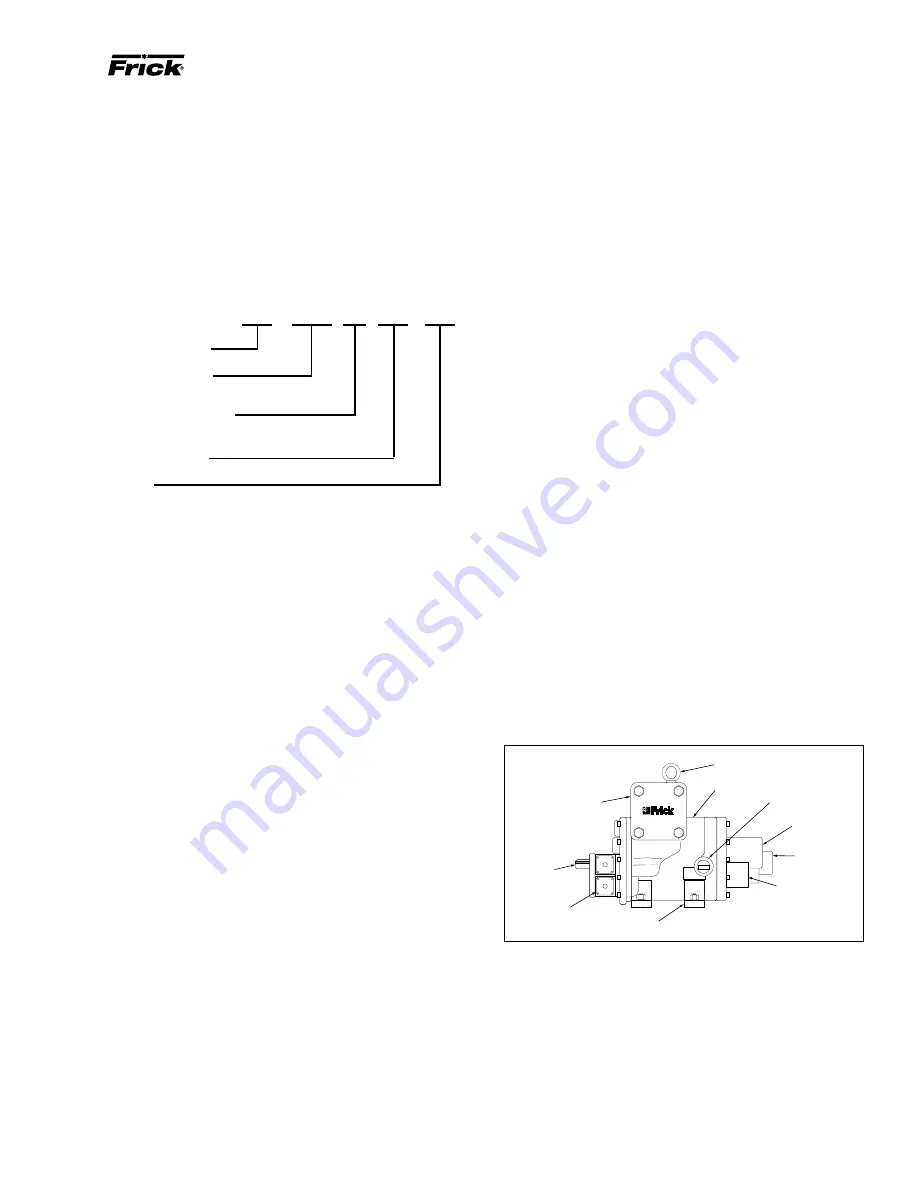
S70-101SM
Page 3
Frick XJS and XJF Rotary Screw Compressor
Service Manual
GENERAL
This manual provides approved procedures for teardown,
parts replacement, and rebuild of Model XJS and XJF 95/120
compressors, manufactured by Frick and installed on RXB
and RXF Rotary Screw Compressor Units.
To avoid errors when ordering parts, always provide complete
Model Number and Serial Number.
MODEL AND SERIAL NUMBER EXPLANATION
MODEL NUMBER
ROTOR DIA. (MM)
2.13/1 GEAR RATIO – S
1.31/1 GEAR RATIO – M
1.62/1 GEAR RATIO – L
SERIAL NUMBER
A - 95S
B - 95M
C - 95L
D - 120S
E - 120M
F - 120L
GENERAL MAINTENANCE
Proper maintenance is important in order to ensure continued, trouble-
free service from your compressor. Some areas critical to optimum
compressor operation are:
• Keep refrigerant and oil clean and dry to avoid moisture contamination.
After servicing any portion of the refrigeration system, evacuate to
remove moisture before returning to service. Water vapor condensing
in the compressor while it is running, or more likely while it is shut down,
can cause rusting of critical components and reduce the service life of
the unit.
• Keep suction strainer clean. Check periodically, particularly on new
systems where welding slag or pipe scale could find its way into the
compressor suction. Excessive dirt in the suction strainer could cause
it to collapse, dumping debris into the compressor.
• Keep oil filters clean. If filters show increasing pressure drop
(indicating dirt or water), stop compressor and change filters. Running
a compressor for long periods with high filter pressure drop can cause
oil starvation and lead to premature bearing failure.
• Avoid slugging compressor with liquid refrigerant. While screw-type
compressors are probably the most tolerant to ingestion of some
refrigerant liquid, they are not liquid pumps. Be sure to maintain
adequate superheat, and properly size suction accumulators to avoid
dumping liquid refrigerant into compressor suction.
• Keep liquid injection valves properly adjusted and in good condition
to avoid flooding compressor with liquid. Liquid can cause a reduction
in compressor life, and in extreme cases, can cause complete failure.
XJS 95/120 S 0123 D
• Protect compressor during extended periods of shutdown. If
compressor will be setting for long periods without running,it
is advisable to evacuate to low pressure and charge with dry
nitrogen or oil, particularly on systems known to contain
amounts of water vapor.
• Preventive maintenance inspection is recommended any
time a compressor exhibits a noticeable change in vibration
level, noise level, and/or performance.
NOTE: • Some photographs or illustrations in this manual
may be of prototype or special order units. Pro-
duction models may vary in some detail from
those shown.
• Some photographs or illustrations in this manual
may show units with optional equipment installed.
These items are available through your autho-
rized Frick Factor.
PREVENTIVE MAINTENANCE INSPECTION AND
SERVICE
Frick Model XJS and XJF 95/120 Rotary Screw Compressors
are designed and manufactured to the highest engineering and
quality standards to provide optimum performance and con-
tinued service in applications of intended use, with no devia-
tions from original design. A preventive maintenance pro-
gram ensures maximum compressor life and minimizes costly
unscheduled unit downtime. Immediate shutdown and in-
spection should be made if increased sound or vibration,
increased shaft seal leakage, erratic slide valve operation,
fluctuating oil pressure, loss of compressor efficiency, in-
creased oil consumption, and/or oil contamination are ob-
served. Major inspection should be made, per the schedule,
listed in the Frick Rotary Screw Compressor IOM manual.
XJS and XJF Rotary Screw Compressor
DRIVE
END
Vi CONTROL SOLENOID
VALVE (120 VAC)
DRIVESHAFT
FRONT VIEW
MOUNTING
FOOT (4)
SUCTION VALVE
AND
STRAINER ASSY.
SLIDE VALVE
INDICATOR
SLIDE VALVE
ASSY.
ROTOR
CASING
LIFTING EYE
GEAR AND ROTOR
ASSY.
DISCHARGE
END
ECONOMIZER PORT
Property of American Airlines