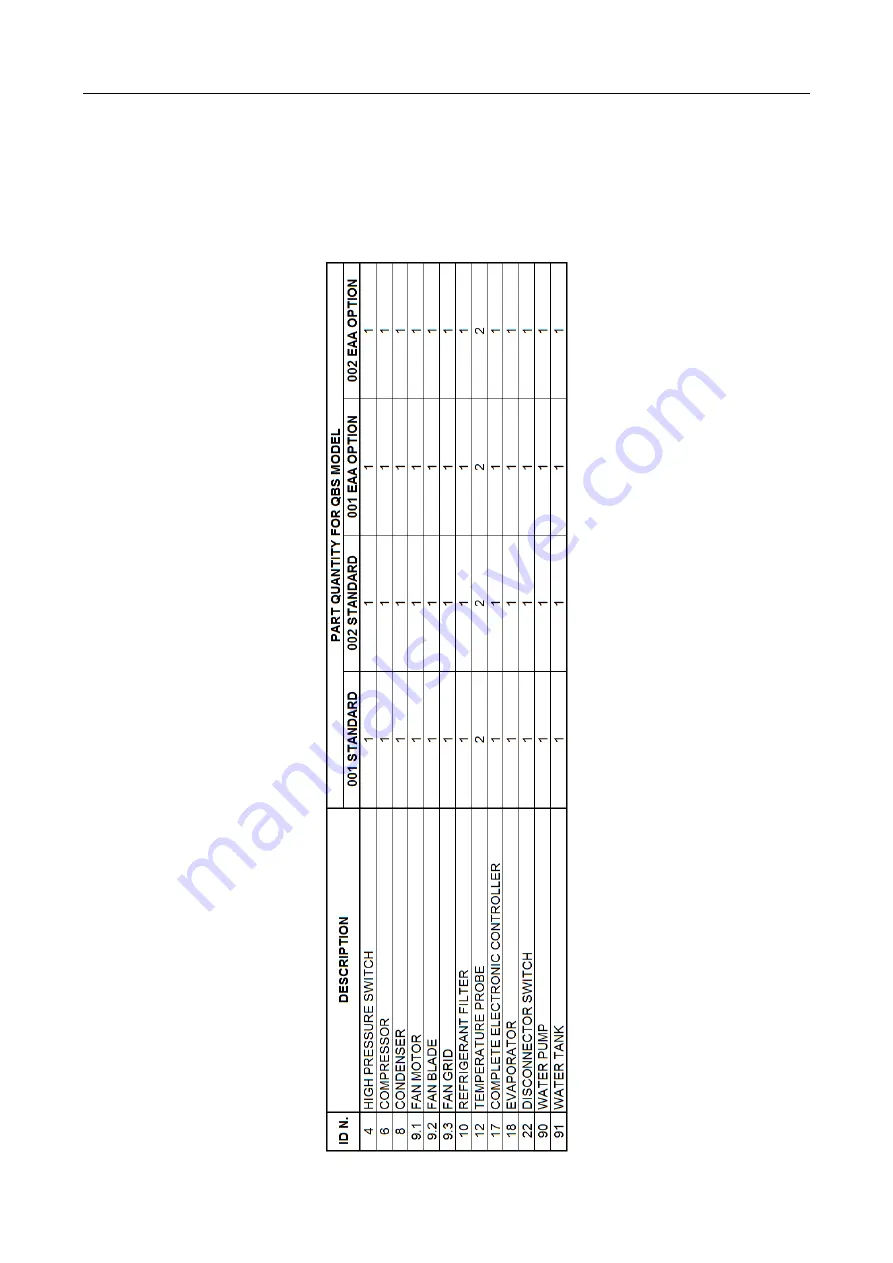
6
7425MUM651
Model: QBS
- Use and Maintenance Manual
Rev. 02
2.8
S
PARE PARTS
Spare parts list is printed on a dedicated sticker applied inside the chiller. On this sticker each spare
part is identified with its ID Number and related Spare Part Number. Here below the cross reference
table between ID Number and exploded drawings Ref. With their description and quantity installed
inside chillers.
NOTE
To order the suggested spare parts or any other part, it is necessary to quote the data
reported on the identification plate.