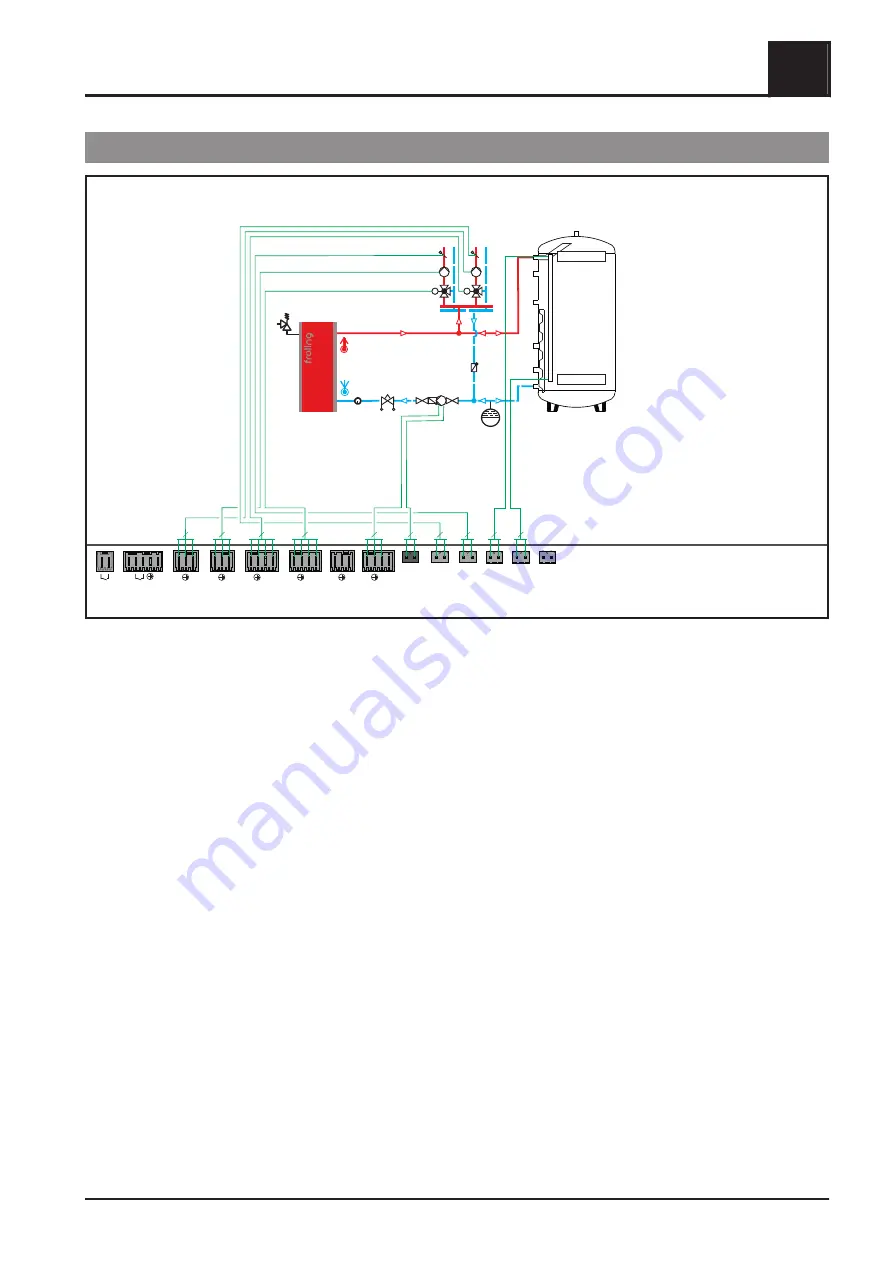
2.5.3 System 1 (layered tank / two heating circuits)
N
AUF
ZU
N
AUF
ZU
L
N
L1
N
L
N
Mischer 2
(30)
HKP 0 /
Brennerrelais
(34)
Heizkreis-
pumpe 1
(33)
Heizkreis-
pumpe 2
(32)
Mischer 1
(31)
PWM/0-10V
Pumpe 1 (26)
V
orlauf-
fühler 1 (23)
V
orlauf-
fühler 2 ( 22)
Durchfluss-
messer (12)
L
N
Netz
(29)
L
N
Pumpe 1
(28)
L
V
Fühler 1 (18)
Fühler 2 (17)
Betriebs-
signal
(35)
M
M
A
B
C
D
E
F
G
H
I
J
2
2
2
2
2
3
3
3
4
4
Fröling PECO
Pump assembly
OE
Layered tank
Flow temperature sensor 1/2
Heating circuit pump 1/2
Mot. mixing valve 1/2
Sensor 1, A
Sensor 2, J
Balancing
valve
Pump 1
If deviating from the default configuration, the following changes must be made:
❒ Select “System 1” in the system selection
❒ Deactivate DHW tank 01
❒ Activate heating circuit 02
⇨ See "Setting the system selection" [page 34]
Adjust sensor assignments:
❒ In the service menu of the storage tank, assign the sensor inputs according to the diagram shown above
Power connection and wiring
2
Connection options with standard delivery
Service Manual Lambdatronic P 3200 for pellet boiler (4,3" Touch) | B1620121_en
31
Summary of Contents for Lambdatronic P 3200
Page 85: ...6 Notes Notes 6 Service Manual Lambdatronic P 3200 for pellet boiler 4 3 Touch B1620121_en 85...
Page 86: ...6 Notes 86 Froling GesmbH A 4710 Grieskirchen Industriestra e 12 www froeling com...
Page 87: ...Notes 6 Service Manual Lambdatronic P 3200 for pellet boiler 4 3 Touch B1620121_en 87...