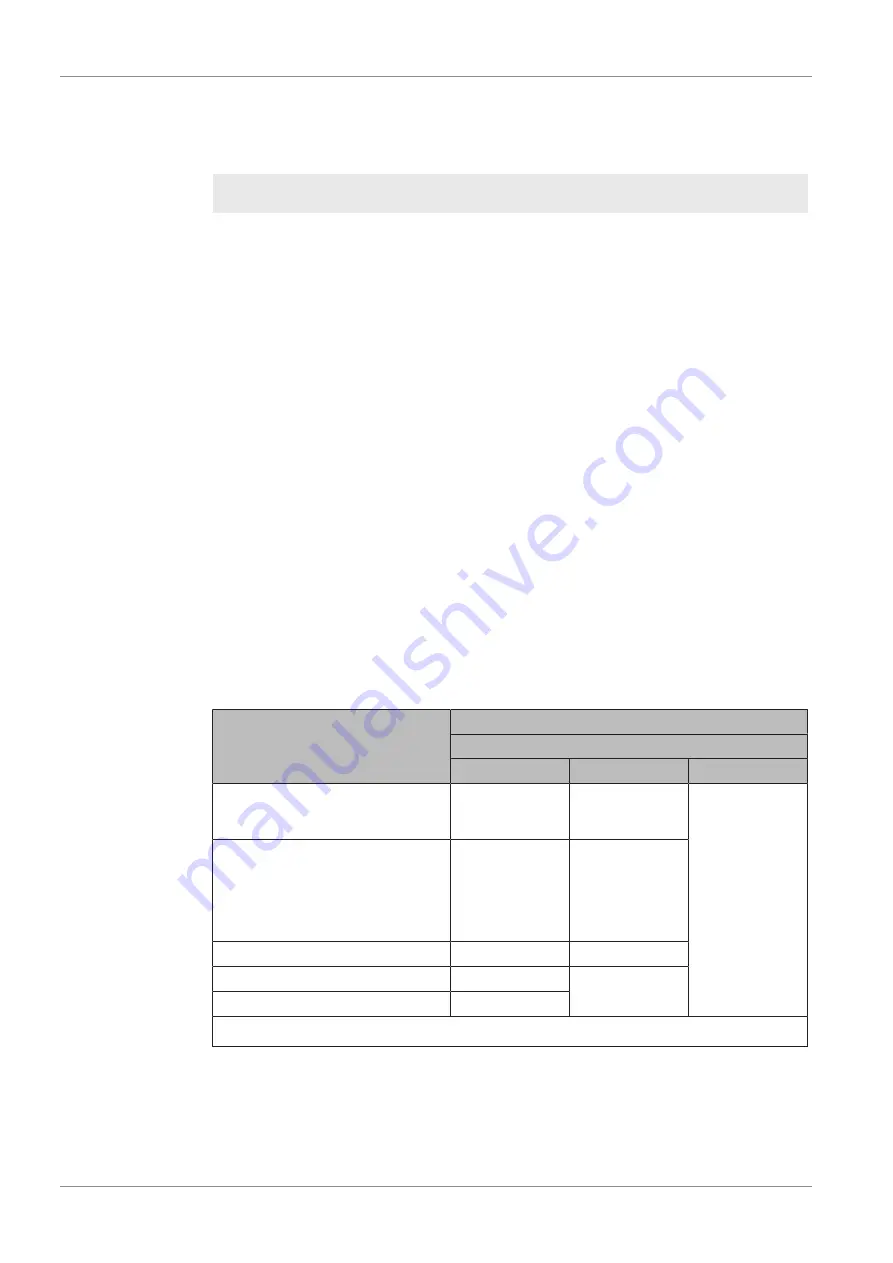
3 | Notes for operating a heating system
20
B1510622_en | Operating instructions Firewood boiler S4 Turbo
3.4 Domestic hot water
Unless contrary to other national regulations, the latest versions of the following
standards and guidelines apply:
Austria:
Germany:
ÖNORM H 5195
VDI 2035
Switzerland:
Italy:
SWKI BT 102-01
UNI 8065
Observe the standards and also follow the recommendations below:
r
Aim for a pH value of between 8.2 and 10.0. If the central heating water comes into
contact with aluminium, the pH value must be between 8.2 and 9.0
r
Use prepared water which complies with the standards cited above for filling and
make-up water
r
Avoid leaks and use a closed heating system to maintain water quality during
operation
r
When filling with make-up water, always bleed the filling hose before connecting, in
order to prevent air from entering the system
r
The heating water must be clear and free from substances that lead to sediments.
r
With regard to corrosion protection, the use of fully demineralised filling and make-up
water with an electrical conductivity of up to 100 µS/cm is recommended in
accordance with EN 14868
Advantages of low-salt or fully demineralised water:
▪ Complies with the applicable standards
▪ Less of a drop in output due to reduced limescale build-up
▪ Less corrosion due to fewer aggressive substances
▪ Long-term cost savings thanks to improved energy efficiency
Filling and make-up water as well as heating water in accordance with VDI 2035:
Total heat output in kW
Total earth alkalis in mol/m³ (total hardness in °dH)
Specific system volume in l/kW heat output
1)
≤ 20
20 to ≤40
> 40
≤ 50
specific water content
heat generator ≥ 0.3 l/kW
2)
none
≤ 3.0 (16.8)
< 0.05 (0.3)
≤ 50
specific water content
heat generator < 0.3 l/kW
2)
(e.g. circulation water heater) and
systems with electric heating
elements
≤ 3.0 (16.8)
≤ 1.5 (8.4)
> 50 to ≤ 200
≤ 2.0 (11.2)
≤ 1.0 (5.6)
> 200 to ≤ 600
≤ 1.5 (8.4)
< 0.05 (0.3)
> 600
< 0.05 (0.3)
1. For calculating the specific system volume, the smallest individual heating capacity is to be used for systems with several heat generators.
2. In systems with several heat generators with different specific water contents, the smallest specific water content is decisive in each case.