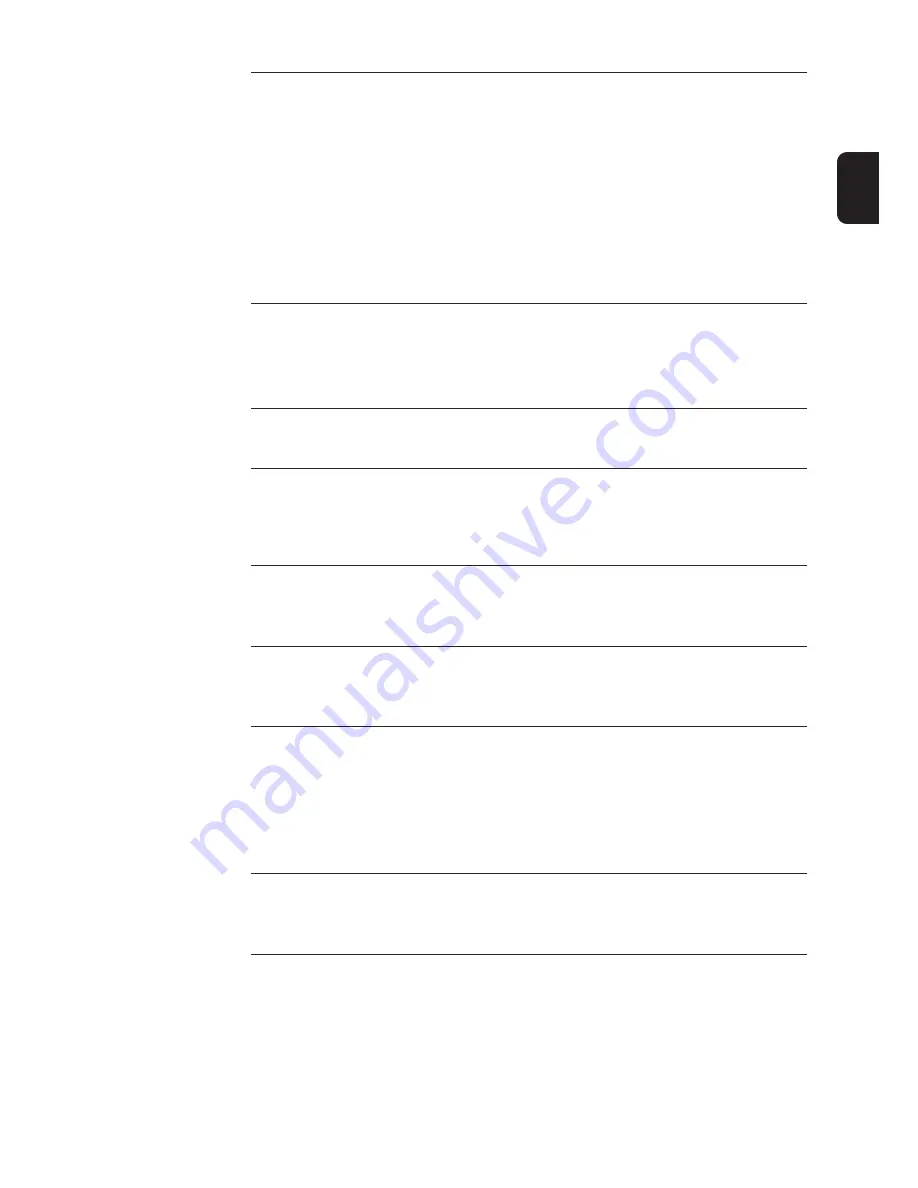
21
EN
Excessive formation of „dross“ during the cutting operation
Cause:
Cutting speed too fast
Remedy:
Reduce cutting speed
Cause:
Cutting speed too slow
Remedy:
Increase cutting speed
Cause:
Cutting current too low
Remedy:
Increase cutting current
Cause:
Wrong operating mode selected
Remedy:
Select a different mode
Cause:
Cutting torch applied incorrectly
Remedy:
Apply cutting torch with a slight forward inclination
Steam escaping between body of torch and protective cap
Cause:
Protective cap fitted to cutting torch incorrectly
Remedy:
Tighten protective cap on cutting torch
Cause:
Cutting nozzle cone dirty or damaged
Remedy:
Clean cutting nozzle or install new cutting nozzle
Service codes
displayed
Fault diagnosis
(continued)
Excess temperature indicator lit
Cause:
Device overheating
Remedy:
Leave device switched on and wait until it has cooled down.
The indicator is turned off automatically as soon as the device is
ready for operation again.
Fill level indicator lit
Cutting can nevertheless continue.
Cause:
Most of the cutting medium in the tank has been used up
Remedy:
Keep a cartridge of cutting medium at the ready or refill tank
Fill level indicator flashing
Cutting can no longer be continued
Cause:
No cutting medium in tank
Remedy:
Fill tank with cutting medium
Torch indicator lit
Cause:
Protective cap fitted to cutting torch incorrectly
Remedy:
Fit protective cap correctly
Cause:
Wearing parts on cutting torch fitted incorrectly
Remedy:
Fit wearing parts correctly
Cause:
Wearing parts faulty or worn
Remedy:
Replace wearing parts
Error indicator lights up
Cause:
Internal machine fault
Remedy:
Switch device off and on again If the error recurs after the device is
switched on again you should notify After-Sales Service immediately.
Summary of Contents for TransCut 300
Page 2: ......
Page 4: ......
Page 14: ...10 ...
Page 28: ...24 ...
Page 31: ...TransCut 300 plasma cutting device ...
Page 32: ...TransCut 300 cutting torch ...