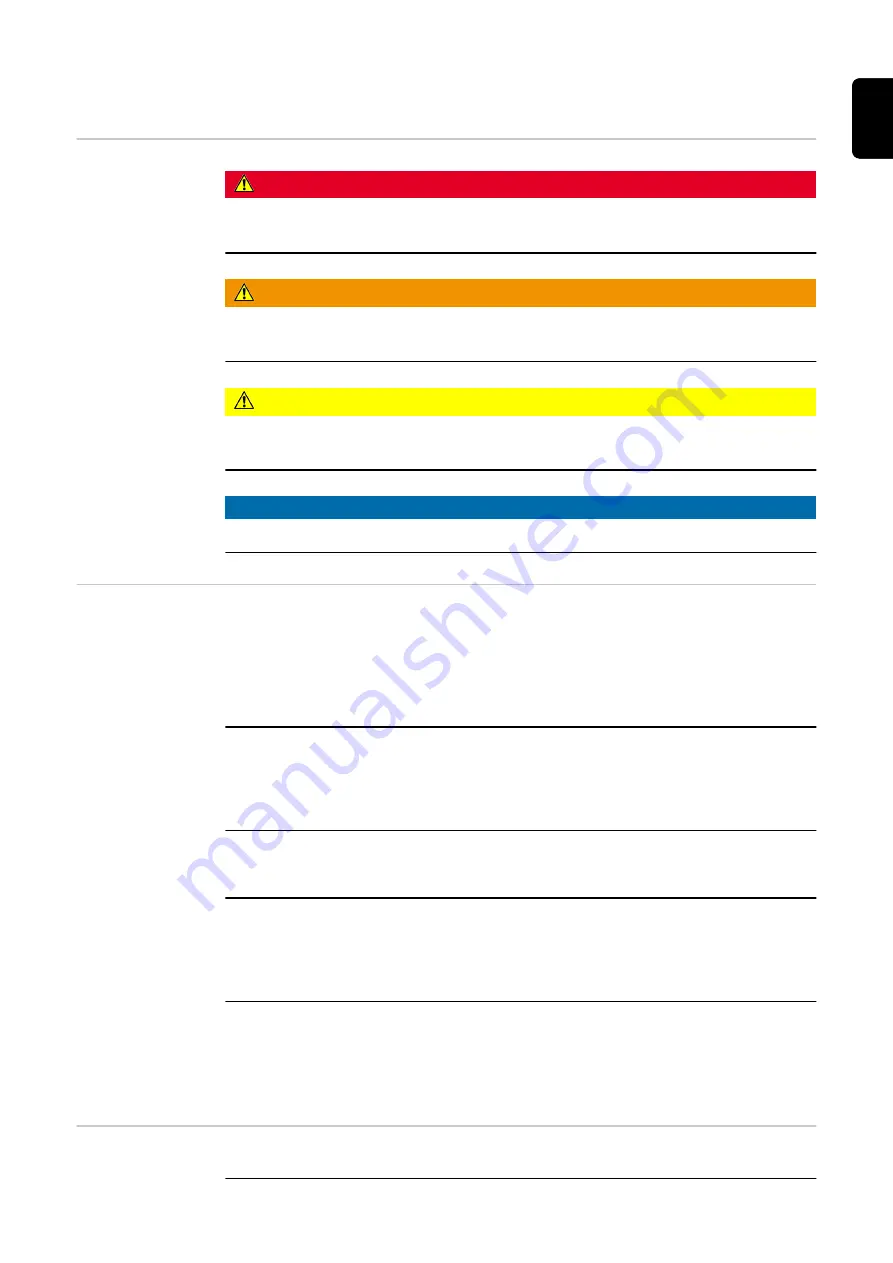
Safety rules
Explanation of
safety notices
DANGER!
Indicates immediate danger.
▶
If not avoided, death or serious injury will result.
WARNING!
Indicates a potentially hazardous situation.
▶
If not avoided, death or serious injury may result.
CAUTION!
Indicates a situation where damage or injury could occur.
▶
If not avoided, minor injury and/or damage to property may result.
NOTE!
Indicates a risk of flawed results and possible damage to the equipment.
General
The device is manufactured using state-of-the-art technology and according to recog-
nised safety standards. If used incorrectly or misused, however, it can cause:
-
injury or death to the operator or a third party,
-
damage to the device and other material assets belonging to the operating com-
pany,
-
inefficient operation of the device.
All persons involved in commissioning, operating, maintaining and servicing the device
must:
-
be suitably qualified,
-
have sufficient knowledge of welding and
-
read and follow these operating instructions carefully.
The operating instructions must always be at hand wherever the device is being used. In
addition to the operating instructions, attention must also be paid to any generally applic-
able and local regulations regarding accident prevention and environmental protection.
All safety and danger notices on the device
-
must be in a legible state,
-
must not be damaged,
-
must not be removed,
-
must not be covered, pasted or painted over.
For the location of the safety and danger notices on the device, refer to the section
headed "General" in the operating instructions for the device.
Before switching on the device, rectify any faults that could compromise safety.
This is for your personal safety!
Proper use
The device is to be used exclusively for its intended purpose.
5
EN
Summary of Contents for WF 25i REEL R /SA/2R/G/W
Page 2: ......
Page 19: ...Wear eye protection 19 EN...
Page 27: ...3 4 5 27 EN...
Page 30: ...AlMg 3 5 Al AlSi 2 4 Tubular cored elec trodes 3 5 30...
Page 39: ...39 EN...