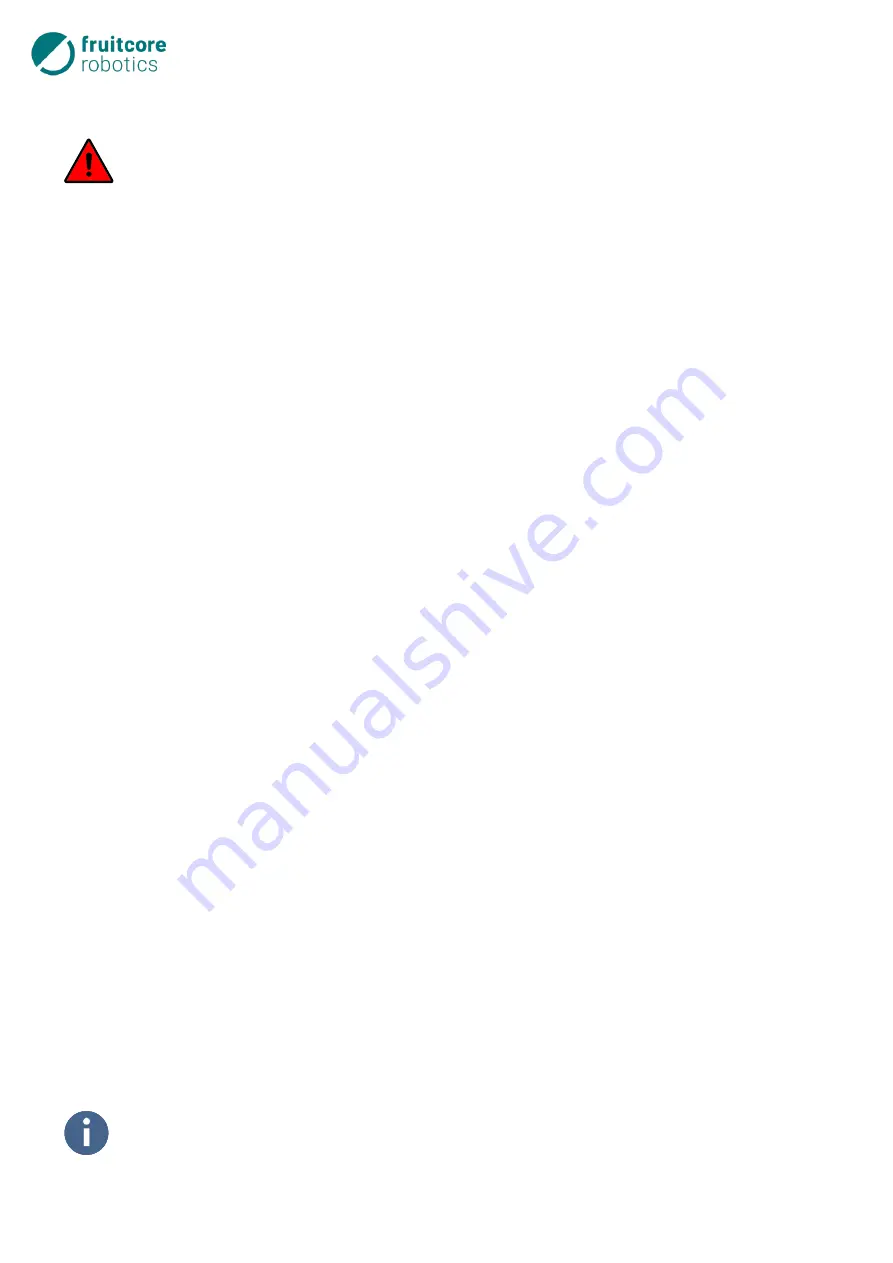
2 Safety Functions
10
The
danger zone
includes the working area and stopping distance of the robot. Persons must not be in
the danger zone while the robot is in operation.
DANGER!
Due to the robot’s automatic movement, sudden dangers must be expected within the danger
zone. Moving modules may cause personal injury or property damage.
The robot system must be operated only in technically perfect condition and with active
safety equipment.
The robot must be used only within suitable protection devices (e.g. separating protection
device, light curtain, or safety laser scanner). The protection devices must stop the robot’s
movement within the danger zone.
The
safe area
is located outside the danger zone. Persons may be in this area during all operating modes.
2.7
Safety Functions
The robot control is equipped with two different types of safety functions, both of which bring the robot
into a safe condition. A safe state is achieved by braking all of the robot’s drive axles.
The two fundamental emergency stop and safety stop safety functions are described below.
Emergency Stop
Bringing about a safe condition of the robot in the event of an emergency situation. This safety function
is available in all operating modes. It takes precedence over all safety functions. It is triggered by the
emergency stop button or external safety controls. External emergency stop devices are connected to the
emergency stop inputs of the switch cabinet, hereinafter referred to as the horstCONTROL.
This safety function must be used in emergency situations exclusively in order to bring the robot into a
safe condition. The emergency stop must not be used for process-related stops.
Safety Stop
Bringing about a safe condition of the robot for process-related and safety-critical situations. This safety
function is to be used for process-related stops during which operating personnel must be able to inter-
vene in the danger zone.
The purpose of both types of safety functions is to bring about a safe condition of the robot.
The safe condition is marked by the following properties:
−
Emergency stop: A category 1 stop is triggered. The robot is braked actively until it comes to a
standstill; the brakes are applied, and the energy of the drives is then switched off.
−
Safety stop: A category 2 stop is triggered. The robot is actively braked until it comes to a
standstill. The drive power is not switched off. The safe standstill is monitored.
The robot control has other safety functions. These are described in the subsections on the configurable
safety functions from page 37.
The safety-
related performance of the control system corresponds to PL “d” with structure
category 3 according to DIN EN ISO 13849-1:2006. It is defined by the risk assessment of the
robot system or DIN EN ISO 10218-1.
Summary of Contents for HORST900
Page 3: ...III ...