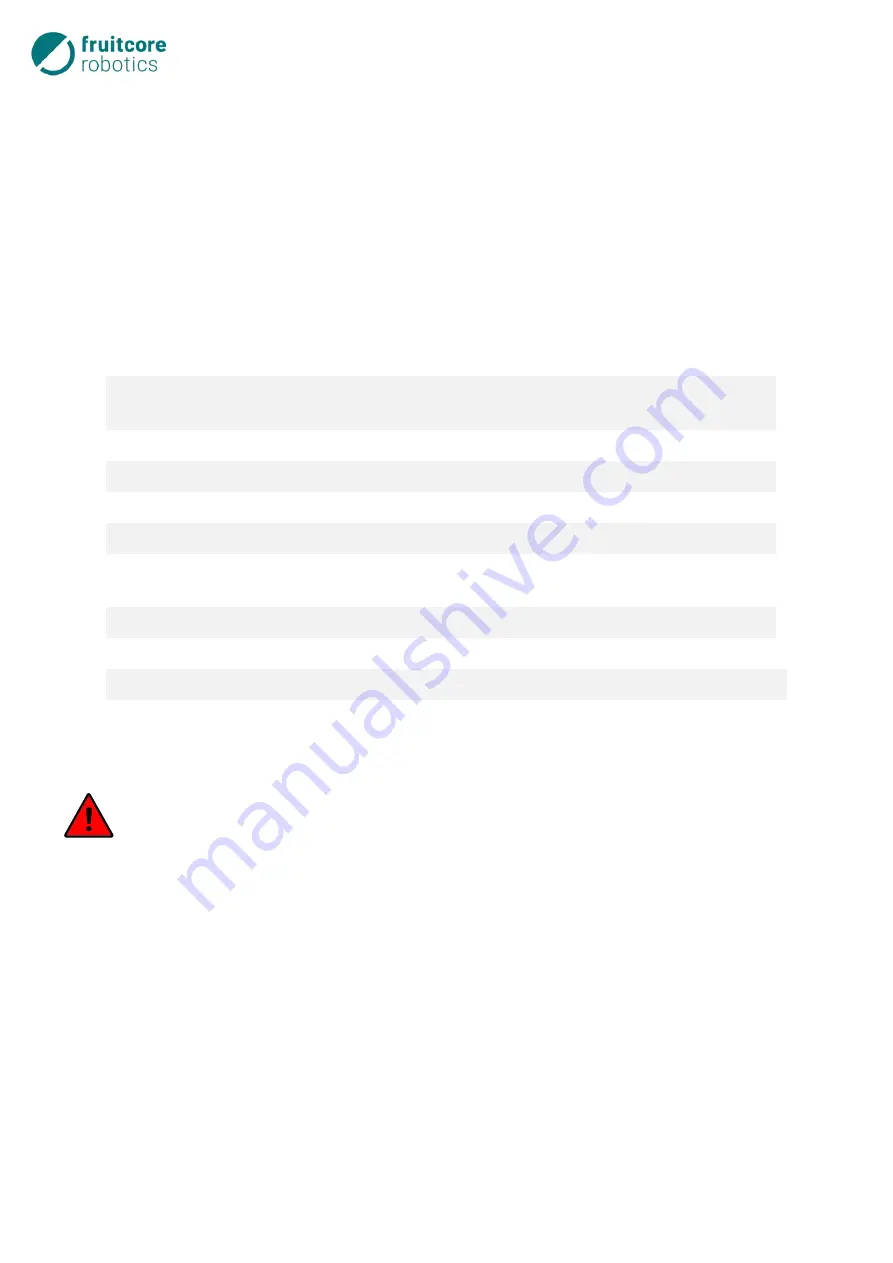
6 horstCONTROL I/O
34
6.4.2
Safety-critical Inputs/Outputs
The horstCONTROL is equipped with several safe inputs and outputs. Safe I/Os are established redun-
dantly through two independent lines. An incident or failure of a line therefore does not result in the com-
plete loss of the safety function.
Some of the safe I/Os are configurable to enable extended connectivity and functionality with devices and
systems. They can be assigned safety-critical functions in the horstFX software, but they can also be
used as normal digital I/Os.
The emergency stop and safety stop inputs as well as the enabling switch input are exclusively safe in-
puts. The emergency stop input is only intended for the connection of emergency stop devices. The safety
stop inputs apply to all kinds of safety-critical protection devices (e.g. safety laser scanners). The func-
tional difference is explained in the following table:
Emergency stop input
Safety stop input
Active
In all operating modes
(T1, T2, Automatic)
Only in automatic mode
Robot movement stops
Yes
Yes
Energization of drives
Off
On
Program execution
Paused
Paused
Acknowledgement
Manually at the horstPANEL Manually at the horstPANEL
Further operation after
acknowledgement
Program continues running
at interrupted position
Program continues running at
interrupted position
Requires reinitialization
No *
No *
Stop category (IEC 60204)
1
2
Power level (ISO 13849-1)
PL d
PL d
* Only if the power supply has been interrupted must the robot must be reinitialized.
Table 6-2: Functional difference between emergency stop and safety stop
DANGER!
Danger due to incorrectly connected emergency stop devices
Never connect safety signals to a PLC that does not meet at least the corresponding pro-
tection level. This could cause the safety functions to be overridden, which could result in
serious injuries or death.
Only use the safe inputs for emergency stop to connect additional emergency stop devices.
Do not connect any emergency stop devices to general digital inputs or safety stop inputs.
Safety-critical I/Os always have two channels. The two channels must be kept separate to
prevent a fault from causing loss of the safety function.
The safety functions must be tested before commissioning and at regular intervals.
Summary of Contents for HORST900
Page 3: ...III ...