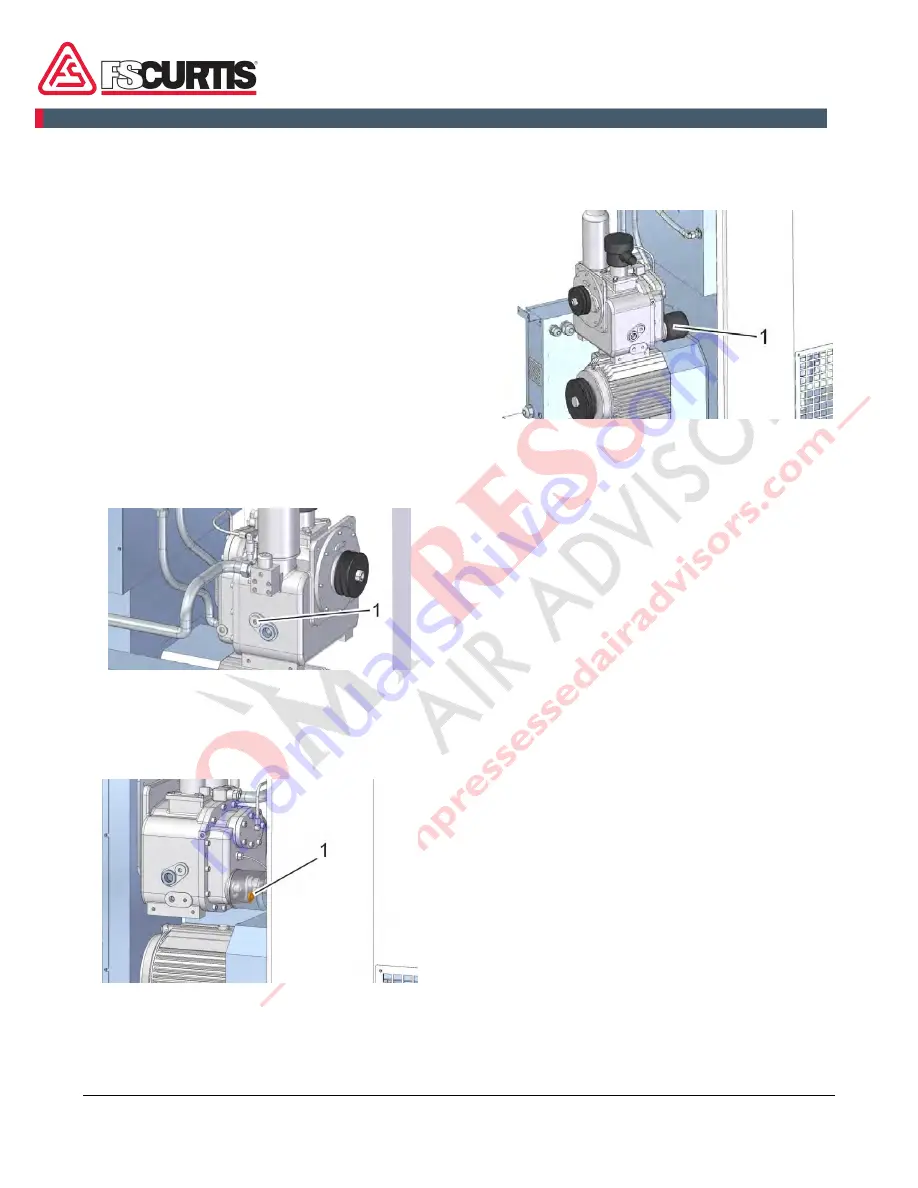
Maintenance
CAP-834
41
10.
Switch on the compressor and switch it off
again without waiting any longer than one mi-
nute
controller documentation
.
11.
Check the oil level and top up as necessary
Chapter 7.4.3 ‘Checking the oil level/topping
up the oil’ on page 37
.
Replace the oil filter
1.
Close the shut-off valve on the pressure network
side and secure it to prevent it from being
opened again.
2.
Open and remove the enclosure panels with the
special wrench.
3.
Use a drip pan to make sure that the leaking oil
is collected.
Fig. 35: Filler nozzle
4.
Unfasten the filler nozzle (Fig. 35/1), remove it
and make sure that the gasket is not misplaced.
Fig. 36: Oil drain
5.
Open the oil drain (Fig. 36/1).
The oil is drained.
6.
Close the oil drain (Fig. 36/1).
Fig. 37: Removing the oil filter
7.
Use the strap wrench to unfasten and remove
the old oil filter (Fig. 37/1).
8.
Remove old gasket remains from the oil filter
housing.
9.
Moisten the new gasket with a little oil.
10.
Screw in the new oil filter (Fig. 37/1) all the way.
11.
Tighten the new oil filter (Fig. 37/1) half a turn
by hand.
12.
Switch on the compressor and switch it off
again without waiting any longer than one mi-
nute
controller documentation
.
13.
Check the oil level and top up as necessary
Chapter 7.4.3 ‘Checking the oil level/topping
up the oil’ on page 37
.
7.4.9
Replacing the air/oil separator
1.
Close the shut-off valve on the pressure network
side and secure it to prevent it from being
opened again.
2.
Open and remove the enclosure panels with the
special wrench.
3.
Use a drip pan to make sure that the leaking oil
is collected.