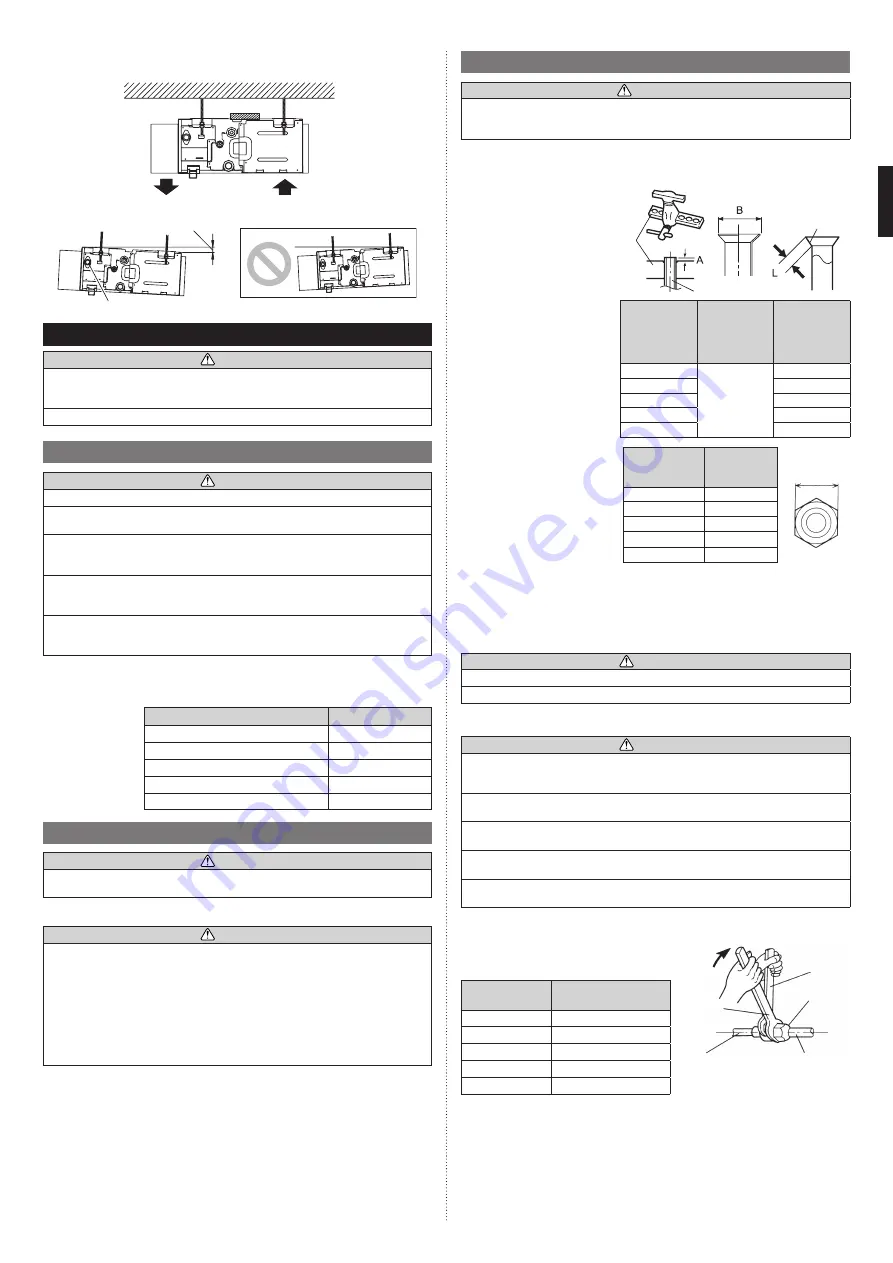
En-4
Right side view
Give a slight tilt to the rear side. The tilt should be in the range of 0 mm to 5 mm.
Level
Air
Air
GOOD
PROHIBITED
5 or less
Drain port
Unit: mm
4. PIPE INSTALLATION
CAUTION
Be more careful that foreign matter (oil, water, etc.) does not enter the piping than with
refrigerant R410A models. Also, when storing the piping, securely seal the openings by
pinching, taping, etc.
While welding the pipes, be sure to blow dry nitrogen gas through them.
4.1. Selecting the pipe material
CAUTION
Do not use existing pipes from another refrigeration system or refrigerant.
Use pipes that have clean external and internal sides without any contamination which
may cause trouble during use, such as sulfur, oxide, dust, cutting waste, oil, or water.
It is necessary to use seamless copper pipes.
Material: Phosphor deoxidized seamless copper pipes
It is desirable that the amount of residual oil is less than 40 mg/10 m.
Do not use copper pipes that have a collapsed, deformed, or discolored portion (es
-
pecially on the interior surface). Otherwise, the expansion valve or capillary tube may
become blocked with contaminants.
Improper pipe selection will degrade performance. As an air conditioner using R410A
incurs pressure higher than when using conventional (R22) refrigerant, it is necessary to
choose adequate materials.
• Thicknesses of copper pipes used with R410A are as shown in the table.
• Never use copper pipes thinner than those indicated in the table even if they are avail
-
able on the market.
Thicknesses of
Annealed Copper
Pipes (R410A)
Pipe outside diameter [mm (in)]
Thickness [mm]
6.35 (1/4)
0.80
9.52 (3/8)
0.80
12.70 (1/2)
0.80
15.88 (5/8)
1.00
19.05 (3/4)
1.20
4.2. Pipe requirement
CAUTION
Refer to the installation manual of the outdoor unit for description of the length of con
-
necting pipe or for difference of its elevation.
• Use pipe with water-resistant heat insulation.
CAUTION
Install heat insulation around both the gas and liquid pipes. Failure to do so may cause
water leaks.
Use heat insulation with heat resistance above 120 °C. (Reverse cycle model only)
In addition, if the humidity level at the installation location of the refrigerant piping is
expected to exceed 70 %, install heat insulation around the refrigerant piping. If the
expected humidity level is 70 to 80 %, use heat insulation that is 15 mm or thicker and
if the expected humidity exceeds 80 %, use heat insulation that is 20 mm or thicker.
If heat insulation is used that is not as thick as specified, condensation may form on
the surface of the insulation. In addition, use heat insulation with heat conductivity of
0.045 W/(m·K) or less (at 20 °C).
4.3. Flare connection (pipe connection)
WARNING
Tighten the flare nuts with a torque wrench using the specified tightening method. Oth
-
erwise, the flare nuts could break after a prolonged period, causing refrigerant to leak
and generate hazardous gas if the refrigerant comes into contact with a flame.
4.3.1. Flaring
Use special flare tool exclusive for R410A.
(1) Cut the connection pipe to
the necessary length with a
pipe cutter.
(2) Hold the pipe downward so
that cuttings will not enter the
pipe and remove any burrs.
(3) Insert the flare nut (always
use the flare nut attached to
the indoor and outdoor units
(or RB unit) respectively)
onto the pipe and perform
the flare processing with a
flare tool. Use the special
R410A flare tool. Leakage of
refrigerant may result if other
flare nuts are used.
(4) Protect the pipes by pinching
them or with tape to prevent
dust, dirt, or water from
entering the pipes.
Check if [L] is
flared uniformly
and is not cracked
or scratched.
Pipe
Die
Pipe outside
diameter
[mm (in)]
Dimension A
[mm]
(Flare tool for
R410A, clutch
type)
Dimension
B
0
-0.4
[mm]
6.35 (1/4)
0 to 0.5
9.1
9.52 (3/8)
13.2
12.70 (1/2)
16.6
15.88 (5/8)
19.7
19.05 (3/4)
24.0
When using conventional (R22)
flare tools to flare R410A pipes, the
dimension A should be approxi
-
mately 0.5 mm more than indicated
in the table (for flaring with R410A
flare tools) to achieve the speci
-
fied flaring. Use a thickness gauge
to measure the dimension A. It is
recommended that a R410A flaring
tool is used.
Pipe outside
diameter
[mm (in)]
Width across
flats of flare nut
[mm]
6.35 (1/4)
17
9.52 (3/8)
22
12.70 (1/2)
26
15.88 (5/8)
29
19.05 (3/4)
36
Width across
flats
4.3.2. Bending pipes
• If pipes are shaped by hand, be careful not to collapse them.
• Do not bend the pipes in an angle more than 90°.
• When pipes are repeatedly bend or stretched, the material will harden, making it difficult
to bend or stretch them anymore.
• Do not bend or stretch the pipes more than 3 times.
CAUTION
To prevent breaking of the pipe, avoid sharp bends.
If the pipe is bent repeatedly at the same place, it will break.
4.3.3. Pipe connection
CAUTION
Be sure to install the pipe against the port on the indoor unit correctly. If the centering
is improper, the flare nut cannot tighten smoothly. If the flare nut is forced to turn, the
threads will be damaged.
Do not remove the flare nut from the indoor unit pipe until immediately before connect
-
ing the connection pipe.
Hold the torque wrench at its grip, keeping it at a right angle with the pipe, in order to
tighten the flare nut correctly.
Connect the piping so that the control box cover can easily be removed for servicing
when necessary.
In order to prevent water from leaking into the control box, make sure that the piping is
well insulated.
When the flare nut is tightened properly by
your hand, hold the body side coupling with a
separate spanner, then tighten with a torque
wrench. (Refer to the following table for the
flare nut tightening torques.)
Tighten with 2
wrenches.
Holding
wrench
Flare nut
Connection pipe
Indoor unit pipe
(body side)
Torque
wrench
Flare nut
[mm (in)]
Tightening torque
[N·m (kgf·cm)]
6.35 (1/4) dia.
16 to 18 (160 to 180)
9.52 (3/8) dia.
32 to 42 (320 to 420)
12.70 (1/2) dia.
49 to 61 (490 to 610)
15.88 (5/8) dia.
63 to 75 (630 to 750)
19.05 (3/4) dia.
90 to 110 (900 to 1,100)
9384723017_IM.indb 4
14-Oct-20 13:29:49