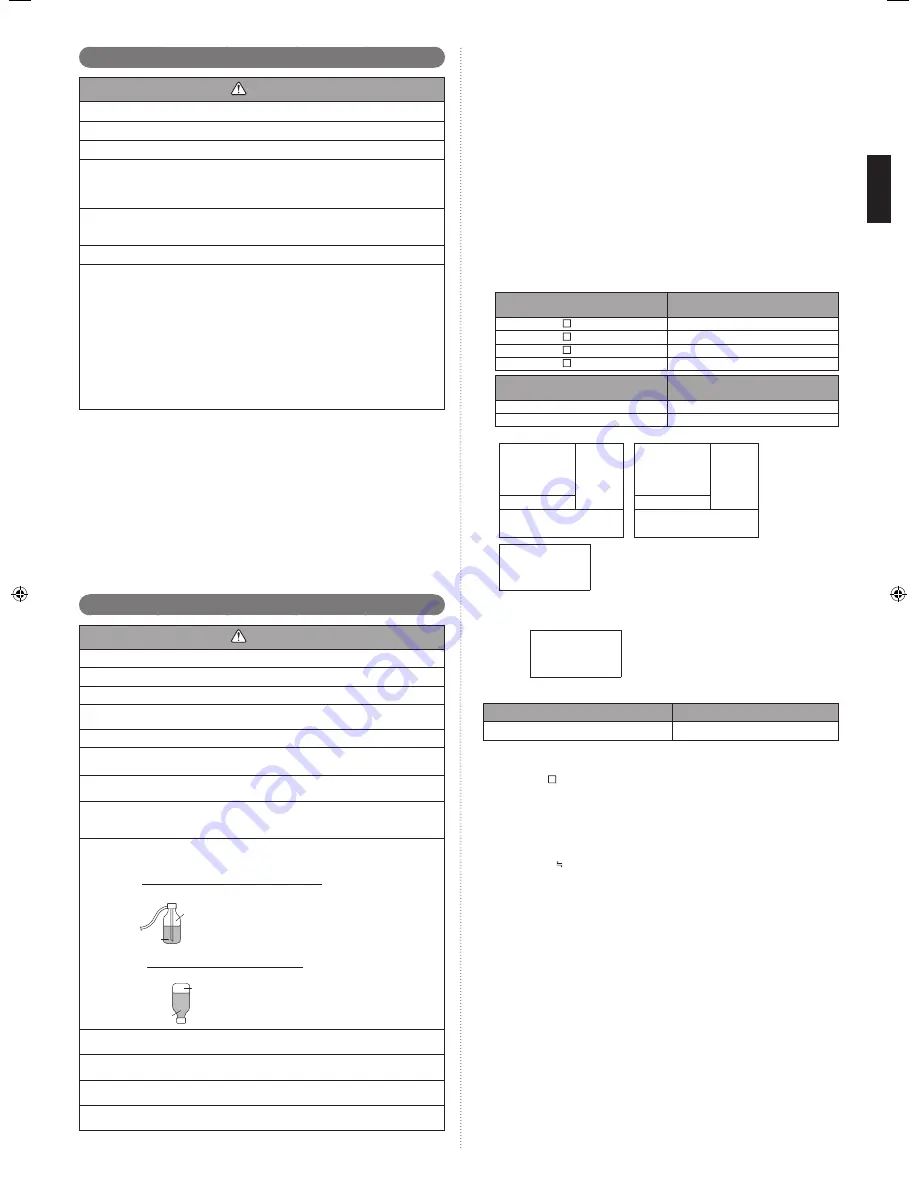
En-18
Vacuum process
8. 2.
CAUTION
Do not turn on the power unless all operations are complete.
If the system is not evacuated suf
fi
ciently, its performance will drop.
Be sure to evacuate the refrigerant system using a vacuum pump.
The refrigerant pressure may sometimes not rise when a closed valve is opened after
the system is evacuated using a vacuum pump. This is caused by the closure of the
refrigerant system of the outdoor unit by the electronic expansion valve. This will not
affect the operation of the unit.
Use a clean gauge manifold and charging hose that were designed speci
fi
cally for
use with R410A. Using the same vacuum equipment for different refrigerants may
damage the vacuum pump or the unit.
Do not purge the air with refrigerants, but use a vacuum pump to evacuate the system.
If moisture might enter the piping, follow below. (i.e., if doing work during the rainy
•
season, if the actual work takes long enough that condensation may form on the
inside of the pipes, if rain might enter the pipes during work, etc.)
After operating the vacuum pump for 2 hours, pressurize to 0.05 MPa (i.e., vacuum
•
breakdown) with nitrogen gas, then depressurize down to -100.7kPa (-755mmHg)
for an hour using the vacuum pump (vacuum process).
If the pressure does not reach -100.7kPa (-755mmHg) even after depressurizing
•
for at least 2 hours, repeat the vacuum breakdown - vacuum process.
After vacuum process, maintain the vacuum for an hour and make sure the pressure
does not rise by monitoring with a vacuum gauge.
Evacuation procedure
Remove
(1)
the blank caps of the gas pipe and liquid pipe and check that the valves
are closed.
Remove the charging port cap.
(2)
Connect a vacuum pump and a pressure gauge to a charging hose and connect it
(3)
to the charging port.
Activate the vacuum pump and vacuum the indoor unit and connection piping until
(4)
the pressure gauge becomes -100.7kPa (-755mmHg).
Evacuate from both the gas pipe and the liquid pipe.
Continue evacuating the system for 1 hour after the pressure gauge reads
(5)
-100.7kPa (-755mmHg).
Remove
(6)
the
charging
hose
and
reinstall the charging port cap.
Additional charging
8. 3.
CAUTION
Do not turn on the power unless all operations are complete.
After evacuating the system, add refrigerant.
Do not charge the system with a refrigerant other than R410A.
Always keep to the limit on the total amount of refrigerant. Exceeding the limit on the
total amount of refrigerant will lead to malfunction during charging of refrigerant.
Do not reuse recovered refrigerant.
Use an electronic scale to measure the charging amount of refrigerant.
Adding more refrigerant than the speci
fi
ed amount will cause a malfunction.
Charge refrigerant using the liquid pipe.
Adding refrigerant through the gas pipe will cause a malfunction.
Add refrigerant by charging the system with the refrigerant in the liquid state. If the
refrigerant cylinder is equipped with a siphon, it is not necessary to place the cylinder
upright.
Check if the steel cylinder has a siphon installed or not before
fi
lling. (There is an
indication “with siphon for
fi
lling liquid” on the steel cylinder.)
Filling method for cylinder with siphon
Set the cylinder vertical and
fi
ll with the
liquid.
(Liquid can be
fi
lled without turning bot-
tom up with the siphon inside.)
Liquid
Gas
R410A
Filling method for other cylinders
Turn bottom up and
fi
ll with liquid.
(Be careful to avoid turning over the
cylinder.)
Liquid
Gas
R410A
Be sure to use the special tools for R410A for pressure resistance and to avoid mix-
ing of impure substances.
If the units are further apart than the maximum pipe length, correct operation can not
be guaranteed.
Make sure to back closing valve after refrigerant charging. Otherwise, the compressor
may fail.
Minimize refrigerant release to the air. Excessive release is prohibited under the
Freon Collection and Destruction Law.
Procedure for charging the system with refrigerant
8. 3. 1.
Remove the charging port cap from the liquid pipe.
(1)
Attach a charging hose to the refrigerant cylinder, and connect it to the charging port.
(2)
Add refrigerant by calculating the additional refrigerant volume in accordance with
(3)
the calculation formula indicated below.
Remove the charging hose and install the charging port cap.
(4)
Remove the blank caps (gas pipe and liquid pipe) and open the valves.
(5)
Close the blank caps.
(6)
After adding refrigerant, indicate the added charging volume on the unit.
(7)
Tighten the blank caps and charging port caps to the torque values speci
fi
ed in the
*
Table A.
To open and close the valves,
Use an M4 hexagon wrench.
Checking total amount of refrigerant and calculating
8. 3. 2.
the amount of refrigerant charge to be added
The amount of refrigerant charge to be added is the total value of the basic refriger-
•
ant charge amount and the value calculated from the length of the liquid pipe.
Round up the value to 2 dec
• imal
places.
Model
B
Factory charged amount (kg)
AJ A36LALH
4.80
AJ A40LALH
4.80
AJ A45LALH
5.30
AJ A54LALH
5.30
Diameter of liquid pipe (mm)
a
Additional amount for pipe length (kg/m)
Ø6.35
0.021
Ø9.52
0.058
Calculation of additional amount for pipe length
(1)
A =
Total length of
ø9.52 mm
liquid pipe
a
× 0.058
(kg/m)
m
kg
+
Total length of
ø6.35 mm
liquid pipe
a
× 0.021
(kg/m)
m
kg
=
Total
kg
(Round up A to 2 decimal place)
Calculation of total refrigerant amount
(2)
C = A+B =
kg
(B : Factory charged amount)
Note: Check the total refrigerant amount under the following conditions
Condition
Computational formula
Total amount of refrigerant
C <
= 15.7kg
<Calculation>
Outdoor unit: AJ A54LALH
Calculation of additional amount for outdoor unit
(1)
If liquid pipe piping length is the following
Φ
9.52: 50m ,
Φ
6.35: 35m
Additional charge volume:
A=50(m) × 0.058(kg/m)+35(m) × 0.021(kg/m)
=3.635kg
3.64kg
Check the total amount of refrigerant
(2)
C=A+B=3.64kg+5.30kg=8.94kg <
= 15.7kg
→
No problem if the above condition is satis
fi
ed.
9380545026-02_IM.indb 18
9380545026-02_IM.indb 18
19/08/2013 17:20:10
19/08/2013 17:20:10