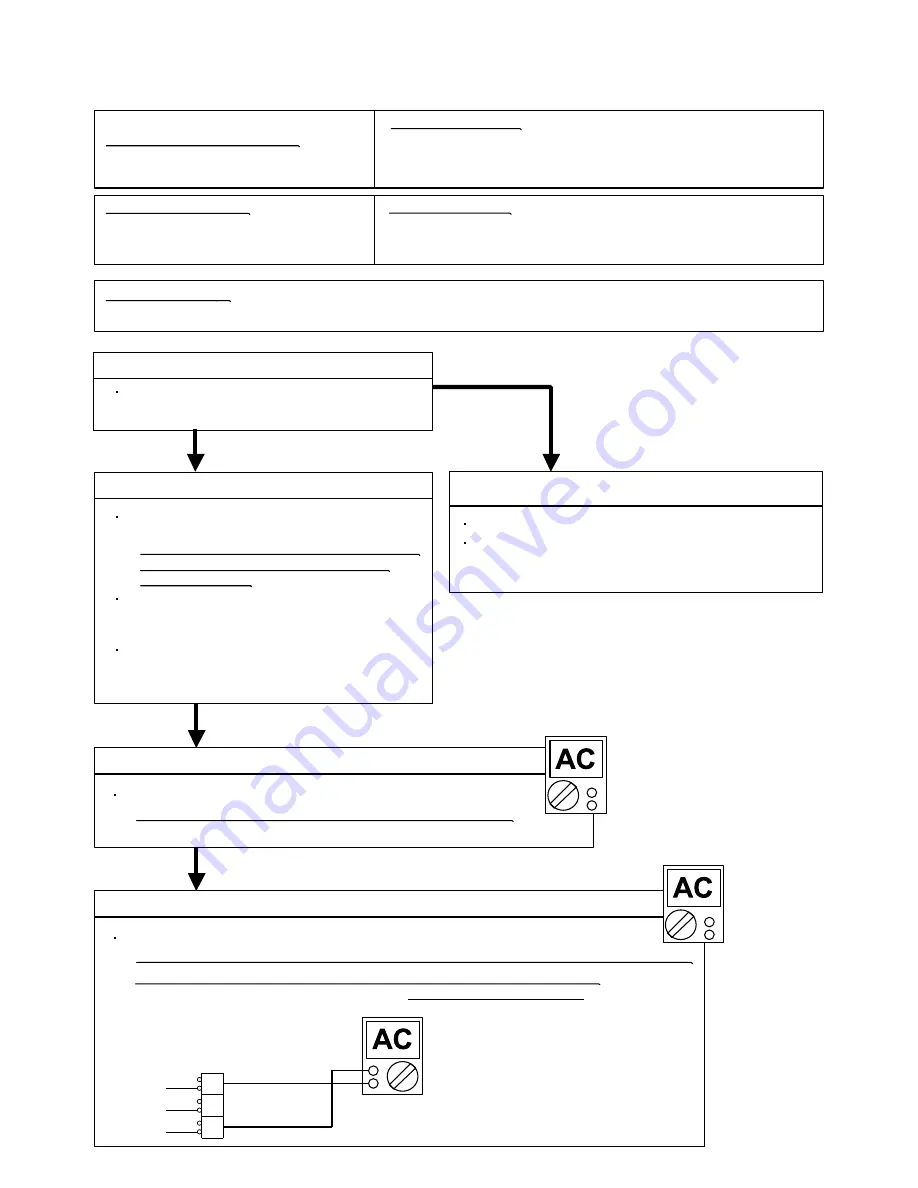
Trouble shooting 11
INDOOR UNIT Error Method:
Detective Actuators:
Detective details:
Forecast of Cause:
Check Point 2 : Check Connection
OK
Indicate or Display:
Indicate or Display:
Refer to error code table.
Check Point 3 : Check the voltage of power supply
Check Point 1-1 : Reset the power
YES
YES
NO
Check Point 1-2:
OK
Check Point 4 : Check Serial Signal (Forward Transfer Signal)
Check Serial Signal (Forward Transfer Signal)
Outdoor Communication Signal Error
(Forward Transfer Signal Error)
Indoor Unit Control PCB (AS,AR),
Main PCB, Power PCB (AU) Circuit
1. Connection failure 2. External cause 3. Controll PCB (AS,AR), Main PCB, Power PCB (AU) failure
Does Error indication reappear?
Check external cause such as noise
Check the complete insulation of the grounding.
Check if there is any equipment that causes harmonic wave
near the power cable (Neon light bulb or any electronic
equipment which causes harmonic wave).
Check the voltage of power supply
>> Check if AC208 - 230V appears at Outdoor Unit Terminal L - N.
>> Check if Indicated value swings between AC70V and AC130V at Outdoor Unit Terminal N - 3.
Check any loose or removed connection line of
Indoor unit and Outdoor unit.
>> If there is an abnormal condition, correct it by
referring to Installation Manual or Data &
Technical Manual.
Check connection between Indoor Unit Control PCB
and Filter PCB.(AR)
(If there is loose connector or open cable)
>> If it is abnormal, Controller PCB is failure. >> Replace Control PCB (AS,AR),
Main PCB , Power PCB (AU)
02-18
When the outdoor unit cannot receive the serial signal from Indoor unit
more than 10seconds.
N
L
3
WHITE
BLACK
RED
+
-
Check connection between Indoor Unit Main PCB
and Power PCB.(AU)
(If there is loose connector or open cable)
Summary of Contents for Inverter Halcyon ASU12RMLQ
Page 3: ...1 DESCRIPTION OF EACH CONTROL OPERATION R410A WALL MOUNTED DUCT CASSETTE type INVERTER MULTI ...
Page 26: ...2 TROUBLE SHOOTING R410A WALL MOUNTED DUCT CASSETTE type INVERTER MULTI ...
Page 76: ...3 REPLACEMENT PARTS R410A WALL MOUNTED DUCT CASSETTE type INVERTER MULTI ...
Page 77: ...REPLACEMENT PARTS 03 01 Models ASU9RMLQ ASU12RMLQ ASU18RMLQ INVERTER ...
Page 78: ...REPLACEMENT PARTS 03 02 Models ASU9RMLQ ASU12RMLQ ASU18RMLQ ...
Page 79: ...Model ARU9RML 03 03 REPLACEMENT PARTS ...
Page 80: ...Model ARU9RML 03 04 REPLACEMENT PARTS ...
Page 81: ...Models ARU12RML ARU18RML 03 05 REPLACEMENT PARTS ...
Page 82: ...Models ARU12RML ARU18RML 03 06 REPLACEMENT PARTS ...
Page 83: ...Models ARU9RML ARU12RML ARU18RML 03 07 REPLACEMENT PARTS ...
Page 84: ...40 Models AUU9RML AUU12RML AUU18RML REPLACEMENT PARTS ...
Page 85: ...41 Models AUU9RML AUU12RML AUU18RML CONTROL UNIT REPLACEMENT PARTS ...
Page 86: ...38 CASSETTE TYPE DECORATION PANEL UTG UFUB W REPLACEMENT PARTS ...
Page 88: ...REPLACEMENT PARTS 03 08 Model AOU24RML AOU24RML1 ...
Page 89: ...REPLACEMENT PARTS 03 09 Model AOU24RML AOU24RML1 ...
Page 90: ...REPLACEMENT PARTS 03 10 Model AOU24RML AOU24RML1 ...
Page 92: ...REPLACEMENT PARTS 03 12 Model AOU36RML AOU36RML1 ...
Page 93: ...REPLACEMENT PARTS 03 13 Model AOU36RML AOU36RML1 ...
Page 94: ...REPLACEMENT PARTS 03 14 Model AOU36RML AOU36RML1 ...
Page 141: ...4 APPENDING DATA R410A WALL MOUNTED DUCT CASSETTE type INVERTER MULTI 1 PT CHART ...
Page 145: ...1116 Suenaga Takatsu ku Kawasaki 213 8502 Japan GS06082006 JUN 2006 Printed in Japan ...