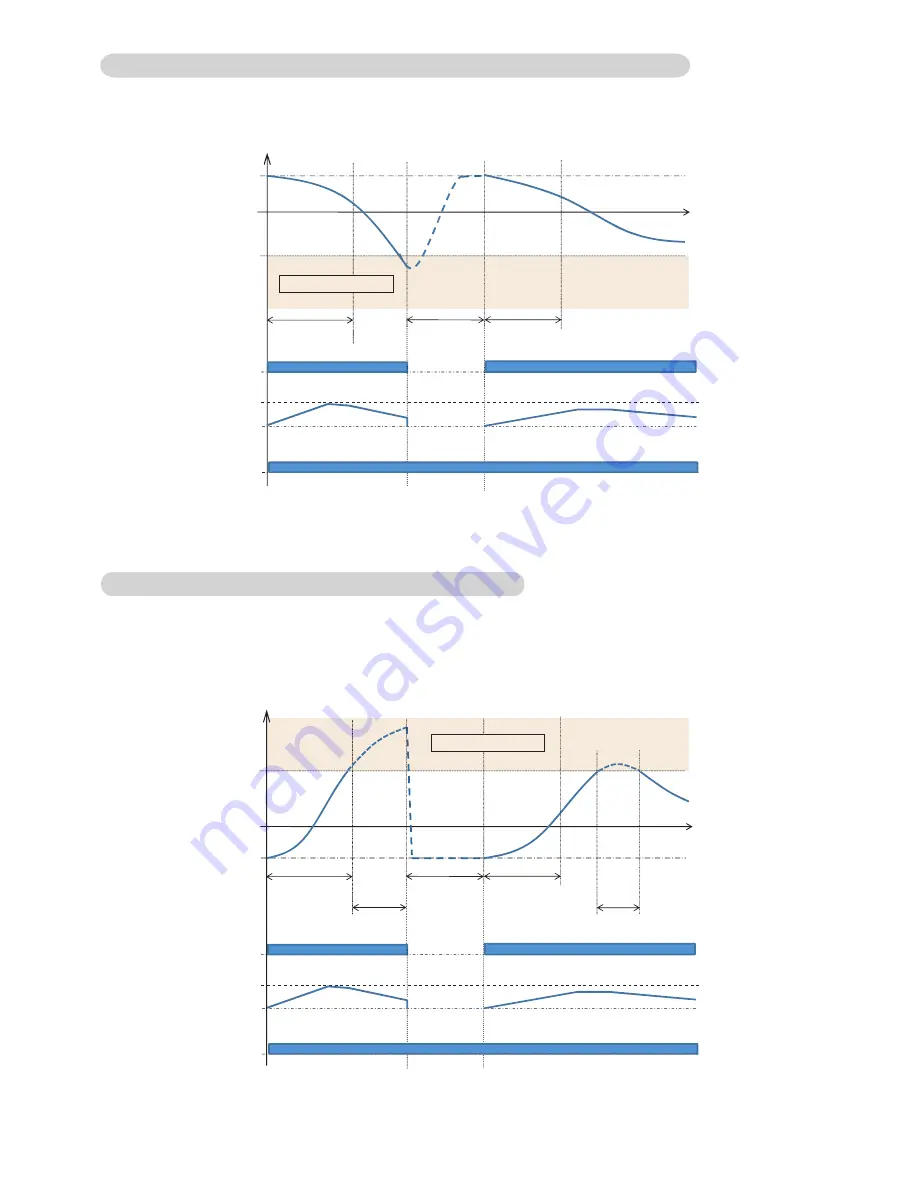
03-09
3-2-4 "COOL" Position for Outdoor air unit
An example for COOLING TEMPERATURE CONTROL time chart (Manual setting)
When using the cooling mode, set the temperature to a value lower than the discharge airflow temperature, otherwise
the outdoor air unit will not start the cooling operation and only the fan will rotate.
•
Outdoor air unit
fan
Ts
•
Opening of
EEV
100%
0%
•
Refrigerant
flow
ON
OFF
ON
OFF
•
Discharge airflow
Temperature
Outdoor temp.
Ts : Corrected setting temperature
Ts - 5°C
Ts + 0.5°C : The thres hold temperature of start of refrigerant flow
Ts - 5°C : The thres hold temperature of stop of refrigerant flow
3-2-5 "HEAT" Position for Outdoor air unit
(1) When using the heating mode, set the temperature to a value higher than the discharge airflow temperature, otherwise
the outdoor air unit will not start the heating operation.
(2)
An example for HEATING TEMPERATURE CONTROL time chart (Manual setting)
During defrosting, the OPERATION indicator lamp flashes 6 sec. ON and 2 sec. OFF, and repeat. The heating operation
will be temporarily interrupted.
Excess capacity area
Compressor ON
(6 minutes)
Compressor ON
(6 minutes)
Compressor OFF
(3 minutes)
Compressor ON
(6 minutes)
5 minutes has passed
at excess capacity area
5 minutes has passed
at excess capacity area
Compressor ON
(6 minutes)
Compressor OFF
(3 minutes)
•
Outdoor air unit
fan
Ts
•
Opening of
EEV
100%
0%
•
Refrigerant
flow
ON
OFF
ON
OFF
•
Discharge airflow
Temperature
Outdoor temp.
Ts : Corrected setting temperature
Ts +5°C
Ts - 0.5°C : The thres hold temperature of start of refrigerant flow
Ts + 5°C for 5 minutes or more
: The thres hold temperature of stop of refrigerant flow
Excess capacity area
Summary of Contents for UTP-VX30A
Page 1: ...SERVICE MANUAL ...
Page 5: ...1 TEST RUN ...
Page 27: ...2 OUTDOOR UNIT OPERATION CONTROL ...
Page 40: ...3 INDOOR UNIT OPERATION ...
Page 70: ...4 TROUBLE SHOOTING ...
Page 205: ...5 APPENDING DATA ...
Page 210: ...05 04 1 MODELS AUXK018 024 030 034 036 045 054GLAH AUXM018 024 030GLAH CASSETTE TYPE ...
Page 214: ...05 07 LOW STATIC PRESSURE DUCT TYPE MODEL ARXB24GALH ARXB30GALH ARXB36GALH MODEL ARXB45GALH ...
Page 217: ...05 10 MODEL ARXC36GBTH MODELS ARXC72GBTH ARXC90GBTH ...
Page 218: ...05 10 1 MODELS ARXK04 07 09 12 14 18 24GCLH COMPACT SLIM DUCT TYPE ...
Page 219: ...FLOOR CEILING TYPE MODELS AB A12GATH AB A14GATH AB A18GATH AB A24GATH 05 11 ...
Page 220: ...CEILING TYPE MODELS AB A30GATH AB A36GATH AB A45GATH AB A54GATH 05 12 ...
Page 222: ...05 14 WALL MOUNTED TYPE MODELS AS A04GACH AS A07GA H AS A09GA H AS A12GA H AS A14GA H ...
Page 223: ...05 15 MODELS AS A18GA H AS A24GA H AS A30GA H ...
Page 224: ...05 15 1 MODELS ASYA004 007 009GTAH ASHA004 007 009GTAH COMPACT WALL MOUNTED TYPE EEV internal ...
Page 225: ...05 15 2 MODELS ASYE004 007 009GTAH ASHE004 007 009GTAH COMPACT WALL MOUNTED TYPE EEV external ...
Page 227: ...05 15 4 MODELS ASYA030 034GTAH ASHA030 034GTAH ...
Page 230: ...05 16 MODEL ARXH054GTAH OUTDOOR AIR UNIT MODEL ARXH072GTAH ...
Page 231: ...05 17 MODEL ARXH096GTAH ...
Page 232: ...MODELS AJ 072LELAH AJ 090LELAH UNITS 5 2 2 Outdoor Unit 05 18 ...
Page 233: ...MODEL AJ 108LELAH OUTDOOR 05 19 ...
Page 240: ...6 DISASSEMBLY PROCESS ...