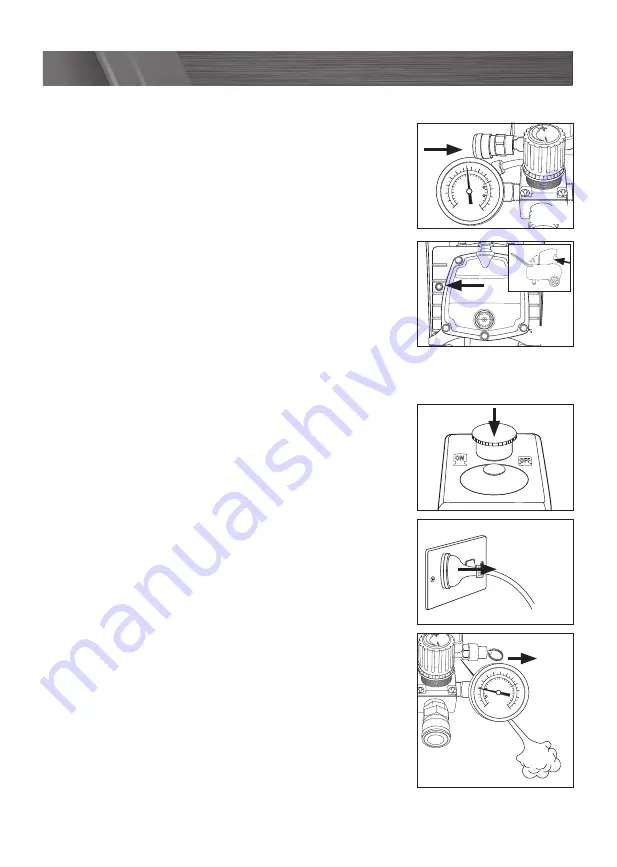
15
Unregulated quick lock coupling
Air tools can also be attached to the unregulated quick lock
coupling (14) (Fig. 26), but the output pressure level may
fluctuate.
Overload switch
The motor is fitted with an overload switch (17). If the
compressor overloads, the overload switch turns off the
equipment automatically to protect the compressor. If the
overload switch triggers, switch off the compressor using the
ON/OFF switch (9) and wait until the compressor cools down.
Then press the overload switch (17) and restart the compressor
(Fig. 27).
Note.
Long supply cables, extensions, cable reels etc. cause a drop in voltage and can
impede motor start-up.
Turning off
1. After the task has been completed, switch off the
compressor by pressing down the on/off switch (9) (Fig. 28).
2. Wait for the pressurised air to bleed from the release valve
under the pressure switch cover.
3 Switch off the power supply and remove the electrical
plug (Fig. 29).
4. Pull the ring on the safety valve (11) outwards, releasing
the remaining compressed air in the tank. Release the ring
so that the safety valve closes (Fig. 30).
Psi
Bar
10
8
6
4
2
0
50
100
150
200
12
14
Psi
Bar
10
8
6
4
2
0
50
100
150
200
12
14
OPERATION
Psi
Bar
10
8
6
4
2
0
50
100
150
200
12
14
Psi
Bar
10
8
6
4
2
0
50
100
150
200
12
14
Psi
Bar
10
8
6
4
2
0
50
100
150
200
12
14
Psi
Bar
10
8
6
4
2
0
50
100
150
200
12
14
Fig. 26
Fig. 27
Fig. 28
Fig. 29
Fig. 30