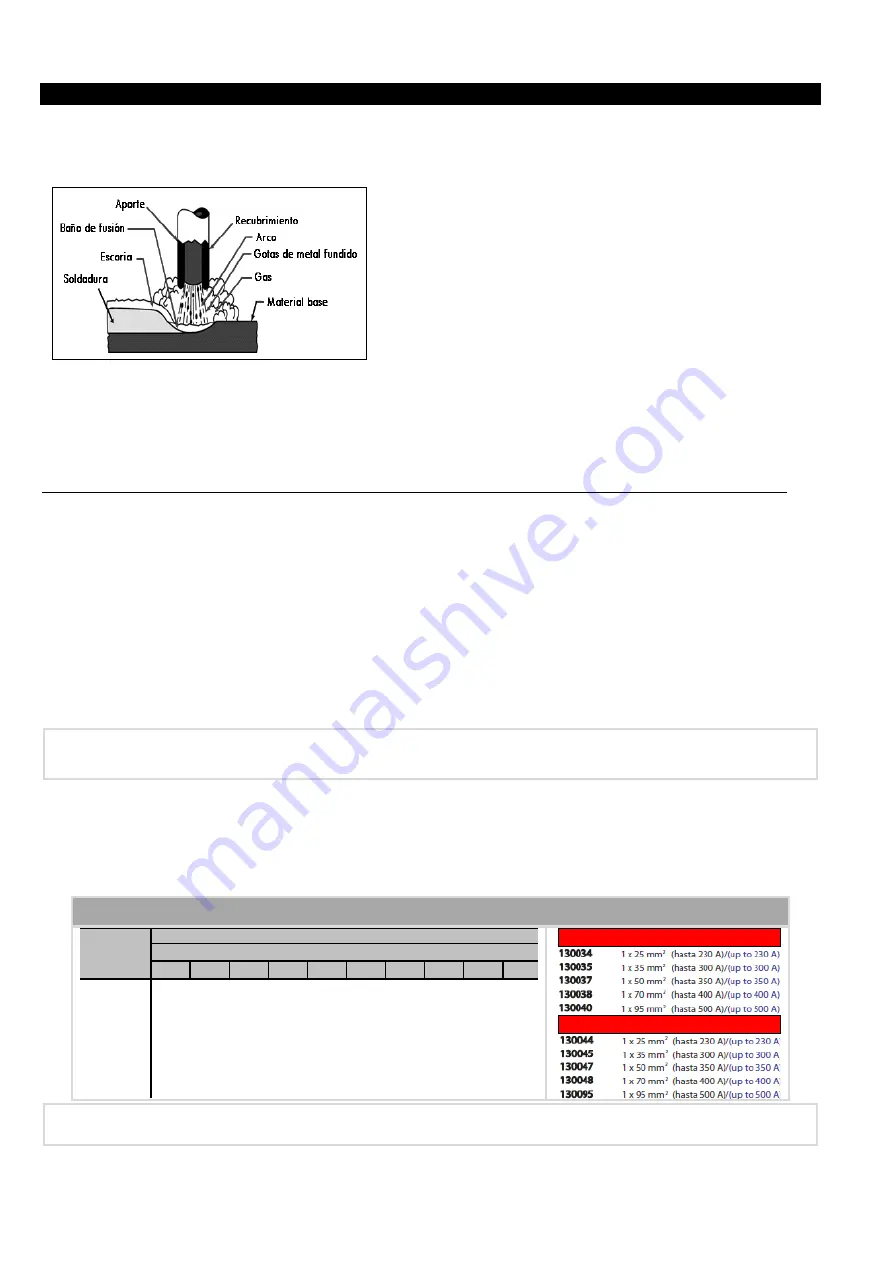
TIG 3200 AC/DC
50
6. WELDING MMA.
Coated electrode welding, also known as MMA (Manual Metal Arc), SMAW or process 111, take part of the arc welding
processes. Therefore we must bearing in mind the fundamental principles of the process before beginning the requested
welding work.
Coated electrode arc welding it is a process in which the metal fusion
occurs between the part and a coated metal electrode.
As the electric current flows through the electrode, there is a heat
build-up at the end of the electrode which produces an arc that melts
the electrode rod or rod and burns the electrode coating.
So, a suitable atmosphere is obtained for transfering of molten metal
from the electrode core to the melt bath in the base material.
These droplets of molten metal fall coated with molten slag from the arc coating melting. The slag floats on the surface
and forms, above the weld bead, a protective layer of the molten metal, controlling the speed of cord cooling and
avoiding the oxidation of the supplied metal.
APLICATIONS
This welding process is especially recommended for welding repair and maintenance, production and installation of
pipes, mounts on outside work. Welding production and repair in shipbuilding, storage tanks, structures, pressure ves-
sels, oil refineries, boilers and any type of pipeline are any of its sectors of application.
The main process features are its simplicity and low price, making it a practical and excellent procedure for Offshore
use or outdoor work.
However, the coated electrode welding procedure does not lend itself to automation or semi automation; its application
is manual essentially.
In case of using electrodes in less favorable conditions (with humidity, without preheating, etc.) we can improve the
welding performance with a setting of control parameters in manual process.
Hot Start: Increase the starting intensity by a percentage to facilitate priming.
Arc Force: Reduce the arc decompensation caused by variations in height by adjusting tension.
We respect the appropriate cable sections for each welding current. Since the movement of electric charges during the
welding phase is restricted by the resistance of the conducting wire.
This resistance is greater when:
1.
Its length is larger.
2.
Minor diameter.
3.
Less conductive is the cable.
GRAPH RECOMMENDATION WELDING CABLE SECTION.
The voltage drop in the welding circuit, will cause reductions of intensity in the welding arc and it will force us to
increase the intensity of output in the machine, reducing the gear factor of the equipment.
Amperios
15
25
30
40
50
60
70
80
90
100
100
25
25
35
35
35
35
50
50
50
50
150
35
35
50
50
50
50
70
70
200
35
50
50
70
70
70
250
35
50
70
70
70
300
50
70
95
95
350
50
70
95
400
50
70
95
Distancia entre máquina y lugar de trabajo (metros)
Sección mímima necesaria mm²
Intensidad
ACRÍLICO
GOMA