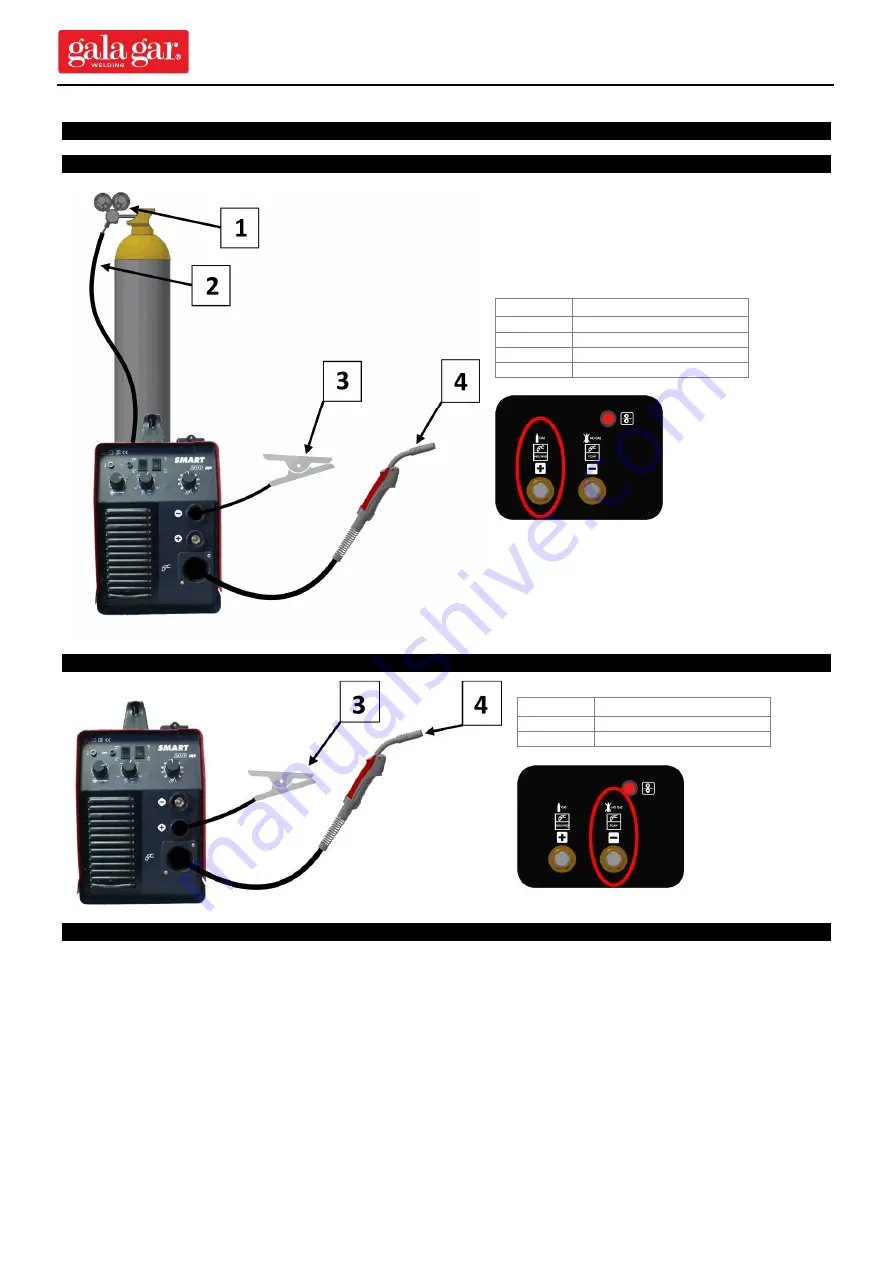
SMART 200 MP
19
3.2 MIG/MAG WELDING. INSTALLATION AND START-UP
3.2.1 INSTALLATION OF STANDARD MIG/MAG SYSTEM WITH GAS. TORCH TO POSITIVE POLE.
MARK
MARK
MARK
MARK
DESCRIPTIO N
DESCRIPTIO N
DESCRIPTIO N
DESCRIPTIO N
1
Pressure reducing va lve
2
Ma chine-ga s connection
3
Ea rth clamp ca ble
4
MIG/MAG Torch
3.2.2 INSTALLATION OF (FCAW) MIG/MAG SYSTEM WITHOUT GAS. TORCH TO NEGATIVE POLE.
MARK
MARK
MARK
MARK
DESCRIPTIO N
DESCRIPTIO N
DESCRIPTIO N
DESCRIPTIO N
3
Ea rth clamp ca ble
4
MIG/MAG Torch
3.2.3. MIG/MAG SYSTEM START-UP.
1) Make sure the mains voltage is 230 V.
2) Connect supply cable with the suitable plug to the relevant single-phase tap. See section 2.2.
3) Change the polarity if it is necessary. The torch must be to positive in MIG/MAG with gas process.
4) If the material to be welde d is aluminium, change the flexible cable and the wire guide tube for the graphite
cable with the torch totally stretched.
5) Depe nding on the wire diameter, fit the groove of the suitable driving wheel to the work to be carried out.
6) Choose suitable gas to wire type to be welde d. If it has a mobile workstation, check that the gas bottle is securely
held by the bottle-holde r system. Above all check that the safety chain is pe rfectly fastened.
7) Install the pressure-reducing valve and connect gas hose checking that there are no leakages, throughout the
whole circuit.
8) Fit the wire reel into the suppo rt axle.
9) Fit the welding wire into the driving system. Do not force the wire pressure handle, as if this is too tight, the motor
remains on overload and does not reach the maximum spe ed, and if the handle is too slack, the wire could slip.
10) Once the wire has be en fitted, we can then conect the MIG/MAG torch. The wire is loade d into the torch via the
wire purge pushbutton.