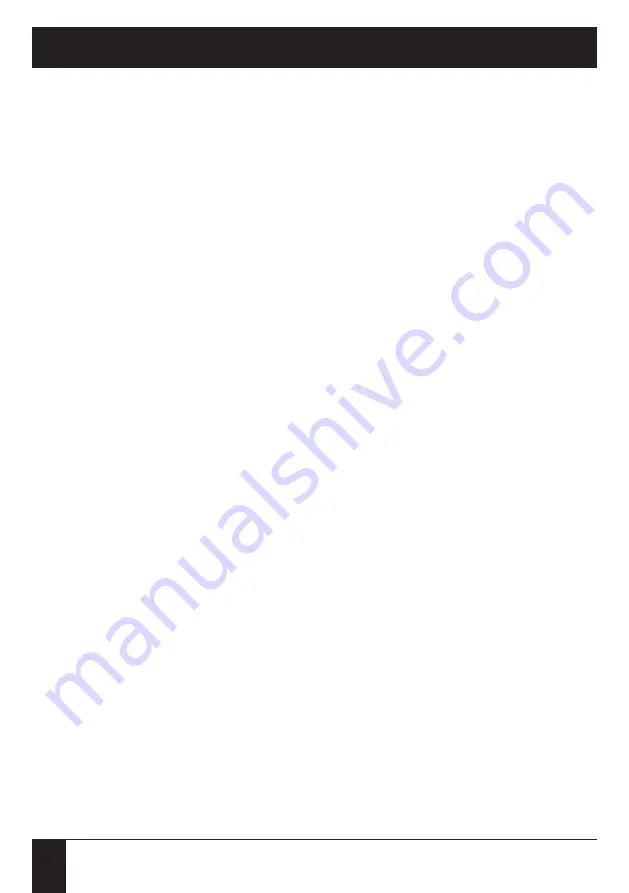
Installation and Operating Manual / Warranty Card - SGW(S), SGW(S)B, SG(S)
© All rights reserved - Galmet Sp. z o.o. Sp. K.
4
even those factory sealed.
The heater can work in an open system (pt. 2.1) or in a closed system including an expansion vessel (pt. 2.2). In winter, when there is a possibility of the water
freezing, the water should be drained by removing the drain plug Ks (pt. 2.1 and 2.2).
1.5. Remember
1. Before installation of the heater it is recommended to read the installation and user manual that comes with the device.
2. Do not start using a water heater that is not filled with water.
3. Do not operate the water heater without a fully operational relief valve (proper functioning of the relief valve must be checked every 14 days by turning
its cap left or right to induce an outflow of water from a discharge port located on the side of the valve. Following that, turn the cap in the opposite
direction until it snaps in place and press down to the valve body. If there is not outflow of water while turning the cap, the valve is not operational. A
continuous outflow of water after returning the cap to its previous position indicates valve head contamination. In such a case, flush the valve several
times by turning the cap to open the outflow of water. Caution - there is a possibility of hot water outflow. The company will not be responsible for
improper functioning of the relief valve caused by wrong installation or errors within the system, e.g. missing a pressure reducing valve in the cold water
removal system. The maximum pressure of full opening of relief valve must not exceed 0,7 MPa (100-140 l water heaters) and 0,97 MPa (200-1500 l
water heaters).
4. If there is a cold water system, supplying it to the heater, check valve or other device functioning as a check valve such as a pressure reducer must be
installed in the water bulk expansion vessel with a capacity of at least 5 % of the capacity of the boiler.
5. Installations equipped with a water heater cannot include devices that cause a "hydraulic stroke", f.ex. a ball valve used as a drain valve.
6. Do not prevent water from dripping from the relief valve – do not plug the discharge port of the relief valve. If water continuously leaks from the
relief valve, it indicates that the water main system pressure is too high, or that the relief valve is defective. Discharge port of the relief valve should
be oriented downwards. It is recommended to place a funnel underneath the relief valve to collect and drain water. A hose can also be fitted over the
discharge port to remove water flowing when the relief valve is being opened. The hose should be heat resistant up to +80°C, with internal diameter
of 9 mm and max. length of 1,2 m, run to a drain with a downgrade (min. 3%) in an environment of temperature not lower than 0°C. The hose must be
protected against bottlenecking (squeezing, plugging) and its discharge end should be visible (in order to verify operation of the valve).
7. The water quality shall be in accordance with the Regulation of the Minister of Health of 29 March 2007.
8. Conductivity should not be less than 100 uS / cm, this will ensure the proper operation of the magnesium anode.
9. Immediately turn off the heater if the tap emits steam (it should be reported to the manufacturer or to a designated service).
10. Continuous operation at a maximum temperature results in faster wear of electrical parts and the tank itself.
11. Adequate protection of the CH boiler connected to the tank ensures proper security of the water heater's spiral coils.
12. It is forbidden to connect the coil to the installation which does not meet one of the following standards: PN−91/B−02413 or PN−91/B−02414.
13. At least once every 12 months the water heater should be rinsed from the sediment.
14. Pollution filters should be used in order to extend the life of the tank and ensure the smooth operation of the safety valve.
15. „Galmet Sp. z o. o.” Sp. K. reserves the right to introduce any modification without prior notification.
16. Before starting operation of the heater, the user is required to read this document, it must be kept on-site and be accessible to the service.
17. The heating coil should be flushed by the installer before the first use (besides, installing a filter is recommended to remove any impurities). If the
heating coil is not used (e.g. due to the use of an electric resistance heater), it must be completely filled with an appropriate glycol mixture in order to
prevent corrosion caused by condensed water. After filling, the heating coil must not be closed on both sides (thermal expansion of air).
18. The tank has an outer casing made of artificial leather (skay, PVC foil), while the thermal insulation is made of polyurethane or polystyrene foam. It is
not allowed to manipulate open fire directly next to the tank, as it may damage the outer casing as well as the thermal insulation
19. All maintenance and installation works must be performed in accordance with applicable health and safety regulations.
20. Unpleasant scents and darkening of the water from the heater may be the result of a hydrogen sulphide, which is formed by reducing the sulphate
content of bacteria that live in oxygen-free water. If cleaning the tank, replacing the magnesium anode and starting with a temperature above 60°C will
not yield result, we recommend using a titanium anode.
1. Operation and service