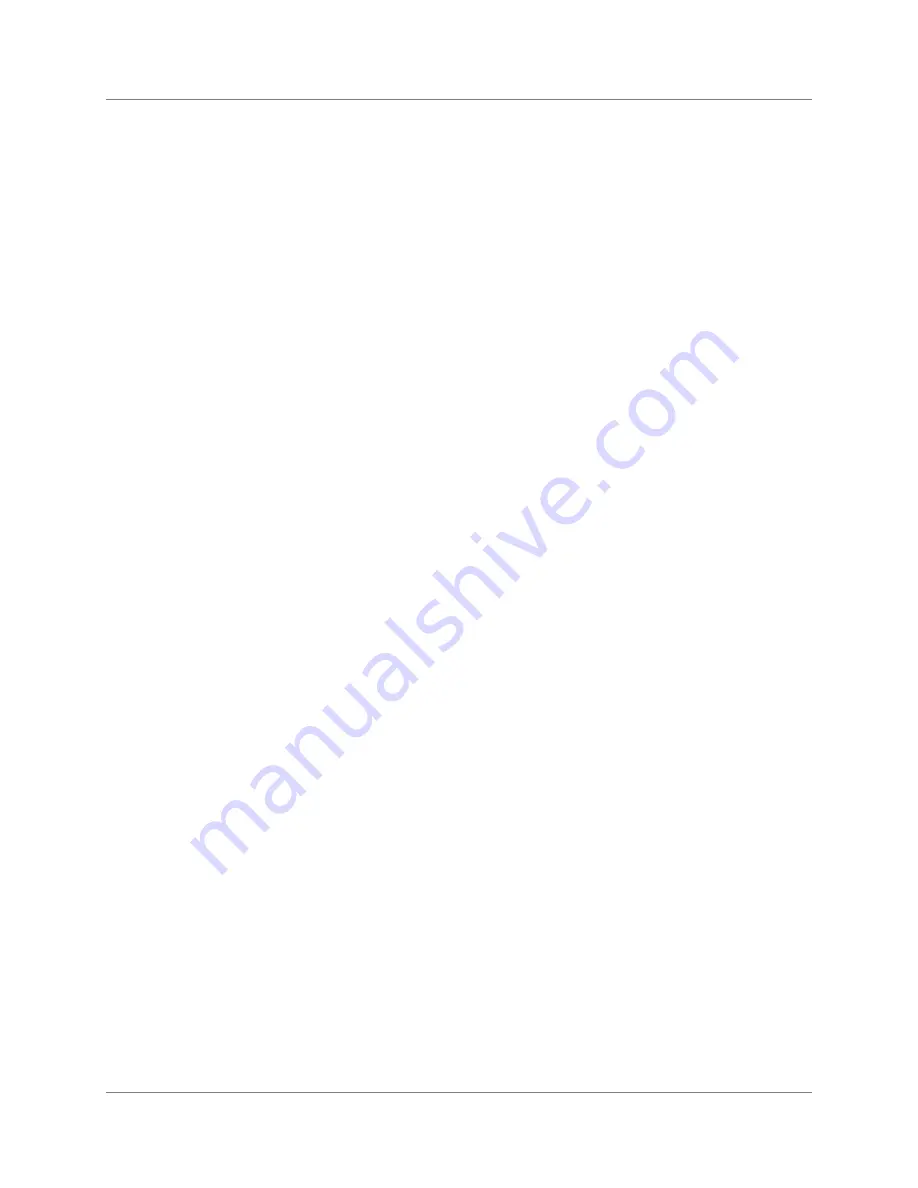
2
0
CAUTION: REFRIGERANT!
If
both
suction
and
discharge
pressures
are
low
but
sub
‐
cooling
is
normal,
a
problem
other
than
refrigerant
shortage
exists.
Do
not
add
refrigerant,
as
this
may
result
in
overcharging
the
circuit.
Use
only
the
refrigerant
specified
on
the
unit
nameplate.
Contact
G&D
for
the
recommended
oil
type
or
refer
to
the
data
plate
on
the
compressor
for
your
specific
chiller.
Failure
to
do
so
may
cause
compressor
damage
and
improper
unit
operation.
WARNING: HAZARDOUS VOLTAGE!
Disconnect
all
electric
power,
including
remote
disconnects
before
servicing.
Follow
proper
lock
‐
out/tagout
procedures
to
ensure
the
power
cannot
be
inadvertently
energized.
Failure
to
disconnect
power
before
servicing
could
result
in
death
or
serious
injury.
FREEZE PROTECTION
The
chiller
system
must
be
protected
from
freezing
by
use
of
a
freeze
inhibitor.
The
solution
must
be
strong
enough
to
provide
protection
against
ice
formation
at
the
lowest
anticipated
ambient
temperature,
and
at
least
20°
cooler
than
the
lowest
set
point.
A
minimum
of
35%
Propylene
Glycol
is
required.
Do
not
exceed
40%.
NOTICE: Equipment Damage!
In
order
to
provide
freeze
protection
in
the
event
of
a
power
loss
you
MUST
use
sufficient
freeze
inhibitor
in
the
chiller.
NORMAL SHUTDOWN
1. Perform
the
normal
unit
stop
sequence
using
the
chiller
pump
down/run
switch.
2. Verify
that
the
chiller,
and
process
pumps
are
cycled
off.
3. Verify
that
the
oil
heaters
are
working.
Note:
Do
not
open
the
external
chiller
disconnect
switch.
This
must
remain
closed
to
provide
control
power
from
the
control
power
transformer
to
the
oil
heaters.