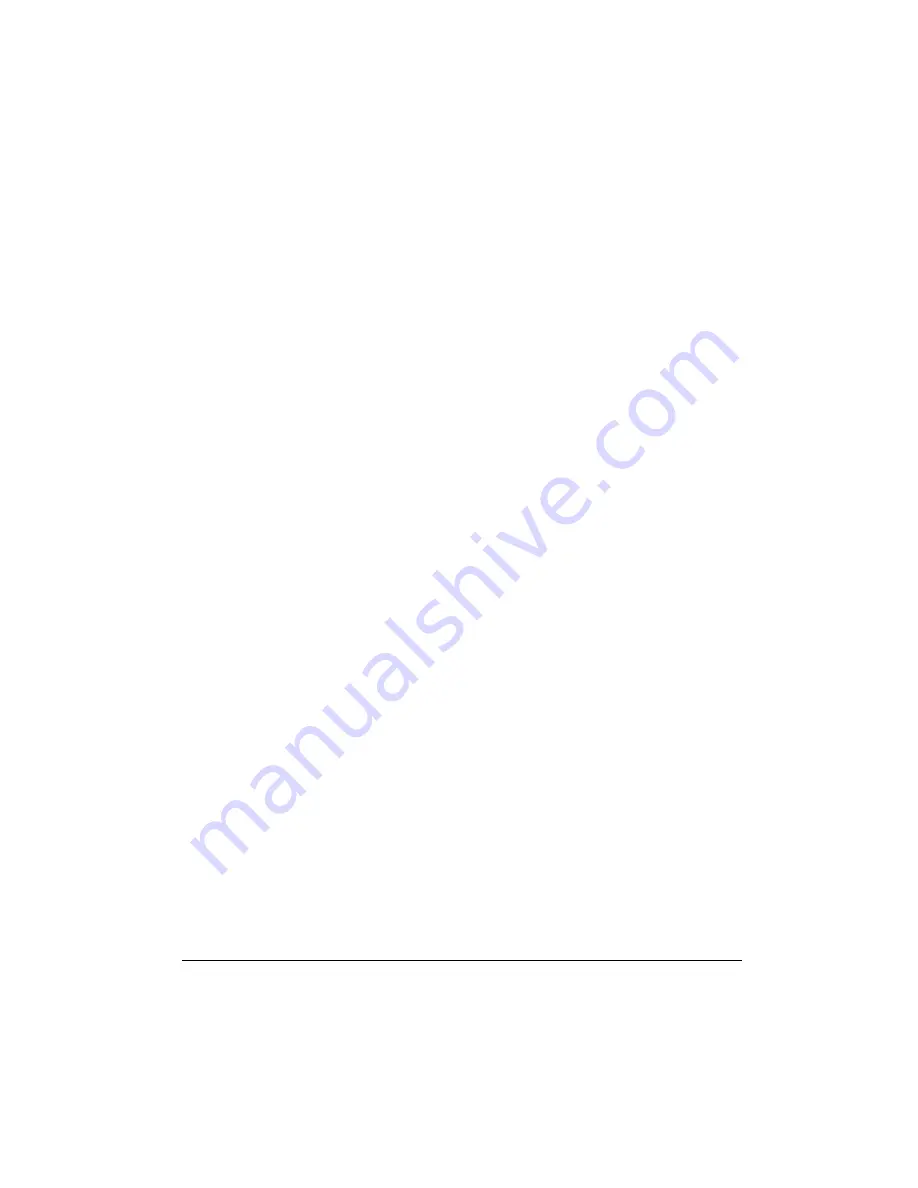
13-9-663 Page 17
Extreme Cold Weather Operation
(Down To -10
°
F, -23
°
C
)
In addition to the above, the following should be provided:
1.
It will be necessary to provide shutters or to block off part of the cooler in some manner since the
cooler is greatly oversized for operation in these low temperatures. Since shutters are not provided
as a factory option, blocking off a portion of the cooler with plywood should be satisfactory.
2.
Auto operation should not be used in extreme environments.
3.
Some means of providing heat during shutdown. Start-up should be provided. There are various
methods to accomplish this, but since openings are not provided for sump heaters, the use of radiant
heaters is recommended. The heaters should be sized to provide at least a +10
°
F (-12 C)
environment for coolers, motor and sump. Figure 2-3, page 16, shows how these might be located
in a typical installation and sizes required.
Remember unsheltered (outside) installations should be avoided where possible. Installation next to a
heated building where enough heat can be used to keep the compressor room above freezing will save
many complications in the operation and installation of the unit.
Refer to Engineering Data Sheet 13-9-411, available from an authorized Gardner Denver distributor, for
the advantages of using the heat recovered from rotary compressors. This heat recovery could easily
pay for an adequate shelter for the unit.
AUXILIARY AIR RECEIVER
- An auxiliary air receiver is not required if the piping system is large and
provides sufficient storage capacity to prevent rapid cycling. When used, an air receiver should be of
adequate size, provided with a relief valve of proper setting, a pressure gauge and a means of draining
condensate.
MOISTURE SEPARATOR/TRAP
- Since the unit is equipped with a built-in aftercooler, a combination
moisture separator and trap is furnished with the unit.
CONTROL PIPING
- Control piping is not necessary since the Rotary Screw compressor unit is factory
wired and piped for the control system specified.
INLET LINE
- Where an inlet line is used between the air filter and the compressor, it must be thoroughly
cleaned on the inside to prevent dirt or scale from entering the compressor.
If welded construction is
used, the line must be shot blasted and cleaned to remove welding scale.
In either case, the inlet
line must be coated internally by galvanizing or painting with a moisture and oil-proof sealing lacquer. Up
to ten (10) feet (3 meters) in length, the inlet line should be the full size of the inlet opening on the
compressor. If an extra-long line is necessary, the pipe size should be increased according to Inlet Line
Length Chart, Figure 2-4.
Accessibility for inlet air filter servicing must be considered when relocating the filters from the unit to a
remote location.
INLET LINE LENGTHS
Length of Inlet Line
Diameter of Pipe Size
0 to 10 Feet (0 to 3 Meters)........................ Same as Compressor Inlet Opening
10 to 17 Feet (3 to 5 Meters)...................... One Size Larger Than Inlet Opening
17 to 38 Feet (5 to 11.5 Meters)................. Two Sizes Larger Than Inlet Opening
Figure 2-4 – INLET LINE LENGTHS