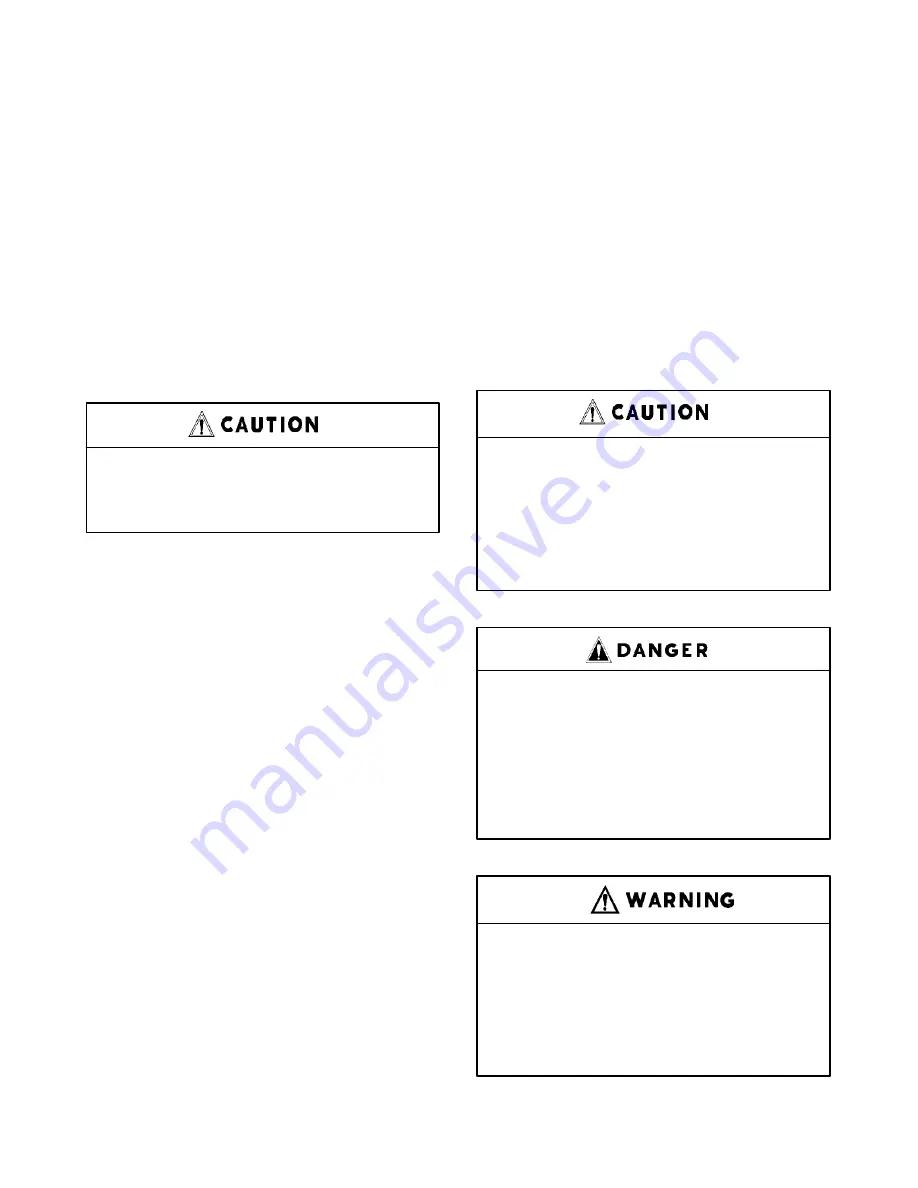
13--8--625
Page 30
6.
Shut down unit, allowing the oil to settle, and be
certain all pressure is relieved.
7.
Add oil, if necessary, to bring level to the top of the
white section of the oil level gauge, FIGURE 5--4,
page 31.
DO NOT OVERFILL as oil carryover will result. The
quantity of oil required to raise the oil level from the bot-
tom to the top of the site glass is shown in FIGURE 5--2,
page 28. Repeated addition of oil between oil changes
may indicate excessive oil carryover and should be in-
vestigated.
Use only CLEAN containers and funnels so no dirt en-
ters the reservoir. Provide for clean storage of oils.
Changing the oil will be of little benefit if done in a care-
less manner.
Excessive oil carry--over can damage
equipment.
Never fill oil reservoir
above the top of the site glass.
LUBRICANT UPGRADE PROCEDURE -- Upgrading
to a longer life lubricant is essentially a very worthwhile
practice. Following are the primary steps to be com-
pleted when upgrading or changing the type of lubri-
cant.
1.
Be sure the unit is completely off and that no air
pressure is in the air/oil reservoir.
2.
Disconnect, tag and lock out the power supply to
the starter.
3.
Thoroughly drain system:
--
Drain oil from air end and cooler while hot.
--
Break low point connections and drain oil from
pipe runs.
--
Dump Oil from filter and reinstall used filter.
4.
Fill system with a 50 percent charge of the new lu-
bricant:
--
Start the machine and stay there to observe.
--
Allow the machine to run about five minutes at
temperature, or until temperature stabilizes,
then shut down.
5.
Thoroughly drain machine.
6.
Change to a new filter and separator.
7.
Fill system with a full charge of the new lubricant.
8.
Machine should then be run normally; however,
total run time after the initial changeout should be
50 percent of normal anticipated service life of the
new lubricant.
--
Drain all lubricant from system, change filter
and separator, and replace with full charge of
the new lubricant.
9.
Subsequent lubricant changeouts should be at
normal intervals. (See “Oil Change Interval” and
chart, page 29.)
Improper
equipment
maintenance
with use of synthetic lubricants will
damage equipment. Oil filter and oil
separator change intervals remain
the same as for AEON 2000 -- -- See
Maintenance Schedule, page 39.
Air/oil under pressure will cause
severe personal injury or death. Shut
down compressor, relieve system of
all pressure, disconnect, tag and lock
out power supply to the starter before
removing
valves,
caps,
plugs,
fittings, bolts, and filters.
High
temperature
operation
can
cause damage to equipment or per-
sonal injury. Do not repeatedly restart
the unit after high temperature stops
operation. Find and correct the mal-
function before resuming operation.
Summary of Contents for EFD-25 HP
Page 13: ...13 8 616 Page 4 DECALS 206EAQ077 212EAQ077 218EAQ077 211EAQ077 207EAQ077...
Page 14: ...13 8 616 Page 5 DECALS 216EAQ077 217EAQ077 222EAQ077 221EAQ077 208EAQ077...
Page 30: ...13 8 625 Page 21 FIGURE 4 4 COMPRESSOR RUNNING FULLY LOADED...
Page 32: ...13 8 625 Page 23 FIGURE 4 5 WIRING DIAGRAM 3 305865 Ref Drawing...
Page 33: ...13 8 625 Page 24 FIGURE 4 6 WIRING DIAGRAM 3 305979 A Ref Drawing...
Page 34: ...13 8 625 Page 25 FIGURE 4 7 WIRING DIAGRAM 3 305979 A Ref Drawing...
Page 54: ...13 8 625 Page 45 AIREND GROUP...
Page 60: ...13 8 625 Page 51 AIREND AND INLET FILTER ASSEMBLY...
Page 72: ...13 8 625 Page 63 COOLING GROUP...
Page 74: ...13 8 625 Page 65 CONTROL SYSTEM ASSEMBLY AND MOUNTING...
Page 78: ...13 8 625 Page 69 CONTROL BOX 3 305979 A Ref Drawing...