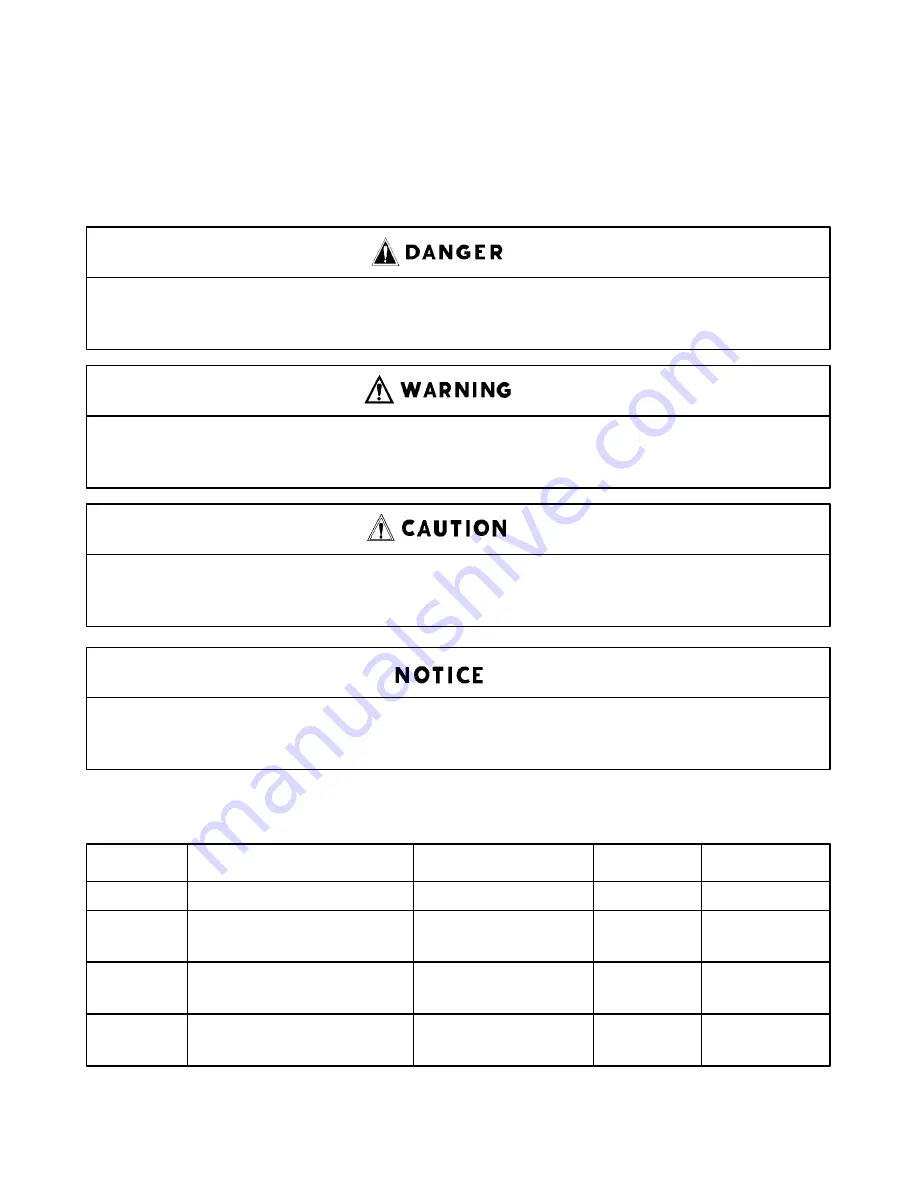
13–8–609 Page ii
FOREWORD
Gardner Denver
Electra–Screw
compressors are the result of advanced engineering and skilled manufacturing.
To be assured of receiving maximum service from this machine the owner must exercise care in its operation and
maintenance. This book is written to give the operator and maintenance department essential information for day–
to–day operation, maintenance and adjustment. Careful adherence to these instructions will result in economical
operation and minimum downtime.
Danger is used to indicate the presence of a hazard which will cause severe personal
injury, death, or substantial property damage if the warning is ignored.
Warning is used to indicate the presence of a hazard which can cause severe person-
al injury, death, or substantial property damage if the warning is ignored.
Caution is used to indicate the presence of a hazard which will or can cause minor
personal injury or property damage if the warning is ignored.
Notice is used to notify people of installation, operation or maintenance information
which is important but not hazard–related.
This book covers the following models:
HP (KW)
PSIG (Bar)
Air Cooled
Domestic
International
15
100, 125
EBE_DH
13–8–509
20 (15)
100, 125, 150
EBE_EH (EBE_EJ)
13–8–509
13–8–509X
(6.9), (8.6), (10.3)
25 (19)
100, 125, 150, 175
EBE_FH (EBE_FJ)
13–8–509
13–8–509X
(6.9), (8.6), (10.3), (12.1)
30 (22)
100, 125, 150, 175
EBE_FH (EBE_GJ)
13–8–509
13–8–509X
(6.9), (8.6), (10.3), (12.1)
Summary of Contents for ELECTRA-SCREW EBE DH-15 HP
Page 14: ...13 8 609 Page 6 DECALS 206EAQ077 212EAQ077 218EAQ077 211EAQ077 207EAQ077...
Page 15: ...13 8 609 Page 7 DECALS 216EAQ077 217EAQ077 222EAQ077 221EAQ077 208EAQ077...
Page 32: ...13 8 609 Page 24 FIGURE 4 10 WIRING DIAGRAM DUAL CONTROL 218EBE546 Ref Drawing...
Page 33: ...13 8 609 Page 25 FIGURE 4 11 WIRING DIAGRAM WYE DELTA 220EBE546 Ref Drawing...
Page 51: ......