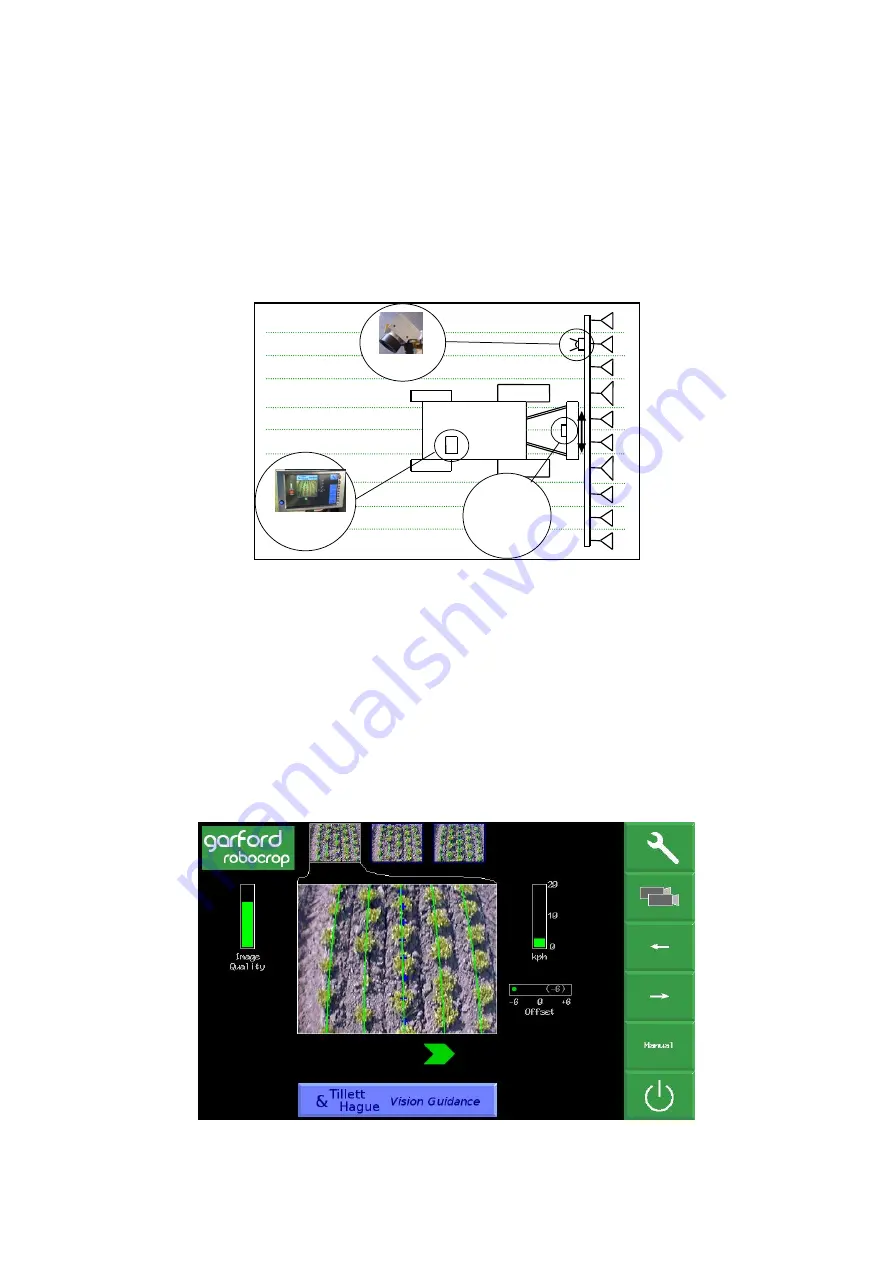
3
1. Preface
Congratulations on purchasing a Robocrop precision guided implement.
Robocrop precision guided implements are guided by a computer controlled steering system.
There are 3 main components to the system.
1. A digital camera or cameras mounted on the implement looking ahead at a wide area of
crop normally taking in several rows.
2. A cab mounted console containing a computer to analyses camera images and find exact
row centres.
3. A hydraulic side shift (or steered discs) controlled by the computer to keep the camera
centrally over crop rows and the implement precisely on track.
Schematic of Robocrop on a rear mounted inter-row cultivator with side shift
Robocrop uses a colour camera to pick out green crop and weed from backgrounds containing
soil, stones and trash. (Consult your Garford dealer for systems to work in red crops.) Robocrop
locates crop rows within a scene by matching a template corresponding to the known planting
pattern with crop rows as they appear in the camera image. That image is displayed live on the
console with the template overlaid as green lines.
Matching a template to a broad area of crop rather than locating individual rows improves reliability
especially when parts of those rows are not present or obscured by weeds. Template shape is
determined by a configuration file pre-programmed to suit a particular crop planting geometry and
implement configuration. Different configuration files can be created for different crops and
implements.
A good match between the template and crop rows is very important for accurate row following.
Console working screen showing a typical live video image with the template superimposed as
green lines over crop rows.
Camera
Micro
controller
and valves
for hydraulic
side shift
Console