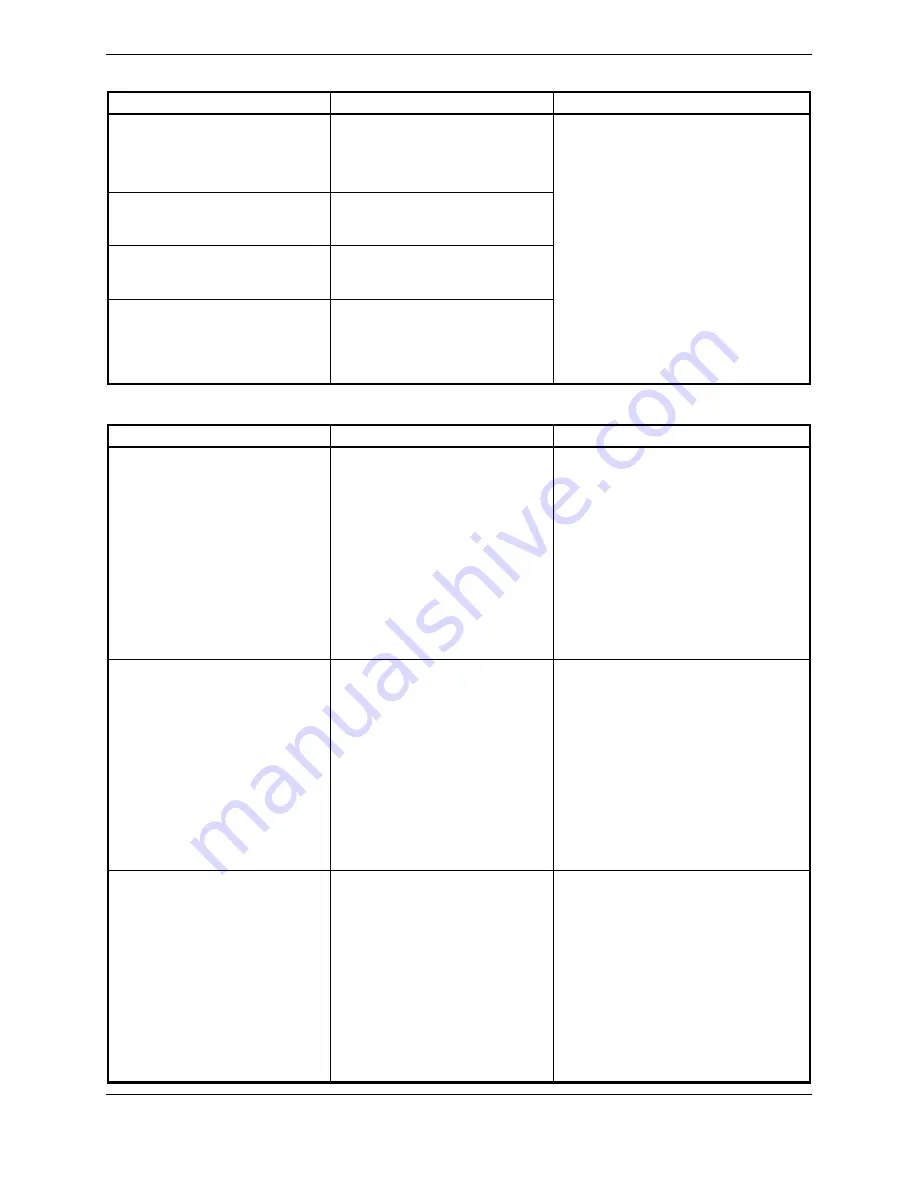
G1000 / GFC 700 System Maintenance Manual - 300/B300 Series King Air
Page 5-49
190-00716-01
Revision 1
Failure Message
Cause
Solution
DB MISMATCH – Airport Terrain
database version mismatch. Xtalk
is off.
The PFDs and/or MFD have
different Airport Terrain database
versions installed.
•
Confirm supplemental data card is
inserted fully.
•
Reload the database or replace the
supplemental datacard.
DB MISMATCH – Terrain
database version mismatch.
The PFDs and/or MFD have
different terrain database versions
installed.
DB MISMATCH – Obstacle
database version mismatch.
The PFDs and/or MFD have
different obstacle database
versions installed.
DB MISMATCH – Terrain
database type mismatch.
The PFDs and/or MFD have
different terrain database types
installed (i.e., different regions:
Americas, International, Atlantic,
etc).
5.9.3
Cooling Alerts
Failure Message
Cause
Solution
MFD1 COOLING – has poor
cooling. Reducing power usage.
MFD1 has exceeded its operating
temperature range.
•
Check cooling fan and wiring
for proper operation (if
applicable).
9
Replace cooling fan if
unable to determine if
operating correctly.
9
If problem persists, replace
the MFD.
•
If problem continues contact
Garmin Aviation Product Support
for assistance.
PFD 1 COOLING – has poor
cooling. Reducing power usage.
PFD 1 has exceeded its operating
temperature range.
•
Check cooling fan and wiring
for proper operation (if
applicable).
9
Replace cooling fan if
unable to determine if
operating correctly.
9
If problem persists, replace
the PFD1.
•
If problem continues contact
Garmin Aviation Product Support
for assistance.
PFD 2 COOLING – has poor
cooling. Reducing power usage.
PFD 2 has exceeded its operating
temperature range.
•
Check cooling fan and wiring
for proper operation (if
applicable).
9
Replace cooling fan if
unable to determine if
operating correctly.
9
If problem persists, replace
the PFD2.
•
If problem continues contact
Garmin Aviation Product Support
for assistance.
Summary of Contents for Cessna Caravan G1000
Page 2: ...This page intentionally left blank...
Page 89: ......