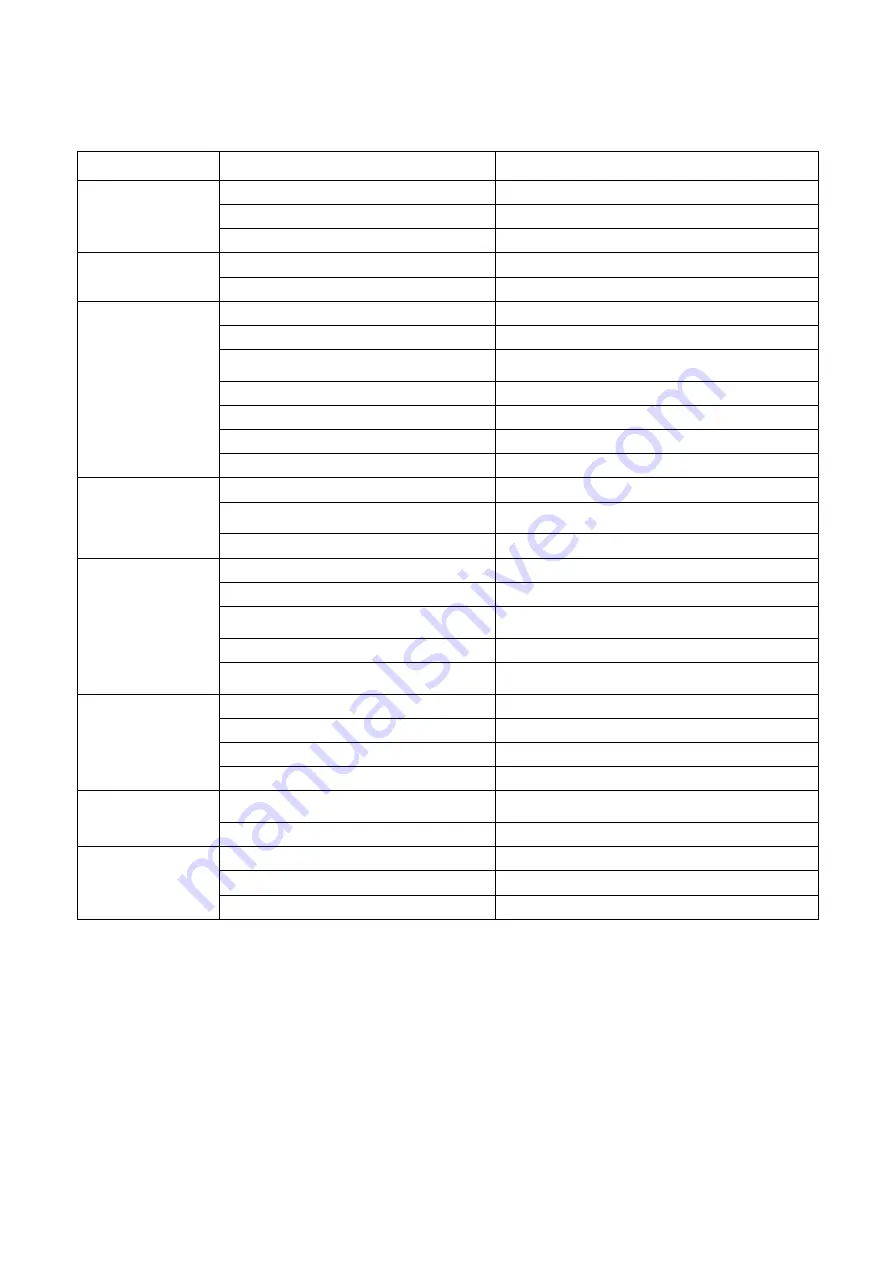
5
Troubleshooting
PROBLEM
CAUSE
CORRECTION
Rolled groove too
narrow or too wide.
Incorrect size of grooving and driving rolls.
Install correct size of grooving and driving rolls.
Mismatched grooving and driving rolls.
Match grooving and driving rolls.
Grooving roll and/or driving roll worn.
Replace worn roll.
Rolled groove not
perpendicular to
pipe axis.
Pipe length not straight.
Use straight pipe.
Pipe end not square with pipe axis.
Cut pipe end square.
Pipe does not track
while grooving.
Pipe not level.
Adjust stand to level pipe.
Groover not level.
Level groover.
Pipe axis not offset 1/2 degree from drive
roll axis.
Offset pipe 1/2 degree
1/2 degree offset not sufficient.
Offset pipe slightly more.
Not applying pressure to pipe.
Apply pressure to pipe
Excessive weld seam.
Grind flush
from end of pipe.
Pipe end not square.
Cut pipe end square.
Pipe flared at
groove end.
Pipe not level.
Adjust stand to level pipe.
Operator is advancing groove roll too fast.
Slow down pumping action.
(Refer to proper
operating instructions.)
Pipe is too hard.
Replace pipe.
Pipe drifts back
and forth on
driving roll axis
while grooving.
Pipe length not straight.
Use straight pipe.
Pipe end not square with pipe axis.
Cut pipe end square.
Hard spots in pipe material or weld seams
harder than pipe.
Use high quality pipe of uniform hardness.
Grooving roll feed rate too slow.
Feed grooving roll into pipe faster.
Pipe support stand rollers not in correct
location for pipe size.
Position pipe stand rollers for pipe size being used.
Groover does not
roll groove in pipe.
Pipe wall maximum thickness exceeded.
Check pipe capacity chart.
Wrong rolls.
Install correct rolls.
Pipe material too hard.
Replace pipe.
Adjustment nut not set.
Set depth.
Pipe slips on
driving roll.
Driving roll knurling plugged with metal or
worn flat.
Clean or replace driving roll.
Grooving roll feed rate too slow.
Feed grooving roll into pipe faster.
Pump not
delivering oil,
cylinder does not
advance.
Pump release valve open.
Close release valve.
Low oil in reservoir.
Check oil level per instructions.
Dirt in pump body.
Have serviced by qualified technician.
Summary of Contents for RG6C
Page 7: ......