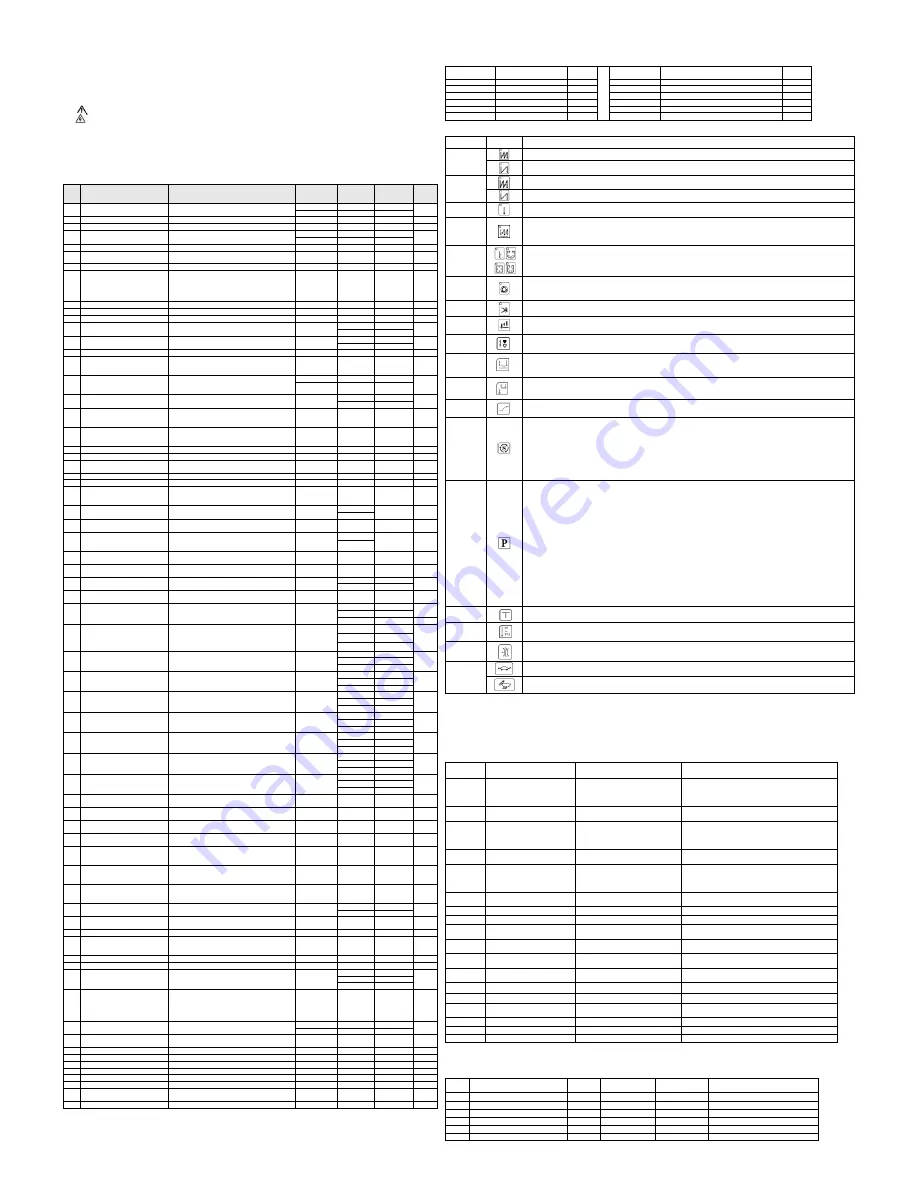
1. Safety instruction
Please read the operation manual and related sewing machinery datasheet carefully before correct use.
1.1 (1) Power voltage and frequence: please refer to motor and control box nameplate.
(2) Interference from electromagnetic wave:please keep far away strong magnetic or high radiation environment in order
to avoid obstructions and make to misoperation.
(3) Grounding: to avoid the noise obstructions or leakage of electricity accident(inculding sewing machine,motor,control
box and positioner).
1.2 Please make sure power off at least 1min and then can open control box cover, because there are dangerous high voltage.
1.3 Please turn off the power while repairing or wearing needle in order to protect operater’s safty.
1.4
Used where potential dangers exist.
Used where high voltage and electric danger exist.
1.5 Product warranty period of one year on condition that this machine is operated correctly and no man-made damage.
No
Project
Content
Setting
range
The
default
value
model
Level
1
Sewing speed
Set sewing speed
200~5000rpm
3700
ABCDGIL
I
200~3500rpm
3000
EFHJKN
2
Soft-start function
1~9: Soft start stitches
1~9
1
All
I
3
Ornamental bartacks
0: Invalid 1: Effective
0/1
0
All
I
4
Fixed-length seam sewing speed
Set fixed-length seam sewing speed
200~4000rpm
3000
ABCDGIJL
I
200~3500rpm
2500
EFHKN
5
Simple sewing mode Settings
0: invalid 1: effectively
0/1
0
All
I
9
Back stitch speed limitation
can keep needle from breaking while
backstitching
500~1500rpm
800
All
I
19
Solid after before sewing stop
0: unavailable 1: available
0/1
0
All
I
20
Setting of reverse sewing switch
function
Reverse sewing switch mode
0: Only reverse sewing
1: Reverse sewing and fill needle
2: Only reverse sewing, standby without operating
0/1/2
0
All
I
21
soft start speed 1
speed of the 1
st
needle of soft start
100~3000rpm
400
All
I
22
soft start speed 2
speed of the 2
nd
needle of soft start
100~3000rpm
1000
All
I
23
soft start speed 3
speed of the 3
rd
~9
th
needle of soft start
100~3000rpm
1500
All
I
24
Presser foot soft lowering
function
0: unavailable 1: available
0/1
0
ABCDEFGHIJK
I
1
LN
25
Presser foot lift function
0: unavailable 1: available
0/1
0
ABCDEFGHIJK
I
1
LN
27
Power on and positioning
0: unavailable 1: available
0/1
1
All
I
28
signal mode for turn/lift switch
Setting of signal mode of turn/lift switch of
machine head 0: always open
1: always close 2:forbid a protection
0/1/2
0
All
I
29
Presser foot soft lowering time
To set presser foot soft lowering time
The longer time the lower speed of the presser
foot
50~500ms
300
ABCDEFGHIJK
II
10~500ms
50
LN
32
Decorative bar-tacking dwell
time
To set decorative bar-tacking dwell time
5~500ms
50
ABCDGIJL
I
100
EFHKN
34
To select standard bar-tacking
pedal speed mode
Standard bar-tacking pedal speed
Mode selection
0:Auto bar-tacking speed ; 1:Pedal speed
0/1
0
All
II
35
By-piece rate setting
0:No by-piece function
1~20:Plus 1 to by-piece value for each set thread
trimming
0~20
1
All
I
37
Thread wiping operation time
Thread wiping operation time
0~800ms
40
All
II
41
Low speed
The lowest speed of pedal
100~400rpm
200
All
I
42
Pedal curve selection
Pedal speed adjustment 0:normal
1:Slow acceleration 2: Quick acceleration
0/1/2
0
All
I
43
Dial the line that can set
0: unavailable 1: available
0/1
1
All
I
44
thread-cutting speed
thread-cutting speed
100~400rpm
280
All
I
45
Reverse sewing speed limit switch
Reverse sewing speed limit switch processing can
prevent reverse sewing needle breakage
0: infinite speed 1: have the speed limit
0/1
0
All
I
46
pressor foot lifting delays
sewing
delay with pressor foot lowered
0~800ms
200
ABCDEFGHIJK
LN
II
100
47
output time of total pressure of
pressor foot lifting
output time of total pressure of pressor foot
lifting
0~800ms
150
All
II
48
output duty cycle of pressor foot
lifting
hold time of pressor foot lifting
output duty cycle of pressor foot lifting
forced shut-down after hold time of pressor foot
lifting
0~100
30
All
II
40
49
output duty cycle of pressor foot
lifting
output duty cycle of pressor foot lifting
1~60(s)
12
All
II
50
output time of total pressure of
reverse-sewing
output time of total pressure of reverse-sewing
0~800ms
150
All
II
51
output
duty
cycle
of
reverse-sewing
output duty cycle of reverse-sewing
0~100
40
ABEFGHJKLN
II
35
CDI
52
hold time of reverse-sewing
forced
shut-down
after
hold
time
of
reverse-sewing
1~60(s)
12
All
II
53
starting
reinforcing-sewing
speed
starting reinforcing-sewing speed
100~3000rpm
1800
ABCDGIL
I
1200
EFHN
500
JK
54
starting
reinforcing-sewing
compensation 1
parameter of starting reinforcing-sewing stitch
compensation
0~100
30
ABGJL
I
35
CDI
58
EFHNK
55
starting
reinforcing-sewing
compensation 2
parameter of starting reinforcing-sewing stitch
compensation
0~100
10
ABGJL
I
24
CDI
18
EFHKN
56
ending reinforcing-sewing speed
ending reinforcing-sewing speed
100~3000rpm
1800
ABCDGIL
I
1200
EFHN
500
JK
57
ending
reinforcing-sewing
compensation 1
parameter of ending reinforcing-sewing stitch
compensation
0~100
30
ABGJL
I
35
CDI
58
EFHKN
58
ending
reinforcing-sewing
compensation 2
parameter of ending reinforcing-sewing stitch
compensation
0~100
10
ABGJL
I
24
CDI
18
EFHKN
59
ending reinforcing-sewing speed
ending reinforcing-sewing speed
100~3000rpm
1800
ABCDGIL
I
1200
EFHN
500
JK
60
continuous
reinforcing-sewing
compensation1
parameter of continuous reinforcing-sewing
stitch compensation
0~100
30
ABGJL
I
35
CDI
58
EFHKN
61
continuous
reinforcing-sewing
compensation2
parameter of continuous reinforcing-sewing
stitch compensation
0~100
10
ABGJL
I
24
CDI
18
EFHKN
62
Pedal travel upon start
Pedal position upon start
Travel relative to medium pedal
10~50
(0.1°)
25
All
II
63
Pedal travel upon acceleration
Pedal position upon start acceleration
Travel relative to medium pedal
10~100
(0.1°)
50
All
II
64
Pedal travel at highest rotation
speed
Pedal position at highest rotating speed Travel
relative to medium pedal
10~150
(0.1°)
110
All
II
65
Pedal travel upon presser foot
lift
Pedal position upon pedal lift
Travel relative to medium pedal
-100~-10
(0.1°)
-30
All
II
66
Pedal travel upon presser foot
lowering
Pedal travel from presser foot lowering position
to neutral position
Travel relative to medium pedal
5~50
(0.1°)
10
All
II
67
Pedal travel 1 upon thread
trimming
Pedal position upon start trimming without
presser foot function
Travel relative to medium pedal
-100~-10
(0.1°)
-30
All
II
68
Pedal travel 2 upon tread
trimming
Pedal position upon start thread trimming with
presser foot function
Travel relative to medium pedal
-100~-10
(0.1°)
-60
All
II
69
Down needle positioning position
To adjust down needle position
120~240
175
ABEFGHJKLN
I
177
CDI
70
Reverse needle lift function
Reversal of needle lift function after thread
trimming 0: unavailable 1: available
0/1
0
All
I
71
Reversal of needle lift angle
Reversal of needle lift angle
0~45°
20
All
I
72
Thread clamp strength adjustment
Adjust the thread clamp strength size
0: Clip line function is invalid
1~9: Three Intensity Adjustment
0~9
7
All
I
73
Thread pressing actuation angle
Thread pressing actuation angle
10~150°
100
All
I
74
Thread pressing release angle
Thread pressing release angle
160~300°
270
All
I
75
Needle position adjustment
Needle position adjustment
0~240°
105
ABEFGHJK
I
112
LN
165
CDI
79
return to factory-set parameter
5: restore the current level factory parameters
8: restore the current level and sewing factory
parameter set
According to S button, select yes, then press the
S key execution
0~15
0
All
I
80
highest speed of sewing
highest speed of sewing
300~5000spm
4000
ABCDGIL
II
300~3500spm
3000
EFHJKN
83
Aggravating function/
Machine needle emphasis function
Needle wear through cloth when used
0: invalid; 1 ~ 15 strength regulation
0~15
0
ABCDEFGHIJ
II
84
Aggravating function
0: invalid; 1 ~ 15 strength regulation
0~15
0
LN
II
85
Suction angle of shear line
To set suction angle of shear line
150~200
175
All
II
86
Power angle of shear line
To set power angle of shear line
200~300
260
All
II
87
Release angle of shear line
To set release angle of shear line
300~360
340
All
II
88
loosen pressing actuation angle
loosen pressing actuation angle
150~250
180
I
I
89
loosen pressing release angle
loosen pressing release angle
200~360
350
I
I
92
Pedal presser foot lift confirm
time
Pedal presser foot lift confirm time
10~300ms
80
All
II
93
The neutral position of the pedal
Trimming the neutral position of the pedal
-15~15(0.1)
0
All
II
95
dial line / clip line Type
selection
Type selection;0:dial line 1:clip line
0/1
0
ABCDEFIJK
II
1
GHLN
2. System parameter table
A:587/586(Full automatic integrated Digital version) B:587C/CD(Full automatic integrated Liquid crystal version)
C:588(Full automatic Less oil integrated Digital version) D:588C/CD(Full automatic Less oil integrated Liquid crystal version)
E:587H/586H(Full automatic Thick material integrated Digital version) F:587CH(Full automatic Thick material integrated Liquid
crystal version) G:587C/CD(Full automatic integrated Liquid crystal version Public models) H:587CH/CHD(Full automatic Thick
material integrated Liquid crystal version) I:589( Full automatic Less oil 9813 Liquid crystal version)
L:587Y(Fully automatic machine pressure foot built-in) N:587YH(Fully automatic
Thick material machine pressure foot built-in)
5. Error codes
Error
Code
Contents
Possible reasons
Checking and treatment
E011
E012
E013
E014
Motor signal error
Motor position sensor signal failure
If electric engine plug is well contacted;
if electric engine signal detecting device has been
broken;
if sewing machine handwheel correctly installed.
E015
Model type error
Unable identify operating box model
type
Check operating box
E021
E022
E023
Motor overload
motor stall
motor overload
If electric engine plug is well contacted;
if machine head or thread-cutting mechanism has been
blocked completely;f materials are too thick;
Electrical signal detection signal whether the normal.
E101
Hardware drivers fault
Current detection abnormal
Driving hardware error
Current
detection
loop
system
is
working
properly;Whether the damage to the device driver.
E111
E112
Voltage too high
High input voltage
Brake circuit fault
Voltage detection error
System into line voltage is too high;
Braking resistance are working properly;
System voltage detection circuit are working properly.
E121
E122
Voltage too low
Actual low voltage
Voltage detection is wrong
If the voltage on the inlet wire is too low Whether the
system voltage detection circuit the normal work.
E131
Current circuit fault
Current detection abnormal
Current detection loop system is working properly.
E133
Oz circuit fault
Oz circuit fault
Oz circuit system is working properly.
E151
Magnet circuit error
Over current magnet circuit
If machine head magnet suffers short circuit
Electromagnet circuit is working properly.
E201
over current
Current detection error
Current detection loop system is working properly
Electrical signal is normal.
E211
E212
Abnormal motor operation
Current or voltage detection error
If electric engine plug is well contacted;
If electric engine signal is matched.
E301
Communication error
Sci circuit error
if operation box plug is well contacted;
if operation box components are damaged.
E302
Operation inner failure
Sci circuit error
To check whether the operating box is damaged..
E402
Pedal ID fault
Pedal verification fault
Pedal connection is loosen.
E403
Pedal zero position fault
The pedal zero position over range
The pedal is damaged or it is not under stop state when
correction.
E501
Safety switch fault
Safety switch effective
Put down the head or check turned up switch.
P.oFF
Power off Display
Power off
Wait for power supply to resume.
EvaL
Trial expired
Trial expired
Contact the dealer processing
Note: 1. Sewing abnormal action (speed electromagnet work abnormal) : in the control interface view model is correct;
2. Turn up E501 fault when: sure it is normal to switch detection, temporary use can change the P-28 parameters;
3. If the above according to check the project cannot rule out fault, please seek technical support.
Function
Button
Described
Starting
reinforcing
-sewing
Execute starting reinforcing-sewing 2 times, to and fro.
Execute starting reinforcing-sewing 1 times, to and fro.
ending
reinforcing
-sewing
Execute ending reinforcing-sewing 2 times, to and fro.
Execute ending reinforcing-sewing 1 times, to and fro.
free-style
sewing
Press treadle ahead for normal sewing, stop in the middle, behind for thread-cutting and thread wiping.
continuous
reinforcing
-sewing
1、Press treadle ahead for automatic sewing, to and fro, which is set at D and can reach 15times.(F)
2、Continuous reinforcing-sewing is in trigger mode by default, treadle doesn’t need to be kept being pressed, and
corresponding trigger light of preset sewing is solid lit.
3、Previous ending reinforcing-sewing setting is invalid if this function is valid.
preset
sewing
1.Press treadle ahead to execute sewing times set at E or E, F, G, H.
2.Sewing will stop immediately if treadle is lifted; press treadle again, it will go on with the rest.
3.Ending reinforcing-sewing (if selected), thread-cutting and thread wiping will be automatically executed after sewing
is completed.
parameter
setting
1.For preset sewing. Trigger treadle and the system will automatically conduct sewing at E, F, G, H sections; the treadle
doesn’t need to be kept being pressed.2.Solid light for continuous reinforcing-sewing mode means that it is trigger mode
by default.
thread-cutt
ing
selection
Set or cancel thread-cutting function.
needle-lift
ing/stitch
compensatio
n
Free sewing mode, can be based on the according to the length of time is different, complementary half needle,
a needle or continuous feeding half needle.
Needle
position
Set the needle position shortcut keys,Key is effective for needle,The cancel key function is set to stop pin。
The middle
presser
foot
Presser foot to set shortcut keys: set or cancel the presser foot function.
Shear line
pressure
foot
The shear line and presser foot set shortcut keys: set or cancel trimmer and presser foot function.
Soft start
Soft start to set shortcut keys: set or cancel the pedal soft start function.
Pinnumberse
t/check
choice
1.Implementation of this key, circulating switch display 3 pin number to set the display value
upper end:A、B、C、DPeriod of pin number,Light corresponding level;
Middleend:E、FPeriod of pin number,Light corresponding level;
lower extreme:G、HPeriod of pin number,Light corresponding level;
2.Corresponding to A D period of pin number, can set range 0 ~ 15 needle, B paragraph C pin number, can set range 1 ~ 15
needle, among them, the liquid crystal display A B C D E F on each for 10 11 12 13 14 15 stitches.
3. To take the thread clamp function model, according to the buttons can show long thread clamp strength adjustment (3
bright lights and three, liquid crystal display [7]), again according to the key exit.
parameter
setting
1.Entering different parameter level
On the sewing setting interface, the user can press the button P to enter the Parameter Interface, then the Level I parameters
in the parameter list will display.
On the sewing setting interface, the user can keep pressing the button for a few seconds to enter the Password Entering
Interface. After entering the right maintenance password, then the user can press the button P to enter the Parameter
Interface, now the Level I and Level II parameters in the parameter list will display.
2.Password setting
On the sewing setting interface, the user can keep pressing the button P for a few seconds to enter the Password Entering
Interface, and press the button combination of “burst
soft start button” to enter the Password Resetting
Interface. The three indicators (respectively are Indicator S1, S2 and S3 from left to right/before three lamp, among which
one is on) corresponding to the button S indicates the current status. S1 lights up, old password input, ending the key
combination trigger key + tangent key, if the correct password into the password reset interface (mistakes have stayed
the S1 state), and at the same time S2 light, prompting the input new password and click confirm S3 S key input again when
the light is the new password, according to S key after two input if consistent, then set success, return to parameter
interfaceIf the new passwords entered are not the same, the Indicator S1 will be on and the LC screen will be reset, and
the user shall enter the old password again. If the user presses the button P, the user will be brought back to the interface
parameters and no modification will be saved. You can choose from the numbers of 0 to 9 or the letters of A to F for every
single character of the password. Please do keep the new password in mind.
Teaching
function
Set or cancel the teaching function. (for liquid crystal panel)
Sewing set
program
The number of needles sewing set,Set up a total of 15 segment needle number P1~PF. (for liquid crystal panel)
Clip the
line
intensity
set
Clip the line strength fast set
speed key
Speed down. Keeping pressing to lower speed, the display will automatically switch to speed set. Simple seam, free seam
effective.(Application of liquid crystal panel)
Speed up. Keeping pressing to increase speed, the display will automatically switch to speed set.Simple seam, free seam
effective. (Application of liquid crystal panel)
Teaching function:
In the long slot (a, four, program seam) mode, long press "T" one second, you can enter the teaching interface, this interface has buttons: T key,
two groups of add-substract key, fill needle key. Role is as follows:
Add-substract key 12: change teaching segments, segment numerical only to accumulate (into the next section teaching automatically save the last needle
numerical reduction), '-' key is invalid. Note: when the pedal operation, the key is invalid;
Add-substract key 34: modify teaching pin number, to stop running when the adjust pin number. Fill needle keys: press can manually fill needle, needle
change.
T: exit show interface, complete the current segment number teaching (section numerical covering the original mode).
After the pedal shear line, will directly from the show and save the needle numerical, before returning to the fixed length of stitch pattern.
6.Accessories
NO
Product name
Amount
Product
specification
Confirm
Remarks
1
Electric control box
1
2
Ball section connecting rod
1
3
pedal
1
PL-302
with bracket
4
screw
3
M5×25
screw
5
The instructions
1
6
power cord
1
3.System Info
Operation panel default mode, press the button at the same time in P made sewing needle trigger select key, enter the system
monitoring state through the +-key choose need to look at the project, according to the S button to enter/exit the selected
projects such as the need to exit monitoring interface, according to P keys can be.
4.Operation box use
Full automatic integrated sewing series manual V1.9
-1-
-2-
show frame
numbers
Item Name
unit
show frame
numbers
Item Name
unit
JJ
Plan number
piece
U6
Motor initial Angle
limit
U1
speed of motor control
rpm
U7
Master control program version/ Head type
/
U2
Motor Current
0.01A
U8
Head type/ Master control program version
/
U3
Motor Voltage
V
U9
Dsp no
/
U4
Pedal voltage
0.01V
vEr
Operation box version of the program
/
U5
Mechanical Angle with
limit
TYPE
Software no
/
Summary of Contents for GF-1107-147 MH
Page 21: ...ANITA MP02300EN_170818 21 23 Change of counter knife and moving knife w w w g a r u d a n c z ...
Page 28: ...ANITA MP02300EN_170818 w w w g a r u d a n c z ...
Page 38: ...ANITA MP02300EN_170818 8 2 MAIN SHAFT THREAD TEKE UP COVER COMPONENTS w w w g a r u d a n c z ...
Page 44: ...ANITA MP02300EN_170818 14 4 HANG LIFTER TENSION RELEASE COMPONENTS w w w g a r u d a n c z ...
Page 46: ...ANITA MP02300EN_170818 16 5 THE NEEDLE BAR SWING COMPONENTS w w w g a r u d a n c z ...
Page 48: ...ANITA MP02300EN_170818 18 6 FEED ADJUST MECHANISM COMPONENTS w w w g a r u d a n c z ...
Page 52: ...ANITA MP02300EN_170818 22 8 BOBBIN WINDER COMPONENTS w w w g a r u d a n c z ...
Page 54: ...ANITA MP02300EN_170818 24 9 AUTOMATIC REVERSE FEED COMPONENTS w w w g a r u d a n c z ...
Page 56: ...ANITA MP02300EN_170818 26 10 THREAD STAND COMPONENTS w w w g a r u d a n c z ...
Page 58: ...ANITA MP02300EN_170818 28 11 WIPER COMPONENTS w w w g a r u d a n c z ...
Page 64: ...ANITA MP02300EN_170818 34 13 OIL LUBRICATION COMPONENTS w w w g a r u d a n c z ...
Page 66: ...ANITA MP02300EN_170818 36 14 ACCESSORIE PART COMPONENTS w w w g a r u d a n c z ...
Page 68: ......