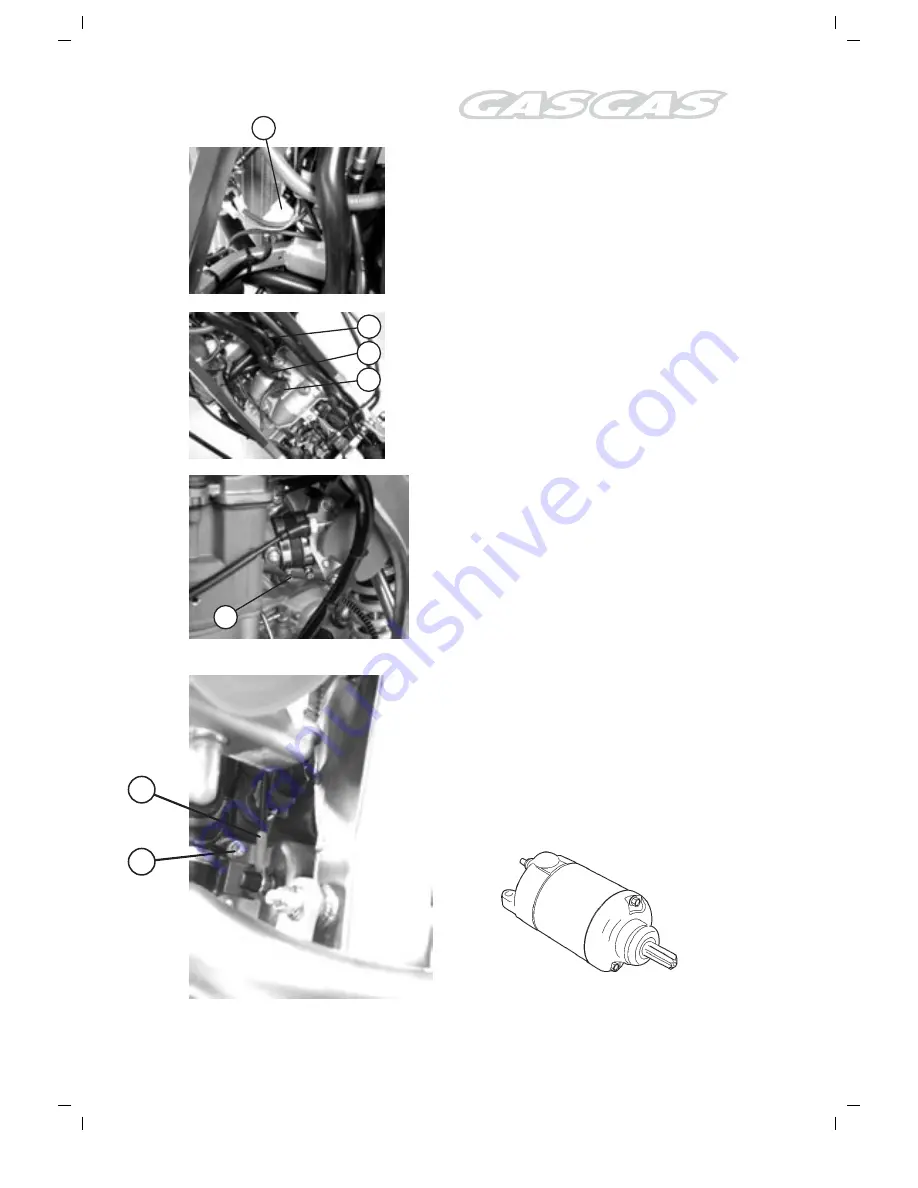
Engine Removal and Installation
89
Detach the wire clamp from the alternator (A) and
the sensor cable from the tonewheel.
Detach the spark-plug arm (1), the engine-oil
devaporizing tube (2), the engine-oil reservoir
breather pipe (3).
Loosen the clamp holding the cylinder head injector
conduit (4).
Detach the wire clamp from the water-temperature
sensor (5).
Detach the connecting cable from the starter (6)
and remove the starter.
3
1
2
4
A
5
6