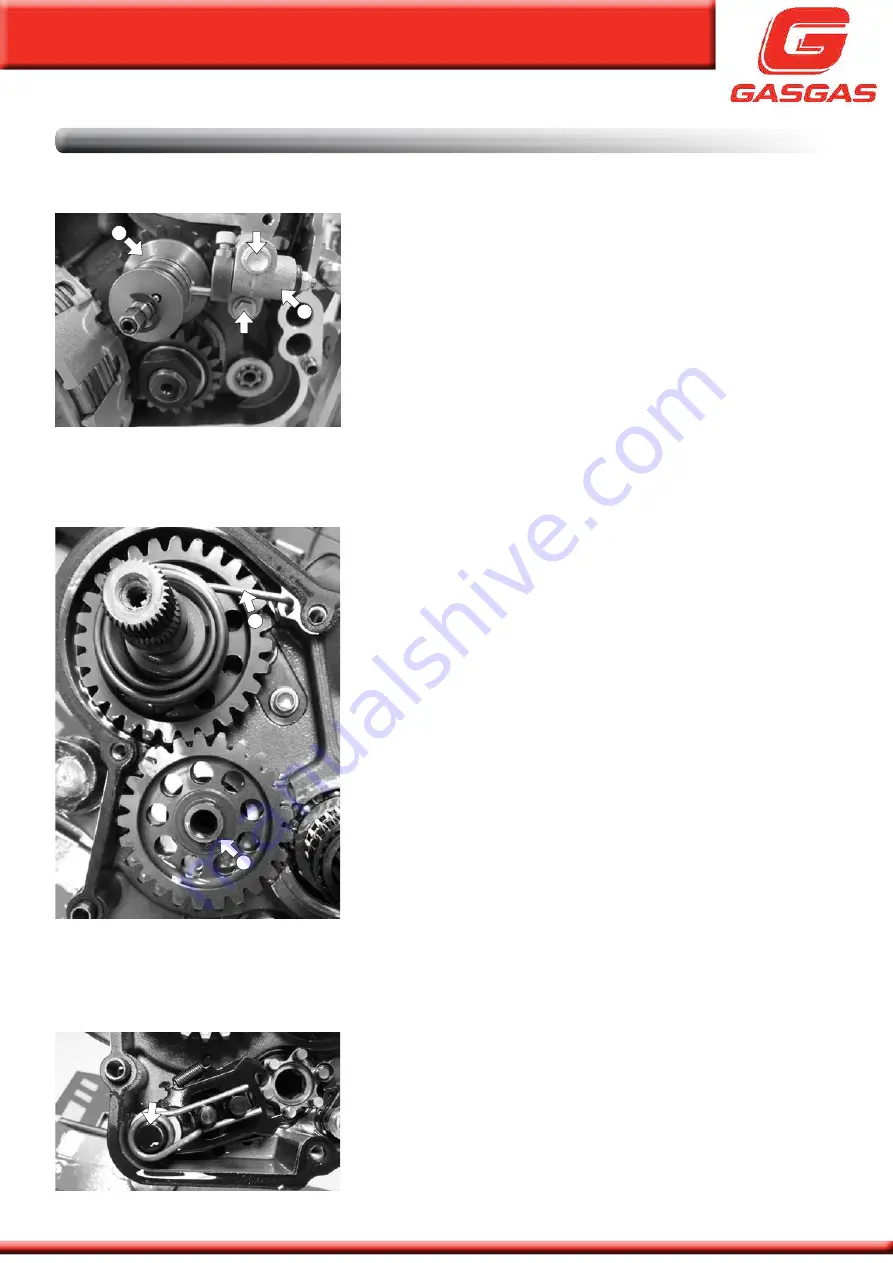
Workshop manual
-25-
REMOVING THE EXHAUST VALVE CENTRIFUGAL DRIVE SYSTEM
- Extract the screws (arrows) and remove the bracket (1) from the exhaust valve
control shaft.
- Detach the exhaust valve centrifugal drive (2).
REMOVING THE KICK-START SPROCKET ASSEMBLY
- Remove the spring (1) with a pair of pliers and detach the kick-start sprocket
assembly.
- Extract the retaining ring (2), remove the spacer washer and detach the inner
starter sprocket.
REMOVING THE GEAR SELECTOR ASSEMBLY
- Remove the entire selector shaft (arrow) by pulling it outwards.
Dismantling the engine
1
2
1
2
Summary of Contents for Enduro 2T 200CC
Page 1: ......
Page 5: ...Workshop manual 5 This page has been left blank intentionally General information...
Page 68: ...Workshop manual 68...
Page 69: ...Workshop manual 69...
Page 70: ...Workshop manual 70...
Page 71: ...Workshop manual 71 This page has been left blank intentionally...
Page 72: ......