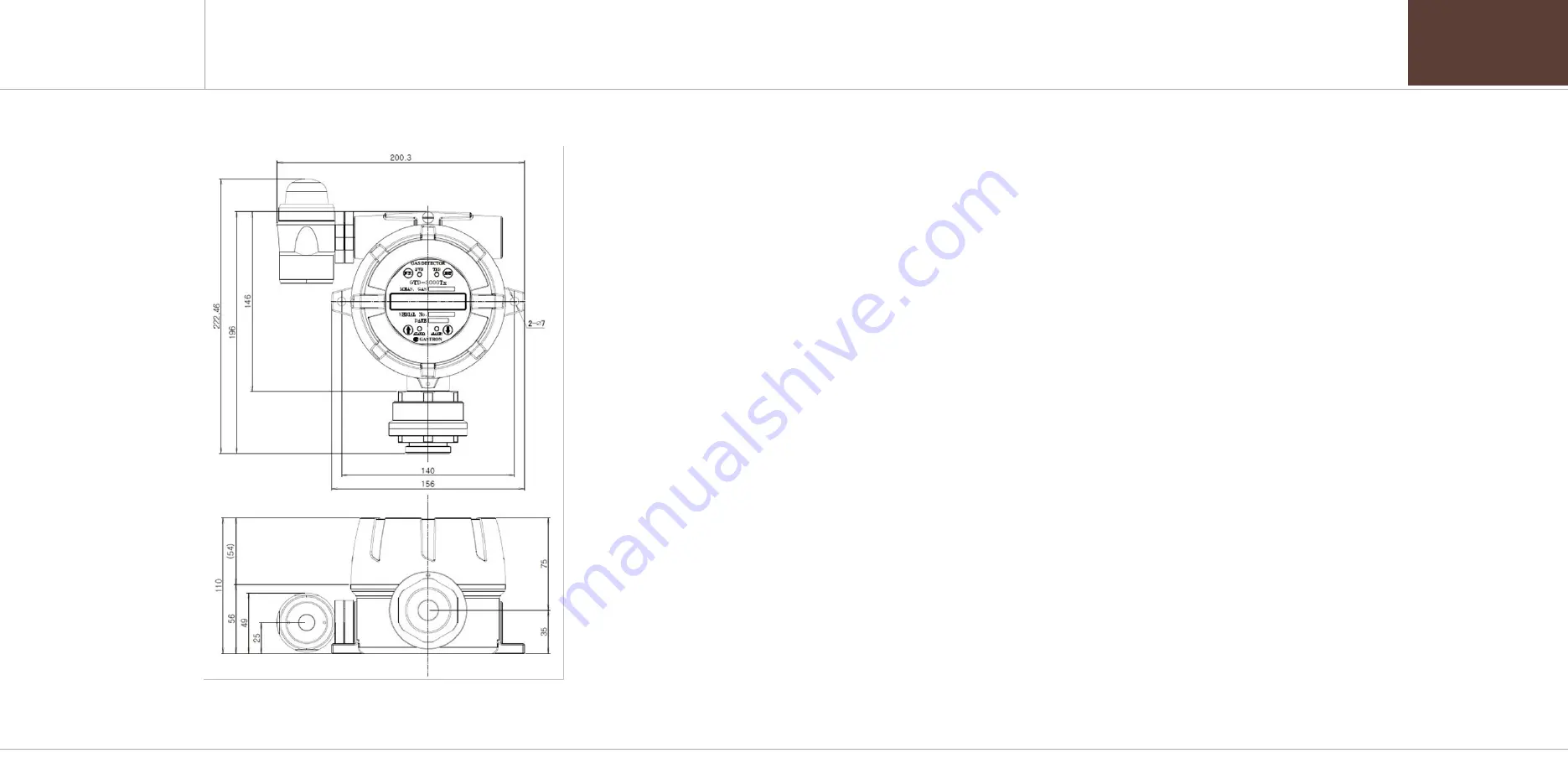
www.gastron.com
32
_
33
GTD-3000TxW
Instruction Manual
10. Drawings and Dimensions
10.3. When Connecting Warning Light
[Figure 16. GTD-3000TxW Warning Light Connection Drawing]
11. Precautions before Installation
11.1. Selecting a Place for Installation (Occupational Health & Safety Act Data)
A gas leak detector alarm shall be installed in the following places.
■
Around chemical equipment and accessories that have concerns of gas leak. This includes compressors, valves, reactors,
pipe joints, etc. installed inside and outside of a building that handle combustible and toxic materials.
■ Places that are easier for gases to stay such as areas around manufacturing facilities with ignition sources like heating
furnace, etc,
■ Areas around equipment for filling combustible and toxic materials.
■ Substations, panel rooms, control rooms, and etc. located within explosive area.
■ Other areas that are easier for gases to stay.
11.2. Selecting a Site for Installation (High-Pressure Gas Safety Control Act Data)
■
Gas detector of gas leak detector alarm must be installed as close to the areas with concerns of gas leakage as possible.
However, for areas where direct gas leakage is not expected but are easier for leaked gas to stay, the detector must be
installed at the point 1 of the following.
■ Gas leak detector alarm installed outside a building shall be installed at points where gas is likely to stay in
consideration to wind direction, wind speed, specific gravity of gas, etc.
■ Gas leak detector alarm installed inside a building shall be installed near the floor when the specific gravity of gas is
heavier than air and near ventilation of ceiling when it is lighter than air.
■ Alarm for gas leak detector alarm must be installed at sites where the gas detector is installed and workers are present.
11.3. Precautions during Installation
Avoid areas with electrical barriers such as rain water, etc. It is recommended to be installed in areas that are easier to
work in since regular maintenance is needed. Avoid areas with vibration or shock since they can affect output values.
Sensor part must be installed towards the direction of gravity.
■ This equipment has explosion-proof construction for internal pressure and belongs to GROUP II for gas and vapor in
general work sites and chemical plants. It can be used in ZONE 1 (ONE) and ZONE 2 (TWO) hazardous sites.
■ Allowable temperature is 85 C or below, which corresponds to T6.
■ Surrounding temperature shall be in a range of -20 to 60 °C (For the main unit and sensor, refer to each sensor manual.)
■ Installation Height: 1,000 M below sea level