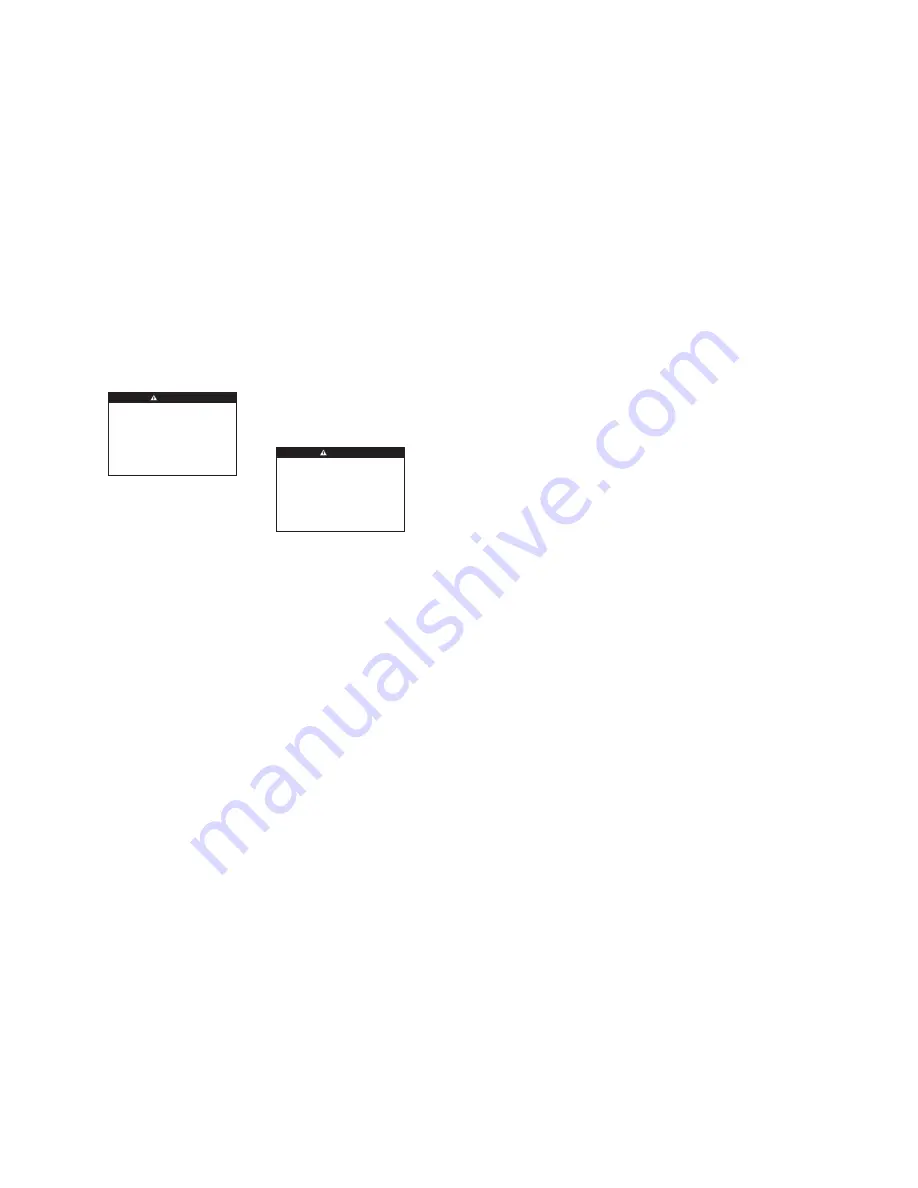
6. Unplug the Power Unit. Install filter. (Install
new filter every 1000 operating hours or 12
months, whichever occurs first.) Replace
the filter
only
with the Gaymar P/N listed
(see parts list, fig. 9, p. 24). Record the
hour timer reading onto the new filter label.
Reattach filter retainer and nut.
The HEPA filter must be seated
properly.
Failure to install the
filter correctly will prevent it from
functioning properly, and could
allow unfiltered air to reach the
patient and cause injury.
7. Replace the six screws holding the enclosure
together.
7.7 Quilt Temperature
Verify temperature output at each heat setting:
1. Prepare the Power Unit test setup, if it has
not been previously prepared:
a. Locate the air temperature sensor at
the center of the end of the hose (fig.
6A, p. 10). Secure the sensor with
adhesive tape.
Verify that the sensor
is located at the center of the hose.
b. Connect the hose to a Quilt (fig. 6B,
p. 10).
c. Plug in the Power Unit and turn it on.
2. Set the
TEMPERATURE SETTINGS
switch
to
LOW
. Run the Power Unit for 5 minutes.
After 5 minutes, note the two highest and
two lowest temperature readings. Record the
average of these four temperatures on the
INSPECTION FORM
(table 2, pp. 16-18).
Allowable LOW temperature:
87°F to 93°F average
(30.6°C to 33.9°C)
50. Reset the thermostats by gently pressing the
center reset buttons.
Use care when resetting the
thermostats.
Excessive force
(force greater than 5 pounds) can
damage the overtemp protection
device and/or inadvertently alter
the trip temperature of the device.
NOTE: Use care when resetting the
thermostats since the power terminals
are delicate. Avoid flexing the terminals.
Thermostats with loose terminals should
be replaced and retested.
7.6 Filter Replacement and Filter
Switch Test (every 12 months or 1000
operating hours, whichever occurs
first)
1. Unplug the Power Unit. Separate the two
halves of the enclosure. Lay the Power Unit
on its back.
2. Remove the filter retainer and nut. Remove
the filter.
3. Put the enclosure back together and secure
it with tape.
4. Plug in the Power Unit. Turn it on. Verify
that the blower does not start and that the
REMOVE FROM USE
light is lit.
5. A timer which counts total running hours
is located inside the Power Unit for use by
service personnel. Timer readings may be
used to track HEPA filter usage intervals. To
read the hour timer:
a. Unplug the Power Unit. Separate the
two halves of the enclosure again.
Locate the hour timer (see figure 10, p.
25). Plug in the Power Unit and turn it
on. Read the hour timer and record the
total running hours on the
INSPECTION
FORM.
b. Turn the Power Unit off.
Section 7 - Functional Check and Safety Inspection (cont’d)
14
W ARNING
CAUTIO N
3. Repeat step 2 for
MED
setting. Average
temperatures and record.
Allowable MED temperature:
97°F to 103°F average
(36.1°C to 39.4°C)
4. Repeat step 2 for
HIGH
setting. Average
temperatures and record.
Allowable HIGH temperature:
107°F to 113°F average
(41.7°C to 45.0°C)
5. If the temperatures in steps 2 through 4 are
not correct, do not put the Power Unit into
service. Call your local Dealer
6. Unplug the Power Unit.
7.8 Ground Resistance
Check grounding resistance:
1. Use a current leakage/ground resistance
tester to measure the resistance between the
grounding pin on the power entry module
and the I. V. pole clamp. An unplated area
on the underside of the I. V. pole clamp has
been provided for this test. Record the value.
2. The value should be less than 0.5 ohms.
7.9 Current Leakage
Measure current leakage:
1. Measure and record the maximum earth
current leakage (ground open). An unplated
area on the underside of the I. V. pole clamp
has been provided if needed for this test.
Measure at all combinations of:
• line polarity
• neutral open/closed
2. The current leakage should not exceed 100
microamperes in any condition.
Section 7 - Functional Check and Safety Inspection (cont’d)
15
7.10 Completing the Functional Check
and Safety Inspection
If the Power Unit has passed the
FUNCTIONAL
CHECK AND SAFETY INSPECTION
for all
requirements of procedures 7.1 through 7.9, the
Power Unit should be considered operational and
suitable for return to service.
This completes the recommended
FUNCTIONAL
CHECK AND SAFETY INSPECTION
for the TC3249
series Power Unit.