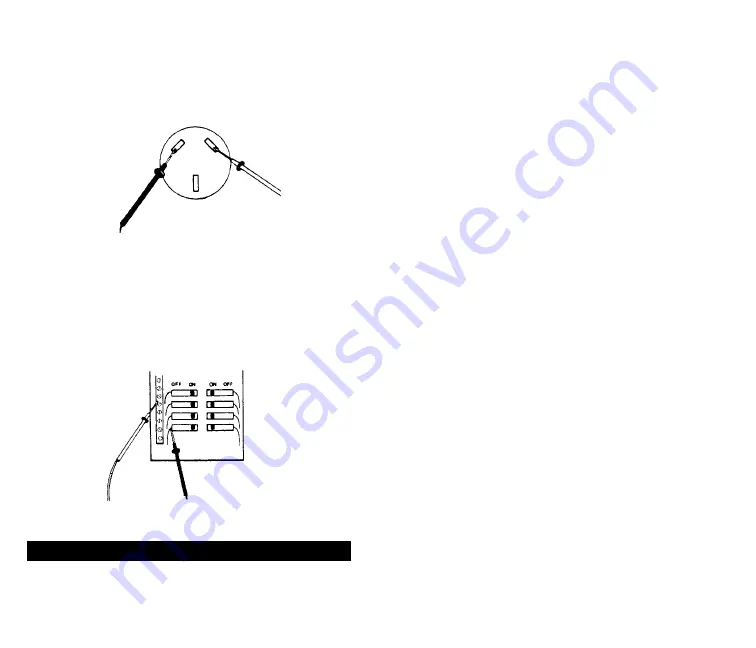
11
12
2) Set the function/range switch to the Rx1K position
(resistance indicated multiplied by 1000) and short the test
leads together. Using the zero ohms adjustment dial,
slowly turn the dial until the needle indicator reads -0-
ohms at the right end of the ohms scale. If the needle will
not zero, replace the internal battery with one new 1.5 volt
AA size battery (see Battery Replacement ).
3) Touch the test leads to the resistance or non-energized
circuit to be measured. Measure the value of the reading
on the ohms scale and multiply the reading by 1000. If
you’re making basic continuity tests, the needle indicator
should move all the way to the right side of the ohms scale
if continuity exists.
Note: When switching the unit back and forth from ohms
to other functions, always zero the needle indicator before
taking another reading. Failure to zero the needle before
taking resistance/continuity measurements will result in
inaccurate readings.
Common Resistance and
Continuity Measurements
Continuity tests are probably the most frequently performed
electrical troubleshooting procedures around the home.
ALWAYS REMEMBER THAT CONTINUITY CHECKS
ARE TO BE MADE WITH THE POWER TO THE CIRCUIT
TURNED OFF. Polarity of the test leads is not a factor in
making continuity checks.
7.1 Extension Cords
Unplug the cord. Set the function/range switch to the Rx1K
position. Touch one of the test leads to one of the metal prong
ends of the cord, and insert the other test lead in either one of
the receptacle slots on the other end of the cord, making sure
the test lead is making good contact with the receptacle (see
fig. 9). If the needle indicator does not move to -0- ohms,
insert the test lead into the other receptacle slot, again making
sure of good contact. If the needle indicator does not move to
-0- ohms the cord should be replaced.
6.2 Appliance Receptacles
Set the function/range switch to 250 VAC. Touch the test
leads to the receptacle slots. The tester should read 240 VAC
between the two “hot” sides of the receptacle, and 120 VAC
between the neutral slot and either of the two “hot” sides
(see fig. 7).
6.3 Circuit Breaker Panel
To test for defective circuit breakers, set the function/range
switch to the 250 VAC or 600 VAC settings. Touch one test
lead to the neutral (buss) terminal strip of the breaker panel
and the other test lead to the terminal on the circuit breaker
(see fig. 8). The tester should read 120 VAC on the
0-250 scale.
For resistance and continuity testing POWER MUST BE OFF:
1) Fully seat the test leads in the input jacks.
Figure 7
7.0 Resistance/Continuity Measurement
Figure 8
Summary of Contents for GMT-18A
Page 28: ...53 54 Notes Notes...