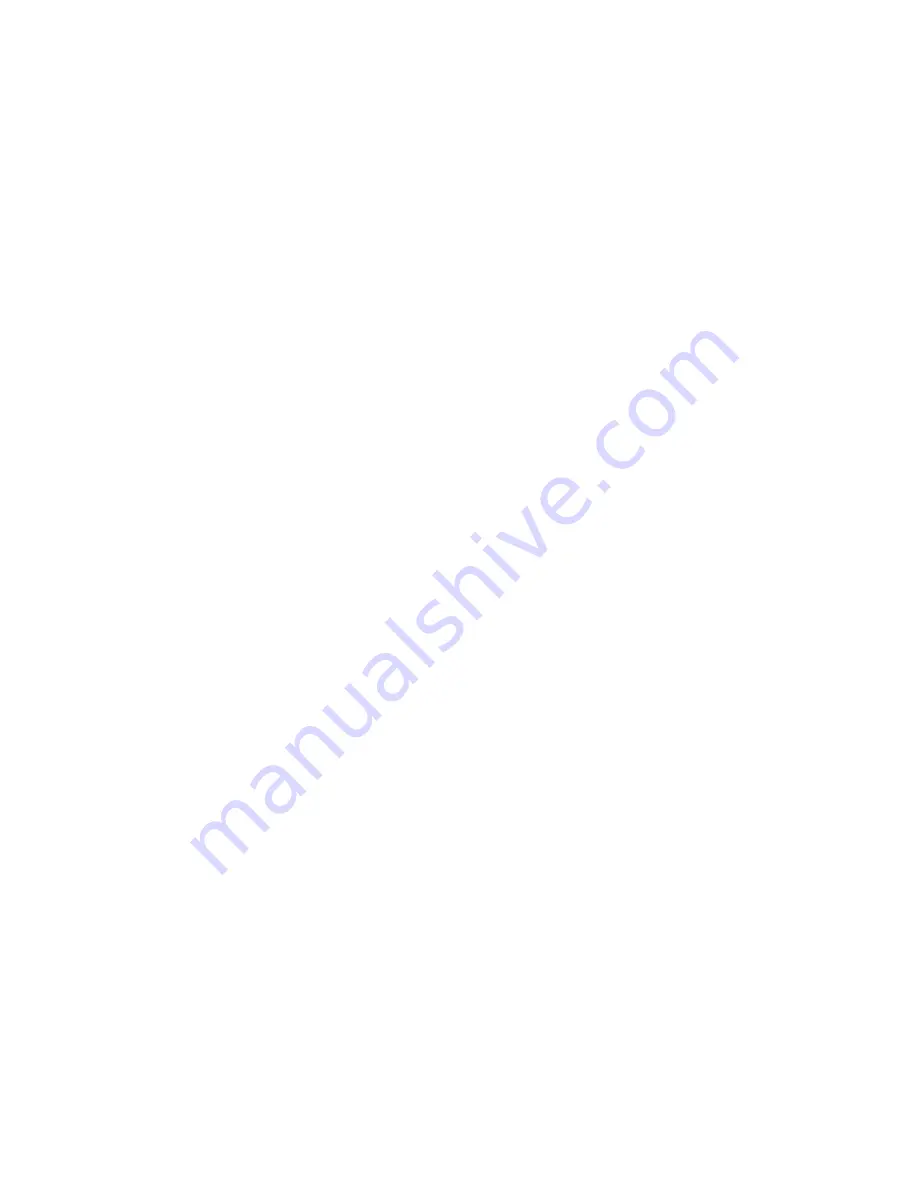
Placement
Environment is to be clean, dry, and indoors. Unit is to remain above floor (rack and 4 wheel casters are provided). The system
is designed to fit under a counter as a corner unit or next to an existing under counter item. The system should be located
in a climate controlled environment where it is protected from extreme hot or cold temperatures. The system must be easily
accessed for monitoring and service. Service area must permit access to all of the filter housings for removal and replacement
of elements or cartridges.
Installation Notes
1. RO unit can be mounted up to 7’ away. Additional distances are available.
2.
Lines to POU: espresso machines, coffee brewers, water tower, and ice machine lines are owner plumbed. Lines to Points
Of Use (POU) are to be Owner-Plumbed. Never include toilets, sinks, or dipper well.
3.
Owner supplied shut off ball valves at city feed. Pipe and valve size must match site requirements.
4. Owner to provide GFCI electrical outlet.
5. The drain line must be attached and installed according to local city code. Usually with an air gap that has an unobstructed
vertical distance through free atmosphere between the lowest opening from any pipe, plumbing fixture, appliance or other
piece of equipment conveying waste to the flood level rim of the receptor. The vertical distance between the conveyor and
receptor shall be no less than 1 inch.
6. Installation must comply with existing local plumbing codes. Air gaps must comply with drawings or an approved air gap
device may be used. In addition some local plumbing codes require back flow devices. Both the air gap device and back
flow device are not supplied as part of the unit. These devices are available through your standard plumbing supply house.
7. RO equipment must not be plumbed to dipper well, toilets or wash sinks. They a re to be on city water only.
8. City feed should be as direct as possible to prevent any pressure drops.
Installation Precautions
• The system must be installed with the inlets/outlets/drain as shown. Do not to reverse connections.
• Do not install on hot water line.
• Maximum temperature allowed is 80°F (38°C).
• A pressure regulator is required on incoming water pressure over 90 psi.
•
Use Teflon tape for connections. Do not use wicking or sealer for fitting connections.
•
Do not use torch or other high temperature sources near filter, cartridges, or any plastic fittings and pipes.
• Installation must comply with existing local plumbing codes.
• Do not install in direct sunlight.
• Protect from freezing. Do not install in area that will drop to 32°F (0°C) or below.
• Allow minimum service clearance space as shown in layouts to facilitate routine maintenance.
• Mount system in a position and location so as to prevent system from being struck by items.
Lines to Points Of Use (POU) are to be owner plumbed. Never include toilets, sinks, or dipper well. Never hook RO up to hot water.
INSTALLATION NOTES
PAGE 6