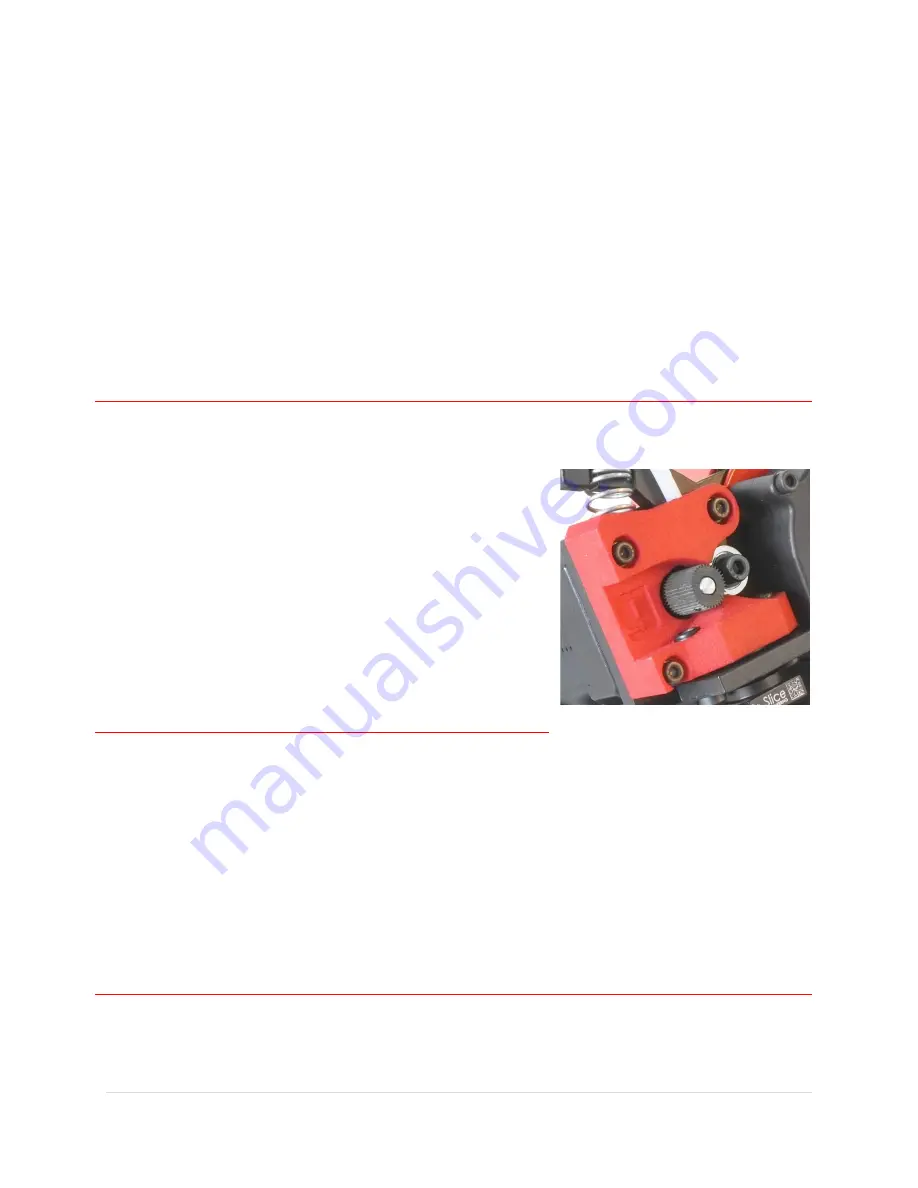
Page 17
•
Make sure the swing arm M4 bolt holding the U groove bearing is tight.
BLtouch Replace Pin
If the pin on your BLTouch leveling sensor broke off, you can easily replace it.
1.
Turn off the printer.
2.
Remove the (2) bolts holding the BLTouch to the extruder bracket allowing it to drop down.
3.
On the top of the sensor, remove the set screw allowing the pin to be removed from the top.
4.
Insert the new pin, and tighten the set screw until its flush with the top of the sensor housing.
5.
Reinstall the sensor on the gMax extruder.
Replace Drive Gear
The gMax uses a hardened steel sharp drive gear to push the filament into the extruder. It may wear
down after long usage and replacing it is simple.
1.
Loosen the set screw on the drive gear using a hex key.
2.
Pull it off the motor shaft.
3.
When installing the new one you will see a flat spot on
the gear that will match a flat spot on the motor shaft.
Slide it on and tighten the set screw.
4.
Make sure the set screw is not in the path of the
filament.
Tightening Bolts and Frame
Due to temperature differences and plastic fatigue, you should check the bolts on the gMax periodically
to ensure they are tight.
Common areas to check are:
•
The extruder assembly where it attaches to the x-axis.
•
The extruder hotend bolts.
•
Extruder bolts. Make sure the swing arm can still swing freely.
•
Bed carriage where it connects to the linear rail blocks. M4 button head bolts.
•
Runout sensor switch sensor.
Adjust Lead Screw
The gMax 2 uses a TR10*4 lead screw and a machined POM nut. The lead screw is 10mm and has a
4mm pitch to combine speed and accuracy.
Summary of Contents for gMax 2 PRO
Page 21: ...Page 21 Other...