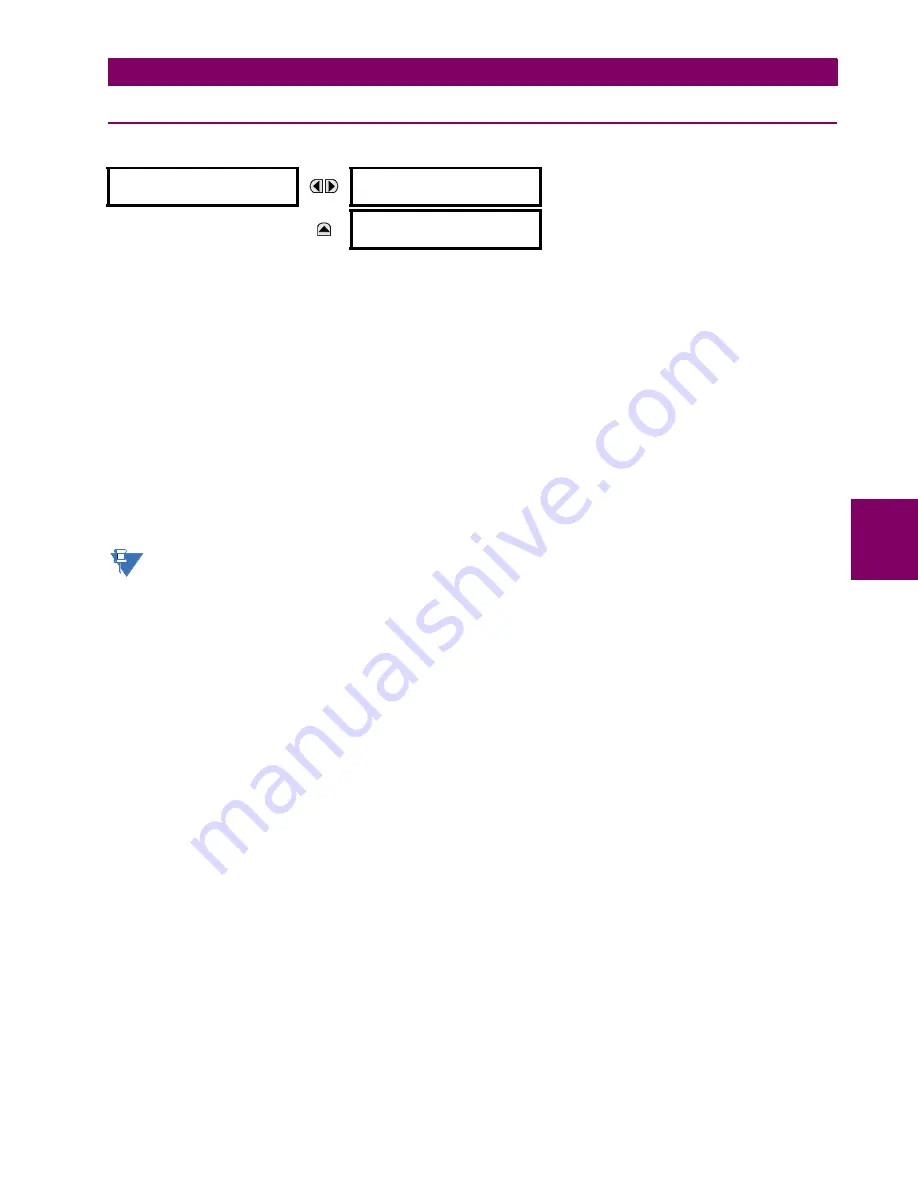
GE Multilin
F60 Feeder Protection System
5-311
5 SETTINGS
5.10 TESTING
5
5.10TESTING
5.10.1 TEST MODE
PATH: SETTINGS
TESTING
TEST MODE
The F60 provides a test facility to verify the functionality of contact inputs and outputs, some communication functions and
the phasor measurement unit (where applicable), using simulated conditions. The test mode is indicated on the relay face-
plate by a Test Mode LED indicator.
The test mode may be in any of three states: disabled, isolated, or forcible.
In the “Disabled” mode, F60 operation is normal and all test features are disabled.
In the “Isolated” mode, the F60 is prevented from performing certain control actions, including tripping via contact outputs.
All relay contact outputs, including latching outputs, are disabled. Channel tests and phasor measurement unit tests remain
usable on applicable UR-series models.
In the “Forcible” mode, the operand selected by the
TEST MODE FORCING
setting controls the relay inputs and outputs. If the
test mode is forcible, and the operand assigned to the
TEST MODE FORCING
setting is “Off”, the F60 inputs and outputs oper-
ate normally. If the test mode is forcible, and the operand assigned to the
TEST MODE FORCING
setting is “On”, the F60 con-
tact inputs and outputs are forced to the values specified in the following sections. Forcing may be controlled by manually
changing the operand selected by the
TEST MODE FORCING
setting between on and off, or by selecting a user-programma-
ble pushbutton, contact input, or communication-based input operand. Channel tests and phasor measurement unit tests
remain usable on applicable UR-series models.
Communications based inputs and outputs remain fully operational in test mode. If a control action is programmed
using direct inputs and outputs or remote inputs and outputs, then the test procedure must take this into account.
When in “Forcible” mode, the operand selected by the
TEST MODE FORCING
setting dictates further response of the F60 to
testing conditions. To force contact inputs and outputs through relay settings, set
TEST MODE FORCING
to “On”. To force con-
tact inputs and outputs through a user-programmable condition, such as FlexLogic operand (pushbutton, contact input,
communication-based input, or a combination of these), set
TEST MODE FORCING
to the desired operand. The contact input
or output is forced when the selected operand assumes a logic 1 state.
The F60 remains fully operational in test mode, allowing for various testing procedures. In particular, the protection and
control elements, FlexLogic, and communication-based inputs and outputs function normally.
The only difference between the normal operation and the test mode is the behavior of the input and output contacts. The
contact inputs can be forced to report as open or closed or remain fully operational, whereas the contact outputs can be
forced to open, close, freeze, or remain fully operational. The response of the contact input and output contacts to the test
mode is programmed individually for each input and output using the force contact inputs and force contact outputs test
functions described in the following sections.
The test mode state is indicated on the relay faceplate by a combination of the Test Mode LED indicator, the In-Service LED
indicator, and by the critical fail relay, as shown in the following table.
SETTINGS
TESTING
TEST MODE
FUNCTION: Disabled
Range: Disabled, Isolated, Forcible
MESSAGE
TEST MODE FORCING:
On
Range: FlexLogic operand
NOTE
Summary of Contents for F60
Page 10: ...x F60 Feeder Protection System GE Multilin TABLE OF CONTENTS ...
Page 30: ...1 20 F60 Feeder Protection System GE Multilin 1 5 USING THE RELAY 1 GETTING STARTED 1 ...
Page 138: ...4 28 F60 Feeder Protection System GE Multilin 4 2 FACEPLATE INTERFACE 4 HUMAN INTERFACES 4 ...
Page 454: ...5 316 F60 Feeder Protection System GE Multilin 5 10 TESTING 5 SETTINGS 5 ...
Page 500: ...7 14 F60 Feeder Protection System GE Multilin 7 1 COMMANDS 7 COMMANDS AND TARGETS 7 ...
Page 508: ...8 8 F60 Feeder Protection System GE Multilin 8 2 FAULT LOCATOR 8 THEORY OF OPERATION 8 ...
Page 522: ...10 12 F60 Feeder Protection System GE Multilin 10 6 DISPOSAL 10 MAINTENANCE 10 ...
Page 660: ...B 116 F60 Feeder Protection System GE Multilin B 4 MEMORY MAPPING APPENDIX B B ...
Page 706: ...E 10 F60 Feeder Protection System GE Multilin E 1 IEC 60870 5 104 APPENDIX E E ...
Page 718: ...F 12 F60 Feeder Protection System GE Multilin F 2 DNP POINT LISTS APPENDIX F F ...
Page 728: ...H 8 F60 Feeder Protection System GE Multilin H 2 ABBREVIATIONS APPENDIX H H Z Impedance Zone ...
Page 730: ...H 10 F60 Feeder Protection System GE Multilin H 3 WARRANTY APPENDIX H H ...