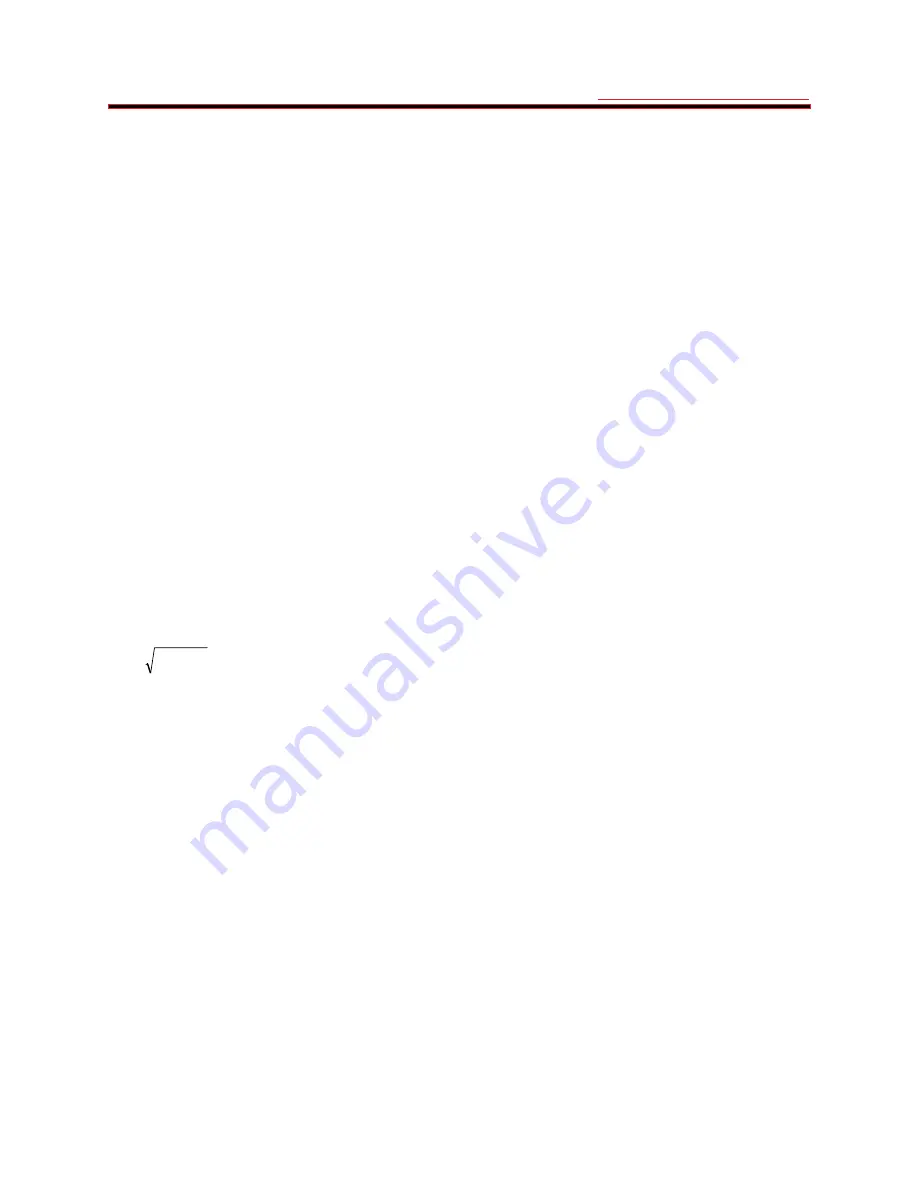
3 SETUP AND USE
g
GE Power Management
69
3.19 Phase Reversal Protection
Phase reversal protection is provided on the 169 to detect improper connection of incoming phases. The order of
the incoming phases must be as shown in figure 2-4 in order for the proper sequence to be detected. This feature
can be enabled or disabled by a setpoint in page 5 of SETPOINTS mode. A phase reversal trip will occur when the
motor is started, if the phases are out of sequence, within 3.5 seconds.
3.20 Thermal Memory
The 169 relay uses an internal thermal memory register to represent the thermal capacity of the motor. To "fill" this
register, the square of the equivalent motor heating current is integrated over time. This equivalent current is a
biased average of the 3 phase currents. The biasing factor is derived from the amount of negative sequence current
flowing in the motor (on a 169 Plus if the U/B input to TC is enabled). The rate at which the memory fills is thus
dependent on the amount of overload, unbalance present, as well as RTD bias. The unbalance input to thermal
memory as well as RTD bias can be defeated using a setpoint in page 5 of SETPOINTS mode. When the thermal
memory register fills to a value corresponding to 100% motor thermal capacity used, an OVERLOAD TRIP will be
initiated. This value is determined from the overload curve.
Thermal memory is emptied in certain situations. If the motor is in a stopped state the memory will discharge within
the motor STOPPED COOL TIME (factory value = 30 min.). If the motor is running at less than full load, thermal
memory will discharge at a programmed rate to a certain value. This value is determined by the "FLC Thermal
Capacity Reduction" setpoint. For example, a value of 25% may be chosen for this setpoint. If the current being
drawn by the motor drops below full load current to 80%, then the thermal memory will empty to 80% of the FLC
Thermal Capacity Reduction setpoint, namely, 20% (0.8 x 25%). In this way the thermal memory will discharge to an
amount related to the present motor current in order to represent the actual temperature of the motor closely.
Thermal memory will discharge at the correct rate which is approximately exponential, even if control power is
removed from the 169. Thermal memory can be cleared to 0% by using the Emergency Restart feature (see section
3.21).
U/B INPUT TO THERMAL MEMORY - When U/B input to thermal memory is defeated the 169 Plus relay will use the
average of the three phase currents for all overload calculations (i.e. any time the overload curve is active). When
U/B input to thermal memory is enabled the 169 Plus relay will use the equivalent motor heating current calculated
as shown:
I
eq
= I
avg
(with U/B input to thermal memory disabled; factory preset)
2
2
n
p
eq
KI
I
I
+
=
(with U/B input to thermal memory enabled)
where:
K = (Istart/Iflc)
2
/ 7.41 or user entered value (negative sequence current heating factor; see below)
I
eq
= equivalent motor heating current
I
avg
= average of three phase currents
I
p
= positive sequence component of phase current
I
n
= negative sequence component of phase current
Thus the larger the value for K the greater the effect of current unbalance on the thermal memory of the 169 relay.
RTD INPUT TO THERMAL MEMORY - The RTD Input to Thermal Memory may be used to protect against loss of
motor cooling and also to serve as a double check for the thermal model. For example, the thermal model is based
on motor running currents. This model does not take into account loss of motor cooling, therefore the RTD bias may
be used for this function.
When the hottest stator RTD temperature is included in the thermal memory (SETPOINTS mode, page 5; factory
preset disabled) the maximum measured stator RTD temperature is used to bias the thermal memory. The thermal
capacity available in the relay is reduced proportional to the RTD stator temperature. When the stator temperature
is at the RTD bias curve maximum value (SETPOINTS mode, page 5) the remaining thermal capacity available will
be reduced to 0%. The capacity will not be reduced at all when the RTD stator temperature is at the RTD bias curve
minimum value or below (SETPOINTS mode, page 5). Between these extremes thermal capacity reduction
increases linearly with the maximum stator temperature, as shown in Figure 3-4. The RTD temperature input to
thermal memory can be enabled in SETPOINTS mode, page 5.
An example of how the RTD input to thermal memory affects the thermal capacity available is described below and
illustrated in Figure 3-4. If curve 1 is used (i.e. factory preset values) and the stator temperature is 130 C, the
available thermal capacity will be reduced to 59%. If the RTD bias curve minimum and maximum values are
Summary of Contents for 169
Page 12: ......
Page 14: ...2 INSTALLATION g GE Power Management 8 Figure 2 2 CT Dimensions ...
Page 17: ...2 INSTALLATION g GE Power Management 11 Figure 2 4 Relay Wiring Diagram AC control power ...
Page 19: ...2 INSTALLATION g GE Power Management 13 Figure 2 6 Relay Wiring Diagram Two Phase CTs ...
Page 20: ...2 INSTALLATION g GE Power Management 14 Figure 2 7 Relay Wiring Diagram DC Control Power ...
Page 28: ...2 INSTALLATION g GE Power Management 22 Figure 2 10 169 Drawout Relay Physical Dimensions ...
Page 29: ...2 INSTALLATION g GE Power Management 23 Figure 2 11 169 Drawout Relay Mounting ...
Page 31: ...3 SETUP AND USE g GE Power Management 25 Figure 3 1 Front Panel Controls and Indicators ...
Page 73: ...3 SETUP AND USE g GE Power Management 67 Figure 3 2 Standard Overload Curves ...
Page 74: ...3 SETUP AND USE g GE Power Management 68 A B Figure 3 3 Custom Curve Examples ...
Page 88: ...5 THEORY OF OPERATION g GE Power Management 82 Figure 5 1 Hardware Block Diagram ...
Page 90: ...5 THEORY OF OPERATION g GE Power Management 84 Figure 5 2 Firmware Block Diagram ...