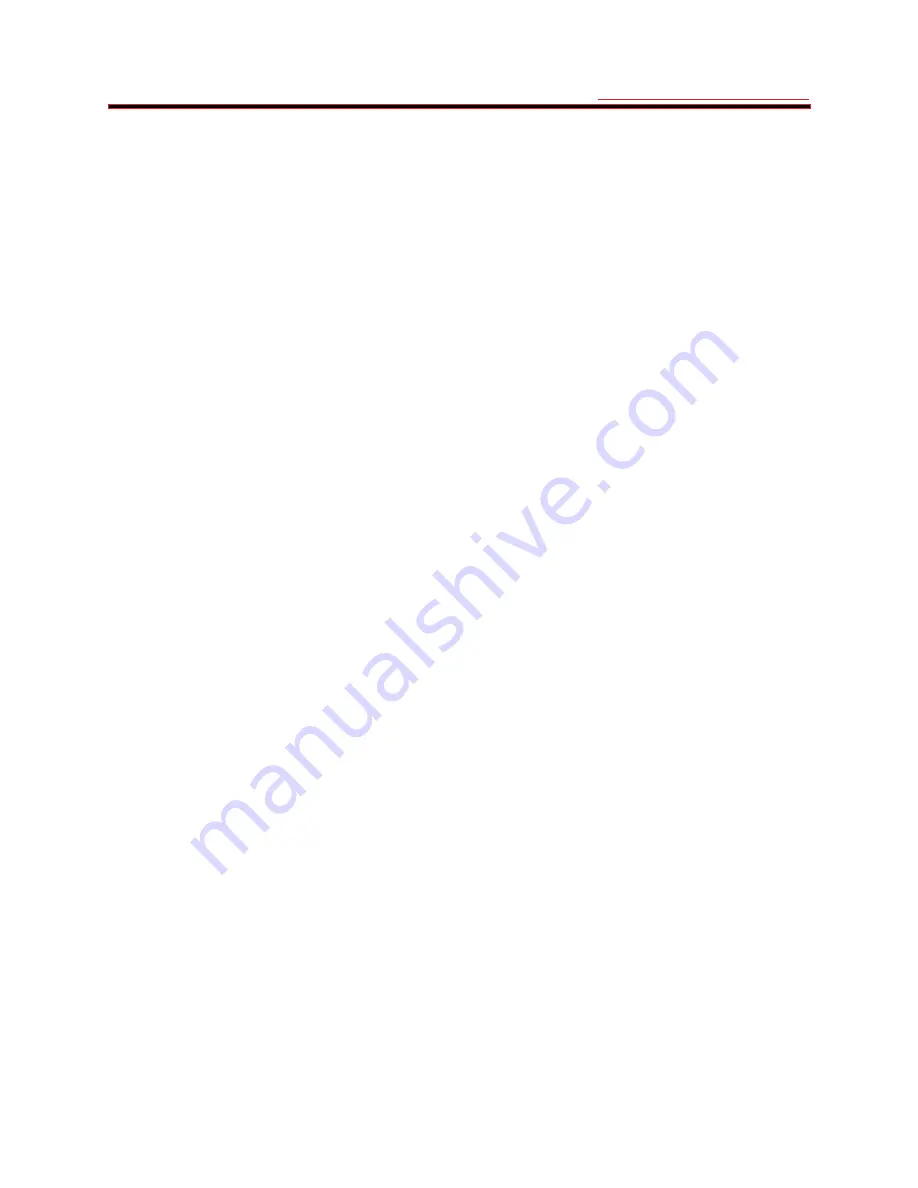
5 THEORY OF OPERATION
g
GE Power Management
83
5.2 Firmware
All mathematical, logic and control functions are performed on an 8031 microcomputer by a program stored on a
separate EPROM. The program execution flow is shown in the firmware block diagram of figure 5-2.
Every 2 ms the system clock generates an interrupt. At this time all timers are updated, the keypad is read and
debounced, and five A/D conversions are performed by the A/D module. These conversions are the ground fault
current reading, three phase current readings, and a single RTD, voltage reference, or power fail circuit reading. At
this point the RMS values of the currents are calculated, and short circuit and ground fault tests are made. The EOC
interrupt routine checks for a motor start condition and if this is true the phase sequence is checked, a start timer is
initiated, and the start register is updated.
The INITIALIZE module is performed whenever the relay is powered on to ensure that the system comes up in a
known state. Parts of this module are executed whenever the relay is reset as well. The SYSTEM EXECUTIVE then
causes execution to loop through a series of modules which perform most of the relay functions.
The O/L module uses the positive to negative sequence current ratio calculated by the U/B module, the learned K
factor, and the RMS phase currents to fill a thermal memory register. The O/L module discharges this register at
either a learned or preset cooling rate when no overload is present. The average stator RTD temperature calculated
in the RTD module is used to bias the thermal memory. This module also compares the RMS phase current values
to the Undercurrent and Rapid Trip / Mechanical Jam trip and alarm levels, and starts appropriate timers if the
current levels are out of range.
The U/B module computes the phase current ratios Ib/Ia and Ic/Ia, and uses them in conjunction with a look-up table
to determine the negative to positive sequence current unbalance ratio In/Ip. This value is compared to the
Unbalance trip and alarm levels and appropriate timers are initiated if trip/alarm conditions are met.
The RTD module uses the RTD voltage reading from each of the 10 RTD inputs and computes the average stator
RTD temperature. This is then used to bias the thermal memory. The RTD readings are compared to the trip and
alarm levels and relay activation is initiated if conditions are met. Each RTD is read 128 times over a one second
scan interval.
The KEYSERVICE/EXTERNAL SWITCH module takes in all of the data associated with the keypad and executes
the function of each key. Timers for the closure times of the VALUE UP/DOWN, PAGE UP/DOWN, and LINE
UP/DOWN keys are initiated and the display is updated accordingly. This module also reads the Emergency
Restart, External Reset, Differential Relay, and Speed Switch inputs and initiates appropriate action.
The MESSAGE module handles all of the message look-up functions and sends the message data to the display.
The displayed messages are made up of individual messages, common message strings, and variable data. Non-
displayed control bytes are used to indicate the message type, variable data type, decimal point placement, and
other control information.
The D/A module gives the DAC the current digital value for the selected option output for conversion to an analog
value. This analog voltage is then fed to a voltage-to-current converter circuit.
The SELF-TEST module causes the 8031 to send out regular voltage signals to indicate to the power supply
watchdog circuit that the system is operating properly. This module also performs all of the self-test features outlined
in section 3.23.
The TRIP/ALARM module is executed when any relay trip or alarm setpoint has been exceeded. This module
handles output relay activation and TRIP/ALARM message output.
Statistical data is updated whenever a statistical value changes. For example, the total number of motor starts value
is updated every time a motor start is detected.
Summary of Contents for 169
Page 12: ......
Page 14: ...2 INSTALLATION g GE Power Management 8 Figure 2 2 CT Dimensions ...
Page 17: ...2 INSTALLATION g GE Power Management 11 Figure 2 4 Relay Wiring Diagram AC control power ...
Page 19: ...2 INSTALLATION g GE Power Management 13 Figure 2 6 Relay Wiring Diagram Two Phase CTs ...
Page 20: ...2 INSTALLATION g GE Power Management 14 Figure 2 7 Relay Wiring Diagram DC Control Power ...
Page 28: ...2 INSTALLATION g GE Power Management 22 Figure 2 10 169 Drawout Relay Physical Dimensions ...
Page 29: ...2 INSTALLATION g GE Power Management 23 Figure 2 11 169 Drawout Relay Mounting ...
Page 31: ...3 SETUP AND USE g GE Power Management 25 Figure 3 1 Front Panel Controls and Indicators ...
Page 73: ...3 SETUP AND USE g GE Power Management 67 Figure 3 2 Standard Overload Curves ...
Page 74: ...3 SETUP AND USE g GE Power Management 68 A B Figure 3 3 Custom Curve Examples ...
Page 88: ...5 THEORY OF OPERATION g GE Power Management 82 Figure 5 1 Hardware Block Diagram ...
Page 90: ...5 THEORY OF OPERATION g GE Power Management 84 Figure 5 2 Firmware Block Diagram ...