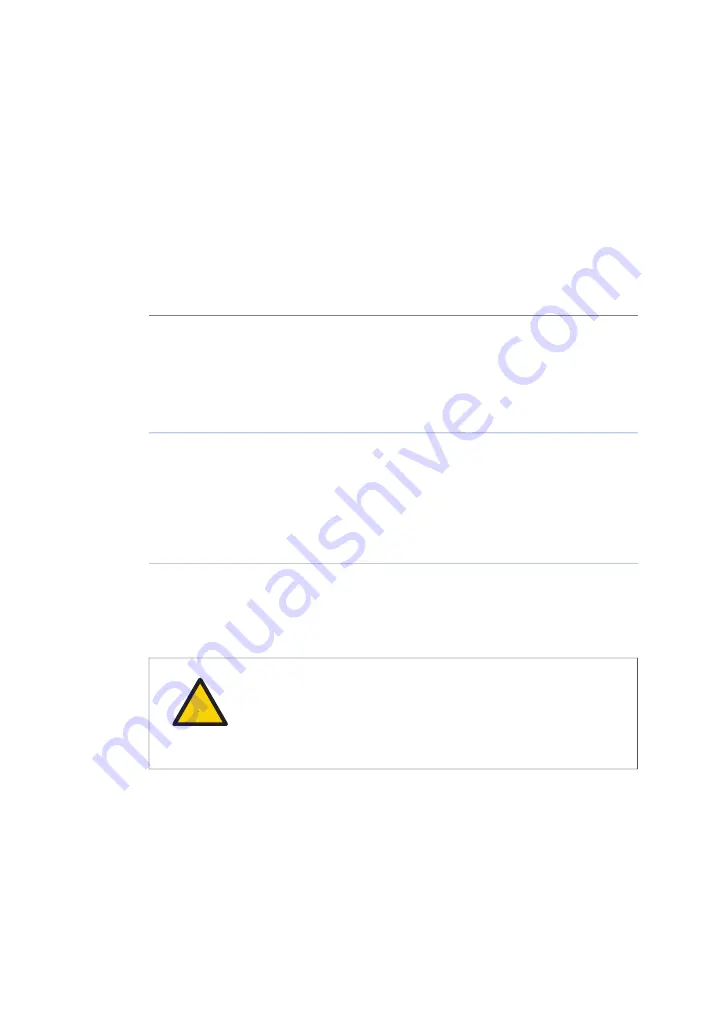
6
Maintenance
About this chapter
This chapter describes how to disassemble and reassemble the major components of
the column and how to replace seals and O-rings. Cleaning and storage of BioProcess
LPLC and MPLC columns is also described.
In this chapter
This chapter contains the following sections:
See page
Section
6.2 Changing O-rings and seals
Precautions
EX
WARNING
EXPLOSION HAZARD! When a BioProcess LPLC or MPLC column is
operated or maintained in a potentially explosive atmosphere, it
MUST be properly grounded to avoid static discharge.
68
LPLC and MPLC Columns Operating Instructions 28-9638-66 AC
6 Maintenance