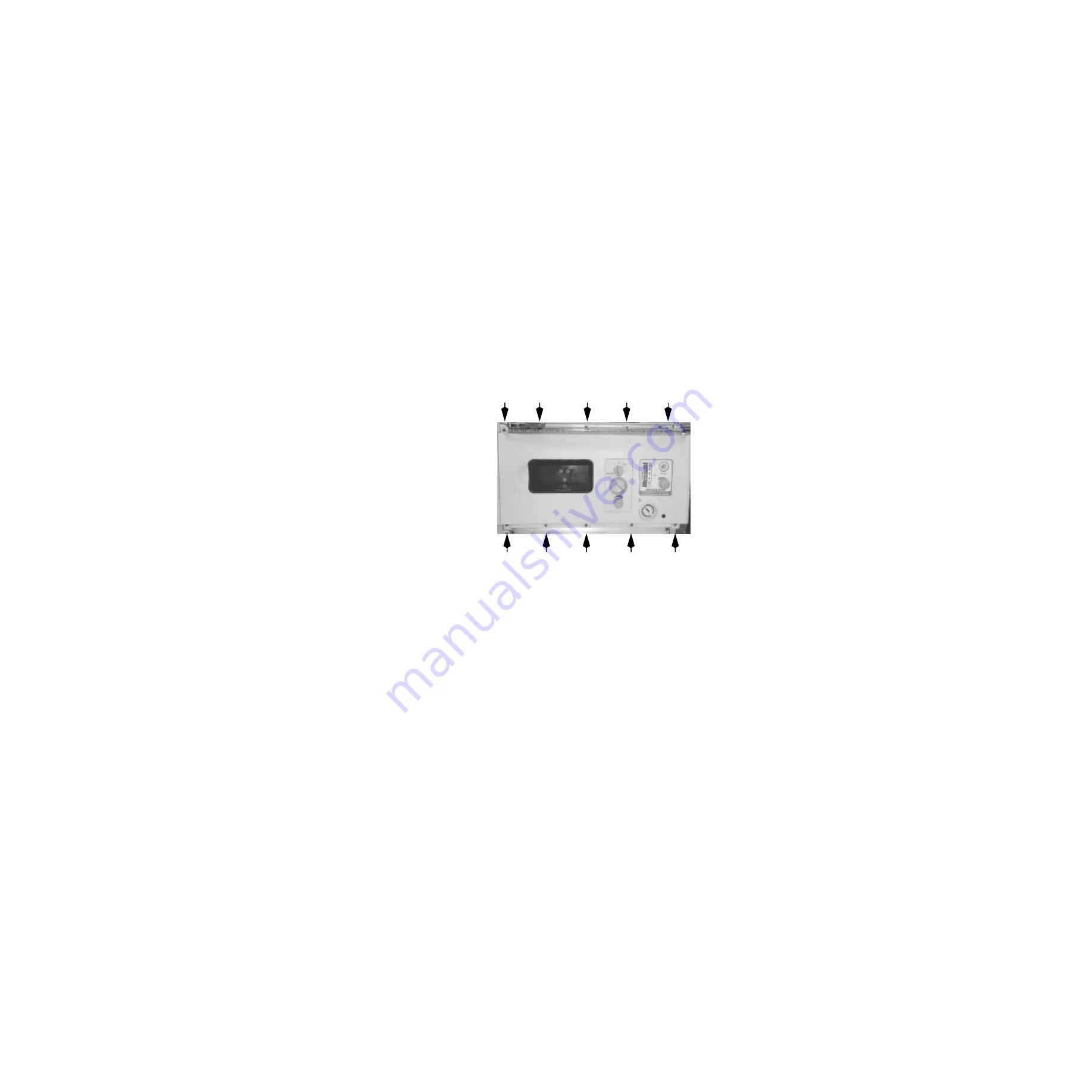
Aisys
9-10
04/08 M1046983
9.6 How to access dashboard components
1. Bleed all gas pressure from the machine (Section 9.2).
2. Ensure that all cylinder and pipeline pressures read zero before proceeding.
3. Remove the tabletop (Section 9.4).
4. Remove the upper bezel located above the dashboard.
5. Loosen 10 captive dashboard mounting screws and move the dashboard forward to
the stop position.
w
CAUTION
When replacing the dashboard back into the machine, take care not to trap, kink,
or snag any tubing or wiring harnesses.
Summary of Contents for Datex-Ohmeda Aisys Carestation
Page 1: ...Aisys Anesthesia Machine Technical Reference Manual ...
Page 16: ...Notes xiv 04 08 M1046983 ...
Page 32: ...Notes 1 16 04 08 M1046983 ...
Page 158: ...Notes 5 20 04 08 M1046983 ...
Page 288: ...Notes 7 106 04 08 M1046983 ...
Page 325: ...9 Repair Procedures M1046983 04 08 9 29 The rear inverter A B C ...
Page 356: ...Notes 9 60 04 08 M1046983 ...
Page 401: ...10 Illustrated Parts M1046983 04 08 10 45 14 1 2 3 6 5 4 5 8 7 15 16 18 17 10 9 11 12 13 or ...
Page 452: ...Notes 10 96 04 08 M1046983 ...
Page 466: ...11 14 04 08 M1046983 Notes ...
Page 470: ...Aisys 12 4 04 08 M1046983 12 3 System Schematics 12 3 1 Power Schematic ...
Page 478: ...Aisys 12 12 04 08 M1046983 12 6 3 Tools Transfer Logs ...
Page 497: ......