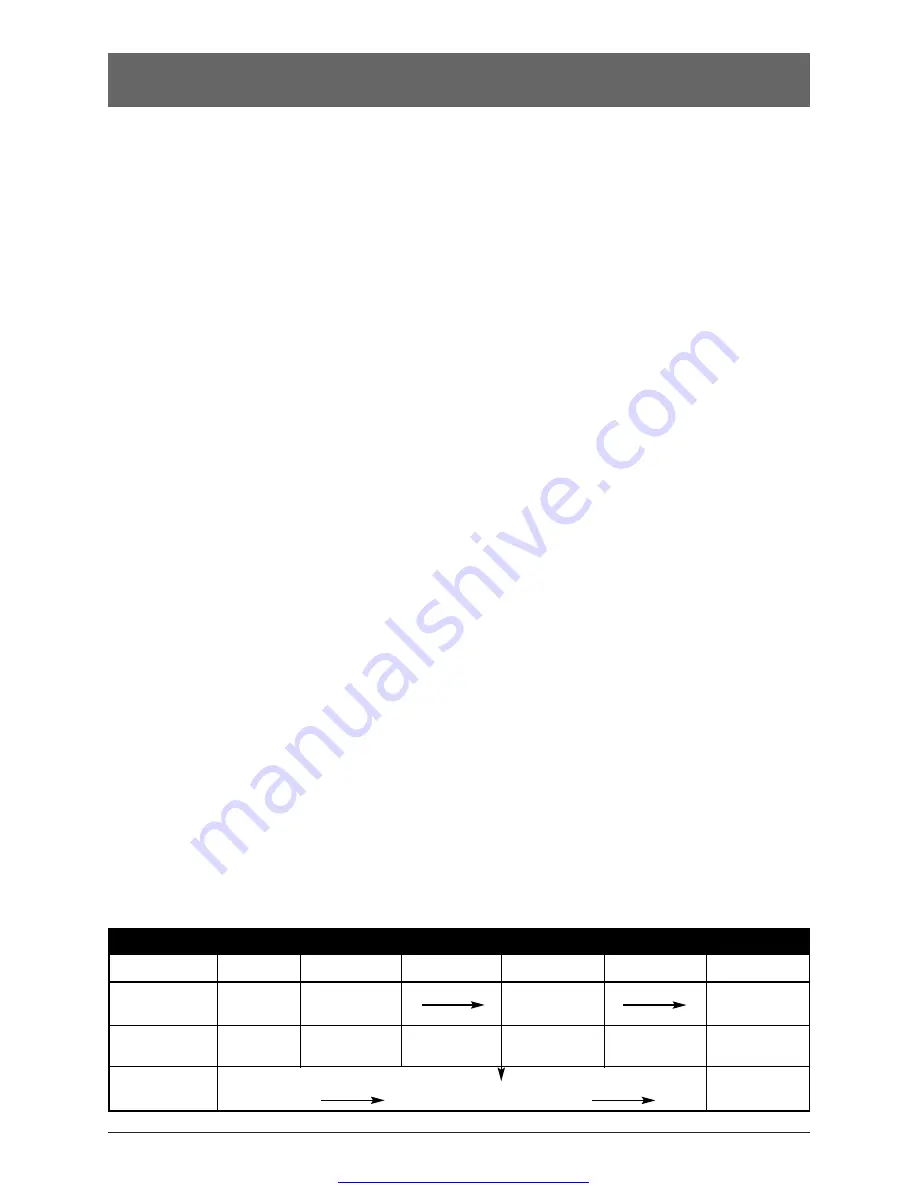
■
24
GE Zenith Controls
■
Entelli-Switch 250 Operation and Maintenance Manual (71
R
-2000)
Sequence of Operation
Standard Transition
Source 1 Power Failure:
When Source 1 voltage or frequency has fallen below
the preset "Fail" values, the controller initiates the Time
Delay Source 2 Start Timer (Engine Start Timer "P")
cycle. Upon completion of the (P) time delay, an
Engine start Signal is sent to Source 2. When Source 2
voltage and frequency reach the preset "Restore" Values,
the time delay to Source 2 Timer (W) begins its timing
cycle to ensure voltage and frequency stabilization
before transfer. A manual pushbutton BYPASS is provid-
ed to bypass the "W" time delay if desired. After the (W)
time delay, the CCE relay energizes the CE solenoid to
close the transfer switch in to Source 2. The SE limit
switch activates to de-energize the CCE relay.
Restoration of Source 1 Power:
When Source 1 power reach the preset "Restore" values,
the controller initiates re-transfer to Source
1sequence.The delay to Source 1 Timer (T) begins its
timing cycle to ensure voltage and frequency stabiliza-
tion before retransfer. A manual pushbutton BYPASS is
provided to bypass the "T" time delay if desired. After
the (T) time delay, the CCN relay energizes the CN
solenoid to retransfer the switch to Source 1. The SN
limit switch activates to de-energize the CCN relay.
Immediately after re-transfer, the S2 Stop Delay Timer
(Delay to Engine Stop "U") begins its cycle to allow
Source 2 Engine to run unloaded. A manual pushbut-
ton BYPASS is provided to bypass the "U" time delay if
desired. Upon completion of the (U) timing cycle, the
controller sends an Engine stop signal.
Delayed Transition
Source 1 Power Failure:
When Source 1 voltage or frequency has fallen below
the preset "Fail" values, the controller initiates the
Time Delay Source 2 Start (Engine Start Timer "P")
cycle. Upon completion of the (P) time delay, an
Engine start Signal is sent to Source 2. When Source 2
voltage and frequency reach the preset "Restore" values,
the time delay to open Source 1 timer (W) begins its
timing cycle to ensure voltage and frequency stabiliza-
tion before re-transfer. A manual pushbutton BYPASS is
provided to bypass the "W" time delay if desired. After
the (W) time delay, the CCNO relay energizes the CNO
solenoid to open the transfer switch out of Source 1
position. The time delay to Source 2 timer (DW) begins
its timing cycle. After the (DW) time delay, the CCE
relay energizes. The switch then completes transfer to
Source 2 by energizing the CE solenoid. The SE limit
switch activates to de-energize the CCE relay.
Restoration of Source 1 Power:
When Source 1 power reach the preset "Restore" values,
the controller initiates re-transfer to Source 1
sequence.The delay to open Source 2 Timer (T) begins
its timing cycle to ensure voltage and frequency stabi-
lization before retransfer. A manual pushbutton BYPASS
is provided to bypass the "T" time delay if desired. After
the (T) time delay, the CCEO relay energizes the CEO
solenoid to open the switch out of Source 2 position.
The time delay to Source 1 timer (DT) begins its timing
cycle. After the (DT) time delay, the CCN relay ener-
gizes the CN solenoid to complete re-transfer of the
switch to Source 1. The SN limit switch activates to de-
energize the CCN relay.
Immediately after re-transfer, the S2 Stop Delay Timer
(Delay to Engine Stop "U") begins its cycle to allow
Source 2 Engine to run unloaded. A manual pushbut-
ton BYPASS is provided to bypass the "U" time delay if
desired. Upon completion of the (U) timing cycle, the
controller sends an Engine stop signal.
Timer Designations as they appear in the SET menu
ATS Type
P
W
DW
T
DT
U
Standard
Time Delay
Time Delay
Time Delay
S2 Stop
Transition
S2 Start
S2 Stable
S1 Stable
Delay
Delay/ Open
Time Delay
Time Delay
ATS Open
Time Delay
ATS Open
S2 Stop
Transition
S2 Start
S2 Stable
Time to S2
S1 Stable
Time to S1
Delay
Source 1
Transfer to Source 2
Source 1
Transfer to Source 1
Engine
Fails
Returns
Cooldown
Table 3